Do you know what’s in your concrete?
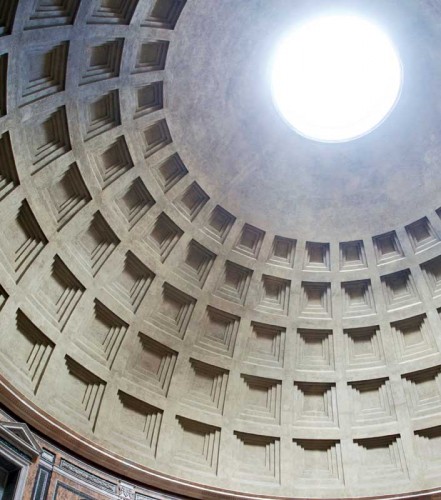
By Sherry Sullivan, MASc, P.Eng., LEED AP
From towering skylines and massive dams to modern bridges and centuries-old temples, concrete structures are the basis for much of civilization’s infrastructure and its physical development. Concrete is used worldwide, more than any other manufactured product—twice as much of it is used throughout the world than all other building materials combined. (See Bjørn Lomborg’s The Skeptical Environmentalist: Measuring the Real State of the World [Cambridge, 2001]). Each year, approximately four tonnes are used for every one of the nearly seven billion people on Earth. (This information comes from the 2009 U.S. Geological Survey). The world record for the largest concrete pour in a single project is the Three Gorges Dam in China’s Hubei province—the amount used is estimated at 16 million m3 (565 million cf) over 17 years. (“Concrete Pouring of Three Gorges Project Sets World Record,” an online article posted in January of 2001, comes from People’s Daily).
Still, as broadly as concrete is used, and as essential as it is to the built environment, people generally know very little about it. The material has evolved in many ways over the years; it is quite literally not your grandfather’s concrete.
Ingredients and environmental impact
In essence, concrete is a composite construction material containing aggregates and paste. The former makes up about 60 to 75 per cent of the total volume, while the latter comprises 25 to 40 per cent. In turn, the paste itself is made up of approximately:
- seven to 15 per cent cementing materials;
- 14 to 21 per cent water; and
- four to eight per cent air (in air-entrained concrete).
The quality of the concrete depends on the paste and aggregate, and the bond between them. In properly made concrete, every particle of aggregate—and all the spaces between—is completely coated or filled with paste. (See Steven Kosmatka et al’s eighth Canadian edition of Design and Control of Concrete Mixtures [Portland Cement Association, 2011]).
Admixtures are those ingredients in concrete other than portland cement, water, and aggregates that are added to the mixture immediately before or during mixing. Chemical admixtures are materials in the form of powder or fluids added to the concrete to give it certain characteristics unobtainable with plain concrete mixes. In normal use, admixture dosages are less than five per cent by mass of cement and are added to the concrete at the time of batching/mixing.
The common types of admixtures and a general description are outlined in this section. (For more, visit the U.S. Federal Highway Administration (FHWA) site, www.fhwa.dot.gov/infrastructure/materialsgrp/admixture.html).
Air-entraining admixtures
These admixtures introduce and stabilize microscopic air bubbles in the concrete, which improves concrete’s durability to freeze-thaw cycles. They also improve workability; segregation and bleeding are reduced or eliminated.
Water-reducing admixtures
Water-reducing admixtures reduce the quantity of mixing water required. They help:
- produce a concrete of a certain slump;
- reduce water-cement (w/c) ratio;
- lower cement content; and
- increase slump.
An increase in strength is generally obtained with water-reducing admixtures as the water-cement ratio is reduced.
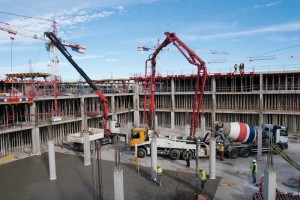
Photo © BigStockPhoto/Rob Wilson
Plasticizers
Plasticizers are a type of high-range water-reducing admixture used with concrete with a low-to-normal slump and water-cementing materials ratio to make high-slump flowing concrete.
Accelerating admixtures
These ingredients are used to accelerate the concrete’s rate of hydration and strength development at an early age.
Retarding admixtures
These admixtures delay the concrete’s rate of setting. They are useful in extending the setting time, but they are often also used in attempts to decrease slump loss and extend workability.
Hydration-control admixtures
Hydration-control admixtures consist of a two-part chemical system:
- a stabilizer or retarder that stops the hydration of cementing materials; and
- an activator that re-establishes normal hydration and setting when added to the stabilized concrete.
Corrosion-inhibitors
Inhibitors are used in concrete for parking structures, marine structures, and bridges where chloride salts are present. These admixtures chemically arrest the corrosion reaction.
Shrinkage-reducers
These admixtures are used where cracks and curling must be minimized for durability or esthetic reasons.
Colouring admixtures
These components can be used to change the colour of concrete for esthetic reasons.
Miscellaneous
Other materials include alkali-silica reactivity (ASR)-inhibitors and admixtures targetting areas such as:
- workability;
- bonding;
- dampproofing;
- permeability reduction;
- grouting;
- gas formation;
- anti-washout;
- foaming; and
- pumping.