DIALOG develops system to build 105-storey hybrid timber towers
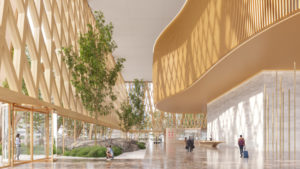
In what ways can this prototype aide architects, engineers, and planners slow down climate change, address global health crises, and improve the well-being of communities and the environment?
Applegath: We must all play a major role in addressing climate change and design, approving and building cleaner, healthier buildings. We designed this building concept not only to show what we can do as architects, engineers, interior designers, and landscape architects, but also to highlight what we must do in the future to meet our goals.
The technology we are showing in this prototype is not a “nice-to-have” but we think, going forward, a “must-have” if we are going to come to grips with the realities of climate change. For example, the use of an algae bioreactor as a way of sequestering the carbon dioxide (CO2) produced by burning natural gas to make heat and power is a hugely innovative made-in-Canada technology by Pond Technologies in Markham, Ont.
How does the prototype HTFS help meet a project’s sustainability goals?
Applegath and Khachi: Our patent-pending HTFS, with post-tensioned steel tendon in the CLT panels will allow for a 12-m, column-free span where standard CLT only spans approximately ¾ of that distance. As floor plates occupy approximately 70 per cent of building material in high-rises, our HTFS will maximize the overall use of sustainably harvested wood in high-rise construction.
Another sustainable system we designed includes the use of photovoltaics (PV). They would be deployed on the building façades, converting sunlight to energy for the facility.
Lastly, we would use a Canadian-made algae bioreactor to pull the carbon out of the boiler system and the co-generation plant.
Please provide more information on how this system allows the building of taller hybrid timber towers.
Wu: The high tensile steel cables encased in concrete bands embedded into CLT panels allows the HTFS to span an extra length, resulting in more spacious floor space. The HTFS is a prefabricated panel helping reduce onsite construction time. The non-combustible concrete band within the prefabricated panel provides the necessary fire safety. With these unique features, HTFS could be deployed in buildings of any and all heights. To seek patent protection internationally, DIALOG has filed an International Patent Application under the Patent Co-operation Treaty, applicable in over 150 countries.
What do you hope to achieve once this prototype design is adopted by AEC professionals?
Applegath, Wu, and Khachi: Our objective was to bring all of these innovations together in a way that could demonstrate the best method to create a zero-carbon building that can climb to great heights, scaling up our capacity for larger, hybrid timber, zero-carbon buildings.
We would like to thank the people and firms that collaborated in developing this prototype. EllisDon played a very important role in exploring and proving both the construction logistics and the costing of the HTFS. RWDI provided guidance and insight on how to best shape the building to deal with wind loading. Morgan Solar contributed their expertise in building envelope-integrated PV, and helped us model the power that could be generated. Pond Technologies worked with our mechanical and electrical teams to develop the CO2 sequestration strategy that will allow this building to generate heat and power from natural gas without emitting carbon dioxide.