Designing with insulated metal panels
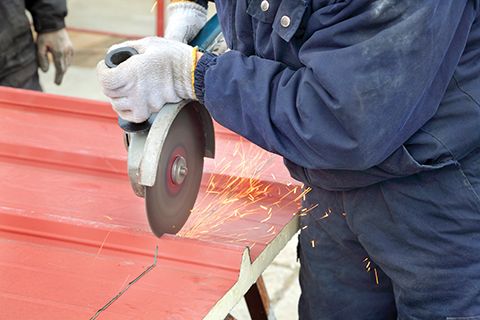
By John Straube, PhD, P.Eng.
Insulated metal panels (IMPs) have become increasingly popular in the last decade as a lightweight, prefabricated, total building enclosure system. Their strong, stiff, metal skins provide excellent water and air control. However, the joints between panels and the transitions to other components—especially windows, doors, roofs, and foundations—demand close attention. Discontinuities at joints and transitions are one of the most common causes of building failures, and this is especially true for designs using IMPs. Employing an appropriate approach to rainwater control will help significantly reduce this risk of failure.
The building enclosure is the component separating the indoor and outdoor environments. To perform its function, an enclosure must offer support, control, and finish functions. The control functions with the most impact on durability and performance are provided by the water, air, thermal, and vapour control layers. Ensuring these control layers are identified and provided in a continuous plane around a building by all involved in the design and construction process is a key to successful enclosure performance.
IMPs are composed of two thin layers of coated sheet metal wrapped around a rigid foam core to form a stiff composite. The metal skins act as the water, air, and vapour control layers, (In most cases, the interior steel sheet acts as the air and vapour control layer. However, in special circumstances [e.g. a cold storage building in a warm climate], the exterior sheet may be defined and detailed as the vapour and air control layer.) and, in many cases, the bare or coated metal also acts as the finish (Figure 1). Just as for any other enclosure, the most important control function is rainwater, followed by air flow, thermal, and vapour. For IMPs, the strategies most successful for rain control will also successfully control air flow and vapour, and each of these topics will be briefly discussed in turn.
Rain-control strategies
As controlling rain penetration is the most important function, it must be addressed first. There are three recognized design strategies to control rain penetration within and through the enclosure. (See this author’ piece [co-written with E.F.P. Burnett], “Rain Penetration Control: Applying Current Knowledge,” which appeared in the July 1999 Journal of Thermal Insulation and Building Envelopes, published by Canada Mortgage & Housing Corp.)
As shown in Figure 2, these approaches are:
- storage (or ‘mass’);
- drained (or ‘rainscreen’); or
- perfect barrier.

Building enclosures have been, and continue to be, designed and built successfully using all three strategies.
Storage
The oldest strategy, storage, assumes some rainwater will penetrate past the outer surface of the enclosure. It requires the use of an assembly of materials with enough moisture storage capacity and moisture tolerance (that is, sufficient ‘mass’) to absorb all rainwater that is not drained (i.e. shed) from the outer surface.
In a functional storage/mass wall, this moisture is eventually removed by evaporative drying from both the inside and outside before it reaches the inner surface of the wall as a liquid. Some examples of storage systems include adobe walls, thatched roofs, and multi-wythe brick masonry.
Drained enclosures
In the drained enclosure approach, it is also assumed some rainwater will penetrate the outer surface. However, rather than storing it, the assembly is designed to remove it by providing drainage. (The term ‘rainscreen’ is applied to some drained systems (since the cladding ‘screens’ the rain), but the term is imprecise, as it means different things to different people.)
Drained systems have justifiably received a lot of attention from researchers and practitioners. For many cladding types (e.g. brick veneer, siding, stucco), drainage is not just the most practical strategy, but it has also been the most successful system of rain penetration control.
While this approach can also accommodate a range of other claddings and backup systems, drained systems are not always an appropriate strategy. Insulated metal panels—as well as existing multi-wythe solid masonry walls, glazing panels, large-format precast panels, and low-slope membrane roofs—are examples of common enclosure systems that perform better when a rainscreen drained system is not used.
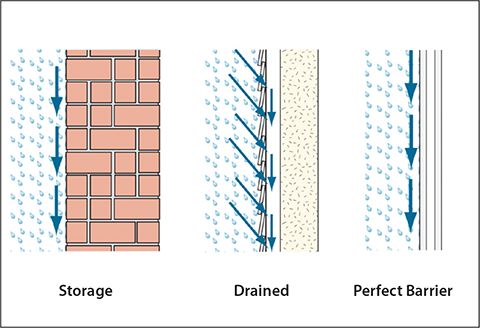
Perfect barrier
In a perfect barrier system, all water penetration stops at a single plane. These assemblies may be face-sealed (where the perfect barrier is at the exterior face) or concealed (where the barrier is protected behind other materials).
Some concealed barrier systems, such as protected membrane roofs (PMRs), have a long record of good performance. Others, such as stucco and adhered veneers applied directly over building paper, have shown disastrously poor performance in many applications. The difference in experience is directly related to the likelihood of a perfectly waterproof barrier being achieved in construction and maintained over the desired lifespan. It is difficult to build and maintain a perfect barrier with many materials, but some systems, usually factory-built, provide wall elements that are practical and durable perfect barriers.