Designing with foam plastic insulating sheathing
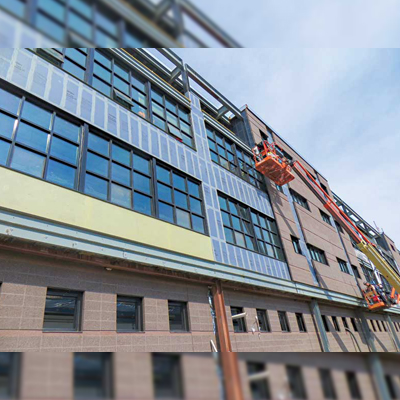
In general, the application methods for most FPIS systems are similar, with minor component-specific variations, such as the required fluid coating edge distances (e.g. 25.4 mm [1 in.] minimum onto pipe penetrations). Tape flashing products universally require a wider application than fluid flashings. Accessory products, including masonry veneer ties, are not incidental components, but rather coordinated components as part of an integrated assembly.
There are a few differences from one system to another for designers to be aware of. While many systems include both a fluid and tape accessory to provide flexibility, some manufacturers do not incorporate a tape flashing in their accessory line or allow for perimeter sealant application (i.e. at window openings) to occur over their fluid membrane at a cut edge. As a result, the system requires additional metal trim at the entire perimeter for every rough opening.
Additionally, certain systems will require special detailing at the fenestration head (e.g. mineral wool at a box beam) and/or fire-resistive treated wood blocking. This is especially critical where SPF is introduced into the system and there is a requirement to protect the SPF from exposure at the fenestration.
Applications
In terms of code requirements, the potential building applications are nearly limitless. That said, some applications are better than others, often those which capitalize on the efficiency of FPIS. Building designs featuring a low window wall ratio (WWR), such as data centers, cold storage buildings, and other industrial facilities, derive more value from FPIS systems than higher WWR designs. This is not meant to imply FPIS systems cannot be utilized for commercial, daylit buildings, however the return on investment diminishes.
Consider a single 1.22 x 2.44 (4 x 8) FPIS panel in an opaque wall. Where this panel abuts all opaque wall, it will contain 2.9 m2 (32 sf) surface area with 7.3 m (24 ft) of perimeter. All detail work (i.e. application of liquid or tape goods) to maintain barrier continuity occurs along the perimeter (in this idealized scenario with no penetrations). The efficiency rate of that panel (surface area/perimeter distance) will be
0.4 (1.33). The higher the rate is, the less detail work that is necessary. One can quickly extrapolate that for a simple rectangular box, more continuous opaque wall equals more shared perimeter joints, driving the efficiency rate up.
For contrast, consider a narrow panel utilizing a half-size standard board (2 x 8) between two fenestration openings. Examining the perimeter detailing of the panel only (and ignoring any impacts of specialized fenestration detailing), the efficiency rate tumbles to 0.24. While these are simplified scenarios, they provide a clear differentiation in terms of installation efficiency.
Cladding specific applications
Each manufacturer publishes their own test report outlining different overall wall assemblies viable with their FPIS. These reports outline numerous allowable cladding types, including, among others: masonry, metal panel, cement board, and stucco along with air/weather barrier accessories.
Masonry systems often require a single anchor style lateral tie plus solid cap washer to limit the penetrations through the insulation board. Thermally, these single penetration lateral ties outperform dual anchor lateral ties; however, they may limit installation tolerance when compared with a standard two-piece adjustable lateral tie. In addition, the single attachment point style of lateral tie inherently lacks the redundancy of a two-point system.