Designing with foam plastic insulating sheathing
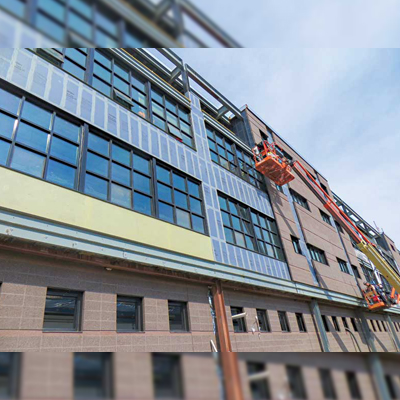
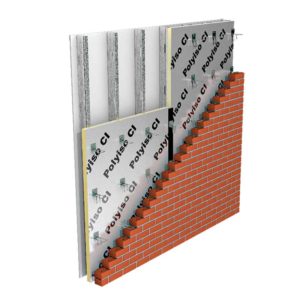
FPIS systems most commonly utilize expanded polystyrene (EPS), XPS, or polyiso insulation enhanced with appropriate facers to create multifunctional products for use in an exterior wall envelope (Figure 1). This article examines polyiso products due to their broad market adoption as an efficient, multi-functional barrier (thermal, air, weather, and vapour) and wall sheathing. Here, efficiency refers both to thermal performance relative to other common insulation types and the related material properties enabling polyiso to serve multiple wall enclosure functions, thereby minimizing necessary wall assembly thickness.
There is a direct correlation between building energy code requirements and the depth of a conventional wall assembly. A conventional 20th century cavity wall would typically include a cladding system (e.g. brick masonry), a 25 mm (1 in.) air space, and a wood or steel stud backup wall system, with all insulation provided in the backup stud wall cavity. As energy code requirements become more stringent, a conventional wall provides limited options to comply. Prescriptive code requires exterior continuous insulation5 (e.g. insulation outboard of the backup stud wall); this improves the entire wall thermal performance and also enhances cavity insulation performance, which is otherwise diminished due to thermal bridging effects at studs, especially steel studs.6
However, the insertion of continuous insulation creates an added dimensional thickness within the assembly previously unaccounted for in a conventional wall. This additional layer has a cascading effect on other wall components. It pushes the cladding further from the structure, which may trigger upgrades to the structural system, necessitate different wall accessories, and potentially reduce the building’s effective usable area. This is not to mention the potential impact to construction schedule associated with the additional exterior layer.
FPIS systems, which incorporate foil facers onto a polyiso board, maximize the R-value per inch relative to other foam insulations. With reported R-values of R-6.5 per inch, one would need to use 30 per cent more XPS (R-5.0 per inch) or 50 per cent more EPS (R-4.2 per inch for high density EPS) to construct an equivalent R-value wall assembly.7
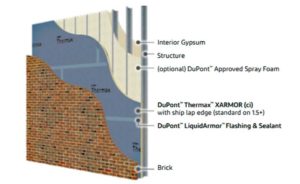
For a building with little flexibility in terms of wall depth, the space savings afforded by an FPIS system can be the difference between prescriptive code compliance and non-compliance. A valuable online resource is canadabuildingcode.dow.com, which allows the user to input basic building characteristics and receive corresponding exterior wall construction requirements specific to assemblies that may use foamed plastics in general, not just FPIS systems.
Wall assemblies featuring FPIS systems may be enhanced with cavity spray polyurethane foam (SPF). In the same efficient vein, SPF complements FPIS well. It is a highly efficient thermal insulation that also creates an effective air and vapour barrier and encapsulates the FPIS anchors, thereby minimizing thermal bridging and/or air leakage potential at board fastener penetrations.
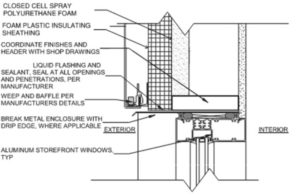
Detailing
Designing with FPIS requires some deviation from conventional wall detailing. Typically, one can differentiate between the field of a wall—which would be covered by a continuous fluid or sheet good—and the edges of a wall, where the more laborious detail work occurs. FPIS installation is essentially all detail work. The field of the board is manufactured with a foil facer; the foil itself provides an air and water resistive barrier. To maintain barrier continuity, every board edge must be detailed. Any penetration through the facer creates a deficiency that must be remedied, right down to the fastener washer. Anything other than a usually solid washer requires a patch.
The detail work incorporates a series of accessory products to create a continuous air and weather resistive barrier along the exterior surface of FPIS. These include fluid-applied flashings, self-adhered tapes, sealants, and/or spray foams, among other products. Figure 3 illustrates one manufacturer’s basic FPIS wall assembly, with a trowel-applied fluid over all board joints.