Designing vegetated roofing for wind forces
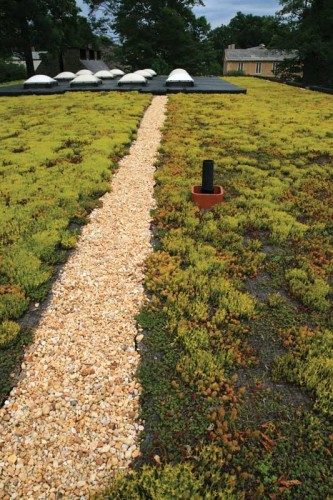
By Jeff Truman, M.A.Sc., P.Eng., PMP
From a purely economic perspective, the positive impact of a vegetative ‘green’ roofing assembly is measured in the long term—40 years or more. This means ensuring its performance and safety over an extended period is crucial.
A green roof protects the underlying waterproofing membrane from the elements. Combined with a higher-quality membrane necessary to resist soil and plant forces, the result should be a longer roof lifecycle decades beyond a conventional system’s 20 to 25 years. This suits institutional real estate owners, such as schools and governments. In this author’s experience, vegetated roofs cost about twice that of a traditional assembly; this is why membrane replacement for these roofs should have double the lifespan of a traditional roof to achieve the economic benefits.
The environmental benefits of green roofs are less quantifiable. They include reducing the urban heat island (UHI) effect, adding insulation to minimize energy consumption, and improving the urban esthetic, especially for those with access to these spaces.
To achieve these intangible benefits, legislation is often required. The City of Toronto became the first major municipality in North America to mandate many new developments (i.e. those larger than 2000 m2 [21,528 sf]) to include up to 60 per cent of the roof area as vegetated. The rules allow industrial buildings to instead have a cool roof (i.e. reflective or white-membrane), as they are often in areas away from residential and office areas, and the esthetic benefits are lower.
There are no real indications green roof legislation may come to other large-scale municipalities in Canada—Toronto’s condo market may be the only one large enough to support such an initiative—but the basic lessons and best practices could certainly be applicable in many of the provinces.
Code requirements and standards
Introduced in May 2009, Toronto’s green roof bylaw (Toronto Municipal Code Chapter 492, “Green Roof”) has created a market driver for vegetated assemblies in Ontario. However, Act IV of the bylaw—Toronto Green Roof Construction Standard—provides little guidance with respect to the structural implications. It requires a wind uplift study be completed by a professional engineer and, as with all developments, landscape/architectural/structural drawings and specifications for all building areas and systems, including the green roof.
For structural design, the standard refers primarily to the Factory Mutual (FM Global) Data Sheet 1-35, Green Roof Systems, which was prepared from a loss prevention perspective. Those aspects are discussed further below, and they arise naturally from the current state of knowledge.
The Ontario Building Code (OBC) does not specifically refer to green roofs. However, it speaks to wind design for building systems and cladding components. Claddings are attached to the main structure, and experiences higher local wind forces due to their location and air turbulence. When it comes to wind design, OBC refers to National Building Code of Canada (NBC) Design Supplement, Commentary J. This resource provides equations to support OBC notations, and graphic representations of buildings with wind force co-efficients that have been developed via wind-tunnel tests, and statistically verified by reviewing building failures.
Proceeding with a wind design on the basis of OBC is therefore quite straightforward. What results, however, is a requirement the green roof’s growing medium be of a depth and density that increases the assembly’s costs and structural needs. Anecdotal evidence and testing on wall assemblies have shown vegetated roofs may not experience the full uplift forces due to ‘pressure equalization’—wind is drawn through, rather than adhered to, the material, reducing suction forces.
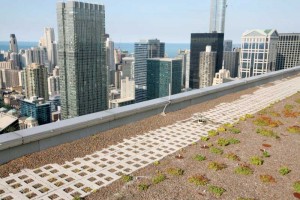
Photo courtesy LiveRoof
Other standards, such as American National Standards Institute/Single-ply Roofing Industry (ANSI/SPRI) Recommend Practice (RP) 14-2010, Wind Design Standard for Vegetative Roofing Systems, pertain mostly to the vegetated system itself. This standard is intended to develop consistency in the product and allows one to be compared to another. For example, the test for growing medium density is based on a ‘kiln-dry’ mass, which would not occur onsite. Therefore, it is inappropriate to use this mass for design purposes, as the growing medium would never reach ‘kiln dry’ (unless installed in a desert area). The mass is more useful to compare the growing medium quality from one product to the next.
ANSI/SPRI RP 14-2010 refers generally to American Society of Civil Engineers (ASCE) 7, Minimum Design Loads for Buildings and Other Structures, which is the wind design standard for the International Building Code (IBC) used in the United States. Canadian codes already perform wind design in accordance with this standard, but use design pressures instead of wind speeds. Regardless, OBC/NBC uplift forces govern, but there is no real guidance to any reductions due to surface irregularities or substrate permeability. Essentially, the ANSI standard does little to enhance the state of knowledge, but simply collects information directly pertaining to vegetated roofs.
As mentioned, FM Global has developed a green roof design and installation guide that generally describes ways to limit the possibility of an insurance loss. The document is written from FM’s perspective, showing the firm has seen green roof failures, and understands the causes. Therefore, it could be argued the specific issues raised by FM are the overriding concerns facing the design of vegetated roofs today.
In addition to the bylaw, the City of Toronto provides design guidance with its supplemental design guide, which mainly speaks to the horticultural issues; the section relating to wind design is based primarily on the FM guide. The City guide refers to the development of another standard, one by Green Roofs for Healthy Cities (GRHC), but this is the aforementioned ANSI one.
Design issues
Following the OBC/NBC method, there is a perimeter zone (size depending on the building dimensions) around the edge that experiences much higher wind loads—about 50 per cent higher than at the rest of the roof area. The corners experience even greater wind forces. This is due to turbulence at the roof edge, and a sudden expansion of the air compressed up the wall. In many designs, the increased wind load results in no plantings at the edge zone, due to weight concerns and the ability of the growing medium to resist scour (i.e. the removal of dirt or stones by wind). The FM guide recommends keeping this edge zone free of plantings to limit losses due to high winds.
The soil can be as deep as necessary to resist the wind uplift forces—this depends on both the expected winds (the lower the building, the lower the wind speeds and uplift) and the composition of growing medium. However, if it is not a contiguous mass, there is concern for scour to remove the soil. If this process occurs rapidly, the entire ballast could be removed. It is therefore essential the plantings are fully rooted, or some means have been provided to ensure the soil mass is contiguous or secured.
Piles of dirt on the ground do not suddenly blow away—there is some cohesion of the soil to hold itself together. Tornadoes do not regularly lift dirt off the ground, for example, at least not beyond the loose layers. However, sand dunes move. In other words, the amount of movement depends on the soil composition. When it comes to vegetated roofing, this author feels there is not enough guidance in this respect.