Designing the virtual air barrier
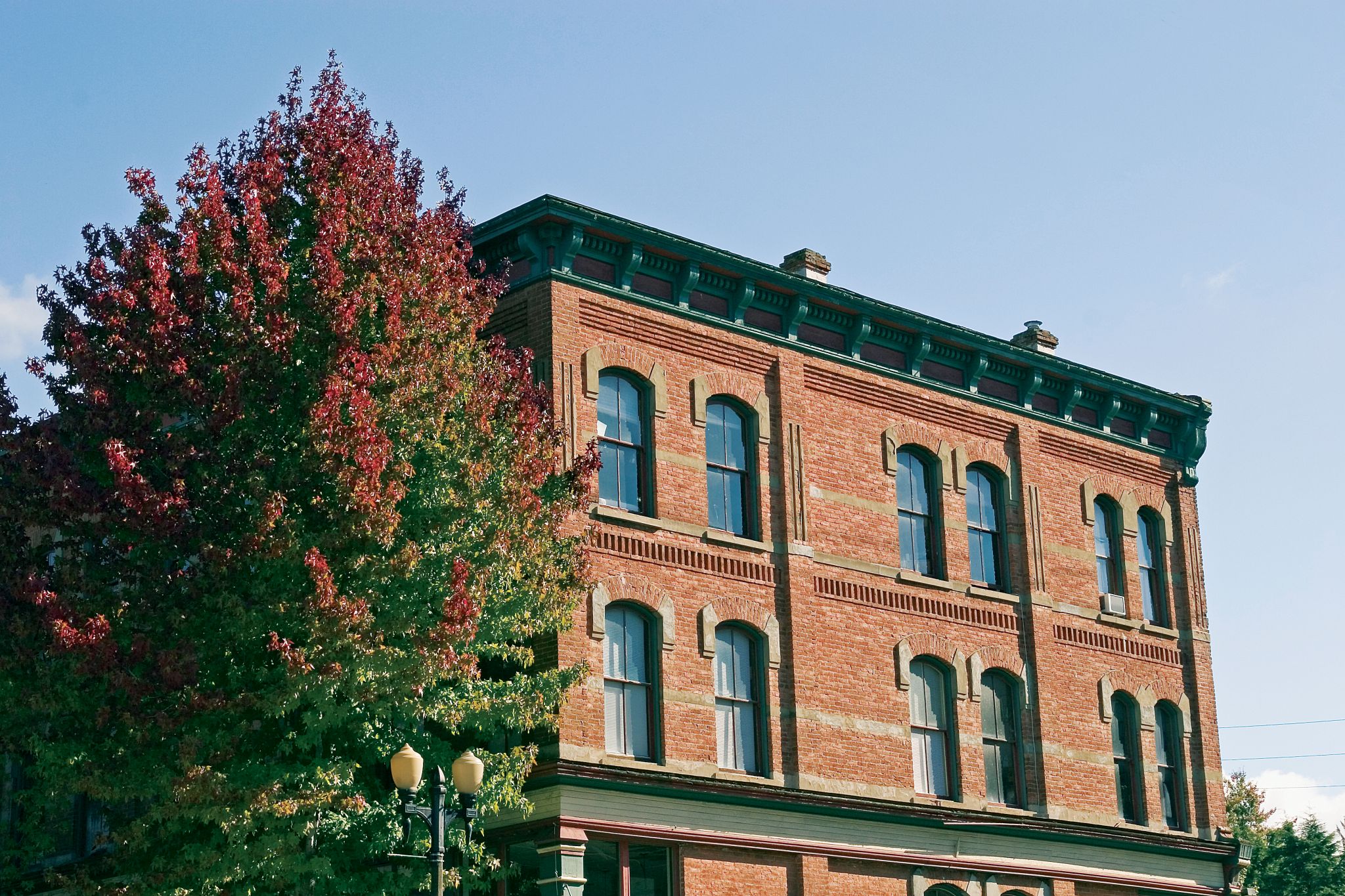
By Rick Quirouette, B. Arch.
Since 1985, the National Building Code of Canada (NBC) requirements for an air barrier system have been adopted for all buildings in this country. While the air barrier concept is widely accepted by industry, its application can be particularly difficult and challenging when it comes to structures predating that code.
With just over 25 years of this technology’s development, there remains a large proportion of existing buildings that have no air leakage control (i.e. no air barrier system). The problem is these facilities are subjected to various types of conversions (e.g. factories converted to condominiums) and mechanical upgrades to include new ventilation and humidification equipment without a complementary building envelope upgrade. These include many older (and some newer) hospitals, museums, schools, offices, apartments, and heritage buildings.
The provision of an air barrier system for existing buildings is technically difficult and costly to incorporate. For this reason, the concept of a virtual air barrier (VAB), or dynamic buffer zone (DBZ), has been applied, tested, and researched over the last decade by this author and the late Michel Perrault. It has been applied fully, partially, or as a feasibility approach to 13 building projects in Canada.
Anatomy of a VAB
The VAB concept involves the creation of a pressure zone (or cavity) within the roof, exterior wall, window (older double pane windows, not sealed units), or below-grade construction of a building. This pressure zone has no material substance (hence it being ‘virtual’), using the attributes of the existing exterior wall or roof to construct part of the VAB system. The pressure zone must be adequately sealed to contain an increased pressure between the zone and the building interior.
To pressurize a VAB zone, a fan, ducts, and an optional in-line heater are required. The pressure zone is supplied with outdoor air, pre-heated if necessary, and pumped into a wall or roof cavity. By adjusting the VAB supply air fan speed, the air pressure within the zone is forced to rise slightly above the indoor air pressure. This situation then prevents moist, indoor air from entering the VAB zone of the exterior walls or roofs.
Figure 1 illustrates the concept as it is applied to an exterior wall or roof cavity. There is no return circuit for this pressurization (ventilation) system, as it would be detrimental to the VAB operation and add considerable cost. It must not be viewed as a cavity ventilation problem, as this approach has been found problematic or, in some cases, disastrous.
A VAB system may comprise many different components, but it generally uses the existing roof or exterior wall components to define a pressure zone. This zone may be inboard of the wall or roof insulation or outboard of the insulation. It is this zone (i.e. cavity) that is pressurized to create a positive pressure with respect to the indoor side of the room. Parts of the exterior cladding, or where there are large openings or holes on the indoor side, may need to be air-sealed. Small cracks, openings, or holes do not significantly affect the VAB system’s performance.
For the VAB to correctly perform, the cavity must be pressurized with dry air from outside—not indoor spaces, elevator shaft exhaust, or mechanical rooms. This is because the VAB supply air must have a dewpoint temperature (i.e. air temperature when condensation occurs) below that of the outdoor air temperature. In this way, the pressurization air can never condense in the VAB zone or anywhere in the roof or wall cavities, behind claddings, or below roof membranes.
The VAB zone pressure is supplied by a small pressurization system designed to function continuously over a period of five to seven months. The VAB zone pressure difference between the zone and the indoor side need not be large, but it must be sustained. In this way, the moist indoor air is prevented from entering the roof or exterior wall cavities. The VAB system then reverses stack effect and building ventilation pressure differences at exterior walls, window, and roof systems to prevent air exfiltration at the outside wall and roof.