Designing hybrid insulated walls to combat climate change
by Rockford Boyer
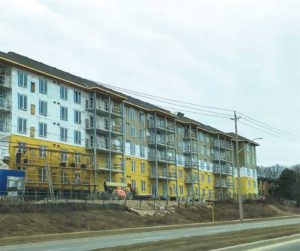
Canadians are used to cyclic weather patterns, and are becoming familiar with catastrophic weather events like flooding and high winds, thanks to their frequent occurrence. In the past decade, though, there has been an obvious increase in severe unpredicted weather events. Figure 1 indicates the increased cost to insurers due to weather-related damage. The damage arising from more frequent extreme weather conditions averaged $400 million a year between 1983 and 2008. This increased to $1 billion a year between 2009 and 2013. This article is not going to debate the reason for these increased weather events, but aims to provide guidance for reduction in carbon emissions in the insulation industry and increase the durability/resiliency of insulated building enclosures.
A recent article in the Toronto Star suggested $1 out of every $2 provided to property insurance is set aside for moisture-related issues within buildings. Other studies from the U.S. Department of Energy (DOE) and independent remediation experts claim 85 per cent of buildings will eventually leak and be responsible for 70 per cent of the construction litigation. With staggering statistics like these, there should be a greater requirement for water and moisture resiliency within the building’s design and operation.
In the author’s experience, the industry appears to believe fire-related disasters are more prevalent and costly than those associated with weather-related damage, especially after the fatal Grenfell Tower fire in the United Kingdom. However, building science professionals, remediation experts, and insurance companies are demonstrating moisture has a far greater potential for damage than building fires. The author agrees fire safety is an important design consideration. Nevertheless, the trend in fire-related building fatalities and damage is trending downwards (25 per cent in the last 10 years), while moisture- and wind-related building damage is on a severe upward trend (2.5 times greater on average in the past 20 years).
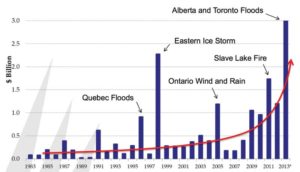
Resistant materials
There are several documents available currently to assist the industry with the design of flood-resistant buildings. One such document is the Federal Emergency Management Agency (FEMA) Technical Bulletin 2, Flood Damage–Resistant Material Requirements for Buildings Located in Special Flood Hazard Areas in accordance with the National Flood Insurance Program. To ensure durability and resiliency of building enclosures, it should be recommended or become code for all new buildings to comply with the flood-resistant material requirements specified in this document. The suggestion for all buildings to adhere to it is based on several factors such as:
- increased density/urbanization;
- reduction of water absorbing softscapes;
- aging/outdated infrastructure;
- increased flooding potential; and
- impacts from climate change.
Table 1 of the technical bulletin describes five classes of building materials according to their resistance to flooding. Table 2 of this document will be useful for designers as it provides generic material names and their applicability to the building enclosure as well as resistance to flooding, prolonged water exposure, and after recession of water. In general, the document states materials below grade and at a reasonable elevation above grade should be designed with completely water-resistant materials and insulated with only closed-cell foam products. Closed-cell foam is resistant to flood waters and can be adequately cleaned during a wetting event, whereas fibrous products can act as a filter and potentially trap hazardous pollutants.
Severe wind events are listed as the second largest driver of property damage in the country, just behind water. The lighter the buildings (in terms of structural design) the more susceptible they are to damage from wind, especially during the construction phase. Figure 2 shows a structure in Southern Ontario that collapsed during the May 2018 windstorm, which caused more than $380 million in insurable damage claims.