Designing with engineered wood products
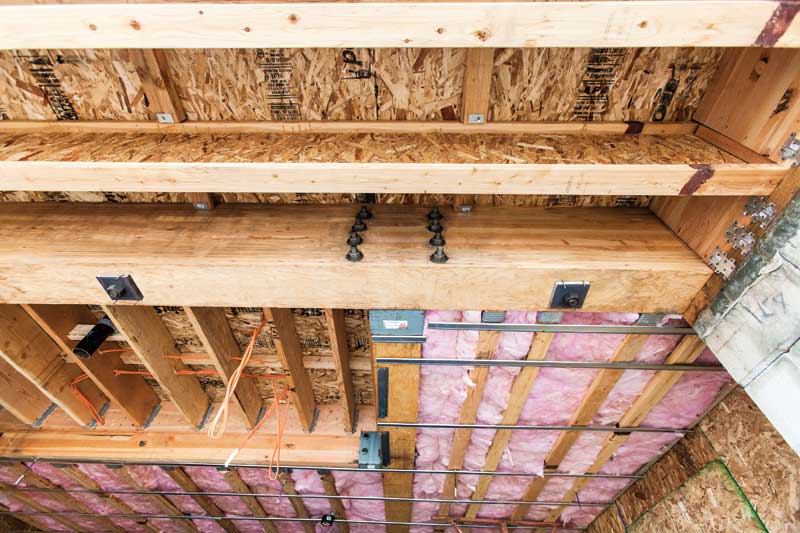
Photo courtesy West Coast Aerial Photography
The OSB wall assemblies enable the building designers to take advantage of the lateral and shear capacities of wood structural panels. Continuous wood structural panel sheathing contributes to a structure’s ability to handle uplift loads, lateral loads, and wind pressures. It also provides flexibility when bracing wall segments that have window and door openings. The engineered shear walls are also designed to resist seismic and wind forces—important considerations on the West Coast.
In all, 2400 sheets of OSB were used for the exterior sheathing, and another 3000 panels were employed for shear walls throughout the project.
“We used OSB in almost every party wall and every corridor wall,” explains Adam Weir, GSC, senior project manager with Adera. “On the lower floors, we used OSB in double-sided shear walls.”
All the OSB sheathing was 15⁄32 Performance Category thickness. (The Performance Category designates the panel thickness range that is linked to the nominal panel thickness used in the building codes. In this case, it is 12 mm [15⁄32 in.].) Weir noted OSB was the most cost-competitive material to meet the structural requirements of the exterior walls and shear walls.
Adera’s design included unique connections detailing where the shear walls were tied to the CLT floors.
“We use only one top plate and one bottom plate in the wall design,” says Weir. “This allowed for the plates to be nailed from the underside of the plate up to the CLT and from the bottom plate down to the CLT.”
While meeting these important structural requirements, the engineered wood and mass timber products also provide enhanced design flexibility and the esthetic advantages of a wood structure.
“The Virtuoso project is an excellent example of how we are fundamentally changing how residential and multifamily housing is being built,” said Stephen Tolnai, a director with the manufacturer of the CLT used on the project. “We’re using new wood building materials and systems in efficient, cost-effective ways, in developments that meet the criteria of discerning homebuyers. They are getting that feeling of the strength and mass of having all this timber around them. They have a healthy home. They have a quiet home.”
The mass of the CLT panels give the floor has a solid feel, similar to what one would expect with concrete. The acoustical benefits of sound-absorbing timber can be recognized even when walking on the CLT immediately after installation, and before the ceiling assembly and acoustical matting is installed.
A Canadian study that evaluated the biophilia effect in building materials showed wood in interiors was perceived by a majority of subjects as more “warm,” “inviting,” “homey,” and “relaxing” than all other tested materials. (The study was summarized in a 2006 issue of Wood and Fiber Science [38(4)], published by the Society of Wood Science and Technology. The article, “Appearance Wood Products and Psychological Well-being,” by Jennifer Rice, Robert Kozak, Michael Meitner, and David Cohen, can be read at www.woodworks.org/wp-content/uploads/Appearance-Wood-Products-and-Psychological-Well-Being.pdf. For more information on biophilia, visit www.apawood.org/designerscircle-nature-in-design-the-biophilia-effect.)
Podium construction
Mid-rise podium construction, consisting of two to five residential storeys of wood framing above a concrete nonresidential first storey (i.e. the podium) is common throughout North America, and current trends for urban living have led to a greater demand for podium structures. Designers can take the concept a step further by using wood instead of concrete for the podium. Engineered wood podium design can reduce overall construction cost and construction time, while creating a more sustainable and less massive building.
Examples of two U.S. wood podium projects are the Oceano Luxury Apartments and Galt Place buildings in California. In both cases, the podiums are composed of gypsum concrete topping over wood structural panels supported by I-joists and glulam beams; the former vary in size from 130 to 311 mm (5 1⁄8 to 12 1⁄4 in.) wide and 273 to 1143 mm (10 3⁄4 to 45 in.) deep.
Galt Place specified one stress class: 24F-1.8E (2400 psi bending stress, 1.8×106 psi modulus of elasticity), while Oceano specified two: 24F-1.8E and 30F-2.1E glulam. The 30F-2.1E stress class is considered a high-strength composite (HSC) glulam, in which the beam’s structural properties are increased by replacing the sawn lumber tension lamination with high-strength LVL. Steel beams were an early consideration for both design teams, but were found to be more expensive. Steel columns were used to support the glulam girders with custom steel saddles designed for both projects. As the glulam beams are deeper than typical stocked sizes, it is essential to consult a manufacturer in advance to ensure availability of the materials when needed.
Both project teams were comfortable with the overall durability of wood podiums, as they provide a building envelope that does not expose the wood members to the environment. Oceano further protected the wood elements with drywall, fibreglass mat gypsum sheathing, and stucco on all subterranean wood surfaces, including the shear walls. The Galt Place designers took a different approach, leaving the glulam exposed for the esthetic appeal.