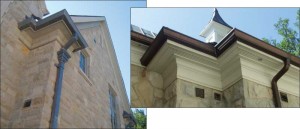
Pergola possibilities
Beyond columns, compact cellular PVC is being employed to create pergola structures. The flexibility of cellular PVC allows creation of curved structural components that would normally have required lamination of multiple pieces of wood. By substituting cellular PVC in place of traditional forest products, one can fabricate structural members with an 11- or 12-degree arc to form the top section of a 3 x 3-m (10 x 10-ft) pergola. Additionally, custom-ordered cellular PVC beams have enough stiffness to make the structure stable, once they have been interlocked together and the joints have been chemically bonded.
For example, in larger (e.g. 3.7 x 3.7-m [12 x 12-ft]) custom-fabricated models, the cellular PVC material can be laminated around an aluminum core to form beam structures that meet the required structural performance standards. Electrical conduit can be incorporated within these beam structures to allow for the installation of lighting.
In one particularly challenging application, the authors designed a pergola that would hold a 113-kg (250-lb) lighting fixture. For structural support, 25 x 102-mm (1 x 4-in.) aluminum tubing, which formed the core of the 51-mm (2-in.) thick and 254-mm (10-in.) high beams, was concealed, along with a 19-mm (¾-in.) diameter cellular PVC electrical conduit within the beam.
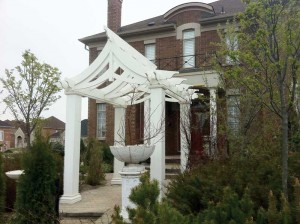
When it was assembled onsite, the pergola components were tied down to structural steel posts, and the steel posts wrapped in PVC column surrounds. All electrical wiring ran within the beams and columns, and ultimately to the fixture’s electrical box. When complete, the lighting fixture was successfully hung, and the pergola, which was built on a lakefront site subject to significant winds, met all provincial requirements pertaining to load and uplift.
Trellises and gables
Trellises can be extremely labour-intensive to create; in their traditional form, they require milling and handling of wood, which impacts the final product’s cost. When cellular PVC was first used for this application, it meant spending a great deal of time laminating two pieces of trim together to arrive at a 38 mm (1 ½ in.) nominal, which resulted in a finished size of 31.75 mm (1 ¼ in.).
All this lamination required priming and painting before shipping (adding yet more expense). With customization capabilities, newer cellular PVC products can be ordered in the correct sizes to begin with, eliminating milling and lamination, and making it nearly impossible to identify seams and joints.
A Canadian big box store provides blueprints and lumber kits to builders across the country. About 5000 houses are built from these kits each year, and many of them feature at least some type of gable detail. In years past, these architectural elements were made at the building site, using a drawing supplied in the kit as the production guide. The elements were typically made out of plywood or pine, and often did not weather well over time due to the porous nature of the materials.
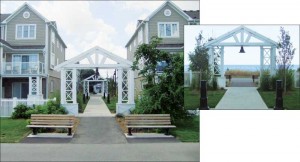
The company knew of PVC products that could be substituted to avoid decay and onsite fabrication problems, but decided one-piece units were costly and difficult to ship. However, a solution was found in a cellular PVC gable detail with a tenon joint that could be easily assembled onsite. Each gable detail was drilled with predetermined holes that were already pre-cored. This allowed the gable to be mechanically fastened from the back, without any mounting hardware being visible. The best features of these gable details were their finish and appearance. Unlike their wood predecessors, there was no variation in dimensions or composition. As a result, there was no need to use drum sanders or to fill open edges. The finish was pristine right out of the box, so the gable details could be left in PVC white or painted to match a selected colour scheme.
From the gable details, a wide variety of other architectural elements made from cellular PVC—many of which are intricately tooled—were offered, including louvres, shutters, brackets, pilasters, dock boxes, window surrounds, and planter boxes. Since many of these elements are installed in high, difficult-to-reach locations, eliminating the prospect of rot and decay—not to mention painting —helps owners reduce maintenance costs and preserve the architectural detail.
Conclusion
Cellular PVC is making the cost of adding high-end architectural details attainable for more projects that face small budgets. With traditional materials, the time spent on sanding and finishing was incredible when it came to fashioning brackets. Now, architectural pieces are essentially ready to go within minutes after they have been shaped and finish-sanded.
Bill Hutt is president of Decor Innovations and Distinctive Rail, and has more than 25 years of construction and renovation experience. Décor Innovations is a supplier of trimboard and a producer of millwork products, while Distinctive Rail is a provider of railings and columns. He can be reached at billhutt@decorinnovations.ca.
John Pace, PE, is president and chief operating officer of Versatex Trimboard. He has more than 20 years of experience in the design, development, production, and installation of rigid and cellular vinyl building products for residential and light commercial applications. Pace is also a founder of Wolfpac Technologies, an extruder of cellular PVC sheet and board materials that has been serving the building products industry since 2003. He can be reached at jpace@versatex.com.