Designing and specifying zinc wall cladding systems
Joints and sealants
Zinc has a high coefficient of thermal expansion and should have accommodations in the design to allow for movement. Caulking often is not required at these critical junctures, helping to lower initial and lifetime costs, and to reduce recurring maintenance.
The first consideration at any joint should be how to achieve the detail minimizing the use of solder or sealant. Sealants can limit airflow or trap moisture behind the zinc panels and decrease the panel’s lifespan. If soldering is essential, choose one that does not contain lead, cadmium, or copper to maintain zinc’s environmental material attributes recognized by LEED and other green building programs.
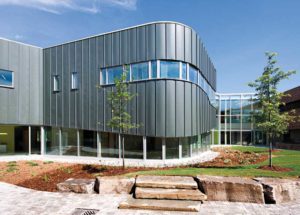
Resilience and longevity
Installed properly, zinc cladding systems will resist air and water infiltration. For regions with high winds and hurricane conditions, zinc wall systems have been tested to withstand high winds as required by codes and local jurisdictions. In environments which are susceptible to fires, zinc also provides a non-combustible solution.
Zinc’s inherent metallic properties allow the material to deliver low-maintenance and long-lasting performance in wall cladding applications. No paint, varnish, or sealants are required. Runoff is minimal, non-staining, and does not adversely affect the environment as the zinc material’s patina naturally forms.
Patination process and appearance
Mill-finish architectural zinc starts with a bright surface. However, most architects and specification professionals select zinc for its future patina appearance. Like copper, zinc develops its distinctive patina, or surface crust, based on the alloy composition and local environmental conditions.
The patination of architectural zinc occurs through a two-step chemical reaction. First, the zinc combines with water and oxygen to form zinc hydroxide, and then with carbon dioxide in free-flowing air, the zinc generates a dense outer layer insoluble to water and a packed inner layer of alkaline zinc carbonate.
A patina’s formation is a process of the gradual growing together of zinc carbonate “freckles” and the rate of its formation is related to the slope of the surface. The patination will be slower on a vertical wall surface than on a slightly sloped one. Its speed can vary between six months and five years or more, depending on climatic conditions. The more exposure to wetting and drying cycles, the quicker the patina will develop.
While the basis of the patina is alkaline zinc carbonate, additional substances are incorporated from the local humidity, rainfall, snowfall, and air pollution levels. Therefore, the colour of the patina can vary from one place to another. The natural patina will appear lighter when used in marine locations where the air contains chlorides. When used in environments where sulfur levels are higher, the patina may appear somewhat darker. In marine environments, lighter colours of architectural zinc will not show salt deposits as much as darker surfaces. For esthetic reasons, lighter surfaces are often chosen for coastal applications.
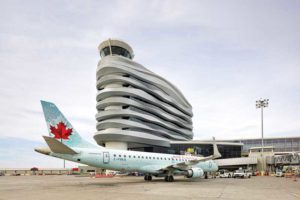
After the true patina has fully formed, the process will slow down, but it never stops. The natural patina will form to a soft blue-grey or graphite-grey colour, depending on the alloy type. To achieve this vintage look at the time of installation, some architectural zinc manufacturers can accelerate the patination process under factory-controlled conditions before the material is fabricated into wall cladding.
Additional colour and coating options for zinc wall cladding include:
∞ Pickling—a pre-treatment process which chemically etches the metal and derives the colour from the alloy. The resulting appearance brings out the metal’s natural grey colour and subtle grain texture.
∞ Phosphating—a treatment where phosphate crystals are deposited on the surface to create a darker colour from the titanium or copper alloy. The resulting colour is produced by the durable phosphate coating, which looks like the zinc structure of natural patina.
∞ Colour coating—a finish applied to the zinc that seals the metal with a selected colour during its manufacturing process. The resulting colour is imparted by the coating.
While coating the zinc surface will delay the visible patination process longer, all these colouring techniques will eventually fade and give way as the material continues to naturally weather and form its patina.