Demystifying self-consolidating concrete
Construction with SCC
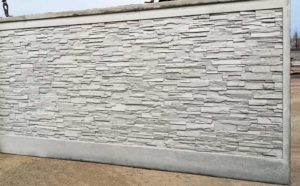
Photo courtesy Lehigh Hanson
From the contractor’s perspective, the keys to ensuring proper placement of SCC include:
- confirming the proposed mix design is appropriate to the actual project prior to ordering;
- selecting an appropriate delivery rate and time with the concrete supplier;
- ensuring placement methods do not result in harmful segregation due to excessive free-fall heights, poor pump configuration, etc. (SCC should be deposited continuously and in layers);
- documenting and clearly communicating jobsite acceptance test methods and results as well as change requests;
- ensuring the placement crew is familiar with the material and that the formwork is properly designed and constructed;
- levelling (screeding or low-level external vibration) and finishing operations, if necessary, are proper; and
- providing adequate protection and curing for the concrete mix.
Due to the relatively low w/c ratio, it is imperative SCC is properly cured to allow the hydration reaction to continue and avoid self-desiccation of the concrete.
Additionally, the formwork must:
- support the weight of the material (considering placement rates and both full liquid head conditions and thixotropic effects);
- be clean and free of debris and imperfection with a properly applied, high-quality form release agent to provide the required surface finish;
- properly secure the embedded items; and
- be sufficiently tight to avoid leakage of mortar or paste (Figure 7).
For information on best practices, one can refer to the “Best Practices Guidelines for Self-Consolidating Concrete” from Concrete Ontario and ACI 237.
Sustainability of SCC
Concrete is a sustainable and resilient building material. SCC offers a high-performance product with many benefits. Use of high-performance concrete for structural elements can result in smaller members that are better able to resist stresses with long-term durability and thus less overall material consumption. Additionally, due to the excellent placement properties of SCC, most projects realize reductions to noise, truck turnaround time, vehicular emissions, risk of injury or strain, and project completion time due to faster construction. Finally, with advancements in admixture technology, Portland limestone cement, and use of supplementary cementitious materials and mineral fillers, SCC mix designs can easily be optimized by the producer to achieve reductions in the material’s carbon footprint, quarried material consumption, and embodied energy.
Ottawa National Holocaust Monument
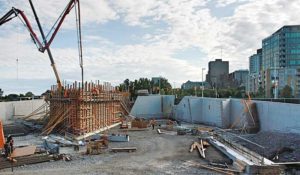
Photo courtesy Hanson Ready Mix
The National Holocaust Monument in Ottawa honours and commemorates the victims and survivors of the Holocaust. The monument stands on a 0.4-ha (1-acre) site in the city’s downtown and is comprised of six triangular concrete elements configured to create the points of a star.
Poured in 2017 and winner of the Concrete Award for Architectural Hardscape, the project incorporated more than 8361 m2 (90,000 sf) of custom-engineered formwork for walls with complex geometries, reaching heights varying from 3 to 20 m (10 to 66 ft). Over 3000 m3 (105,944 cf) of concrete was used, of which more than 1000 m3 (35,315 cf) was 35 MPa (5 ksi)- C1 exposure class SCC employing Portland limestone cement and 60 per cent slag replacement, resulting in a lighter colour, and approximately a 64-per cent reduction in the carbon footprint of the cementitious component as compared to a straight Portland cement mix. The extensive use of SCC was chosen due to its high performance, durability, and flexibility, allowing for smooth and even flow into the forms and a superior exposed architectural finish.
Conclusion
SCC offers a flexible, high performing, and sustainable product that can be easily placed. However, it is important to have a solid understanding of what the product is doing and respect and treat it accordingly. A little extra planning, forethought, and communication between all parties involved is critical to a successful project. The quality of a project also depends on the whole concreting system from the specification, raw material selection, and mix design to batching, delivery, proper construction practices, and curing. The keys to success with SCC are understanding, consistency, and a willingness to manage with a hands-on approach.
Michael Stanzel has been the technical services manager for Lehigh Cement in Ontario since 2010. He is knowledgeable about cement quality and operations as he has 18 years of experience in the industry. Stanzel holds a bachelor’s degree in chemical engineering from Queen’s University. Stanzel is a member on the Canadian Standards Association (CSA) A3000, Cementitious Materials Compendium, Committee and the American Concrete Institute (ACI) and an associate member on CSA A23.1, Concrete materials and methods of concrete construction/Test methods and standard practices for concrete. Stanzel can be reached via e-mail at michael.stanzel@lehighhanson.com.