Demystifying self-consolidating concrete
SCC chemistry
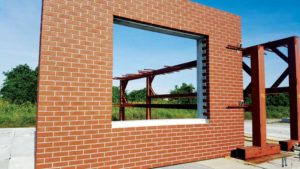
Photo courtesy Coreslab Structures
Consideration of SCC rheology first requires an understanding of the physical and chemical interactions within the paste system. The paste is a highly concentrated suspension of solid particles undergoing a series of chemical reactions. Portland cement-based materials comprise calcium silicates, calcium aluminates/alumino-ferrites, and calcium sulphates. When in contact with water, the hydration of cement proceeds in the following four stages:
- An initial rapid reaction where the highly soluble species dissolve to produce an aqueous solution of calcium and hydroxyl ions, aluminates, and sulphates. These ions create inter-particle charge differences resulting in particle agglomeration.
- An amorphous layer of calcium sulphoaluminate forms around each grain, thereby creating a diffusion barrier to provide a short dormancy period during which the concrete can be placed. During this stage, the concentration of the calcium and hydroxyl ions continues to rise until the water is saturated with calcium hydroxide.
- As the barrier wears off, there is a quick reaction where the calcium silicates in the saturated water precipitate out to form calcium-silicate-hydrate and calcium hydroxide crystals that grow and interlock with each other over a few hours, resulting in the setting of concrete and initial development of its strength.
- As the hydration products precipitate out of the solution, it allows further dissolution of the cement minerals. The reaction rate decelerates due to the thickening of the layers of hydration products around the cement grains and the filling up of free space within the matrix for the crystals. Supplementary cementitious materials react with, or in the presence of, the calcium hydroxide to form more calcium-silicate-hydrate to densify the product matrix and enhance its durability.
Most of the action with chemical admixtures is happening during the first few stages of the hydration process. The benefits of using high-quality admixtures cannot be overstated. It is critical to work with admixture and cement suppliers as some of the mechanisms and effects may compete with each other at various points.
It is important to note polycarboxalyte super-plasticizers absorb on to the cement grain surfaces to impart repelling electrostatic charges and create physical steric repulsion through the long polymer chains to de-agglomerate the flocculated suspension. This results in improved workability, slump retention, and a better water to cement interface for the hydration reaction and strength development of the mixture.
Additionally, accelerators and retarders absorb onto the hydrated surface to promote or impede the dissolution of certain cement ions to speed up or slow down the rate of reaction. Further, air-entraining agents stabilize the bubbles formed during mixing with a calcium hydroxide film.
Viscosity-modifying admixtures, typically based on polysaccharides, cellulose ethers, biopolymers, synthetic anionic polymers, and high molecular weight glycols, act as ‘micro-switches’ where they align and open while the concrete is under motion, and close when the concrete is at rest. This allows flow while under motion but causes a gelling effect when the concrete is still.
Other admixtures undergo various mechanisms at different stages. For example, shrinkage-reducing admixtures decrease the intra-capillary surface tension of the pore solution to bring down internal tensional forces, while shrinkage-compensating admixtures undergo slight expansion to cancel out the natural shrinkage of concrete.