Defining the Definition: Thermal continuity in IMPs
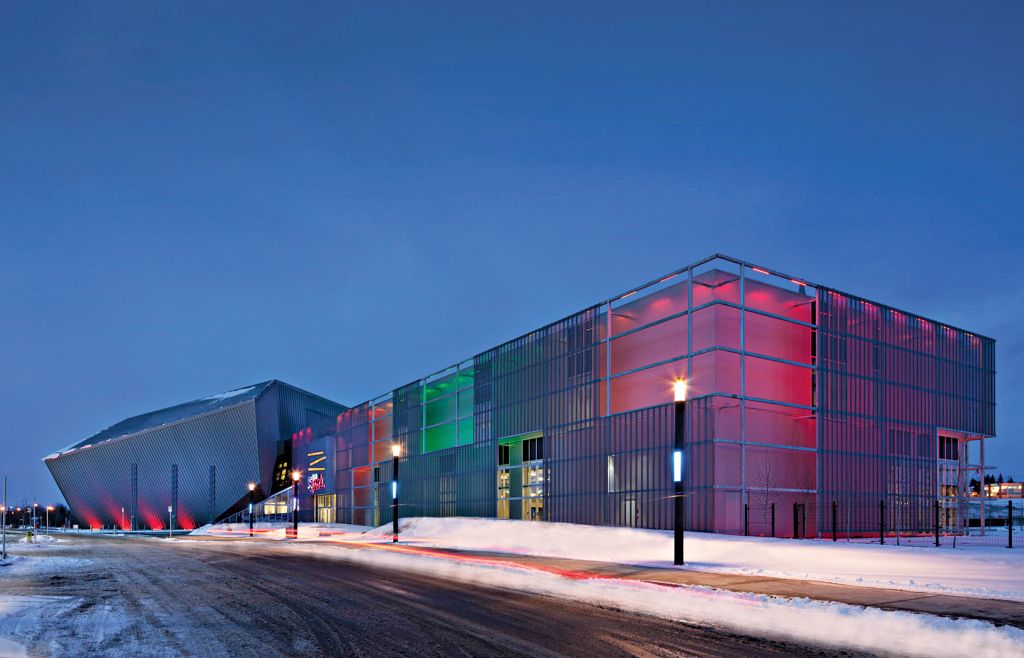
By Paul R. Bertram Jr., CSC, FCSI, CDT, LEED AP, and Ian J. Manser, CEM
Approximately one-third of Canada’s secondary energy use is the operation of commercial and residential buildings, which also account for the same amount of the country’s annual greenhouse gas (GHG) emissions.
This issue stretches further than North America, and the search for effective policies to decrease global energy demand is ongoing. Improving the energy efficiency in buildings has become a chief goal of policy makers around the world.
Building envelope
The building envelope system protects the structure’s other systems (e.g. structural, mechanical, and interior) from the harsh outside elements. This design approach focuses on initial overall enclosure as a key to reach maximum thermal energy efficiency.
To fully maximize the possibility of making a structure energy-efficient using the building envelope, many components must be considered. From construction to operations, the multitude of functional requirements to be met by the building envelope must be carefully analyzed regarding design and cost to ensure a high-performing building.
These requirements include:
- structural (i.e. wind barrier);
- weather barrier;
- air barrier (i.e. thermal);
- moisture management;
- energy conservation;
- sound barrier;
- fire safety; and
- security.
A chief functional requirement of the building envelope—the interface between the interior of the building and the outdoor environment, including the walls, roof, and foundation—is its role as a thermal barrier, which is important when determining the amount of energy necessary to maintain a comfortable indoor environment. An optimized building envelope also has an impact on lighting, HVAC, and building controls, leading to greater energy conservation. Similarly, insulation as part of the envelope assemblies helps slow the conduction of heat, improving building envelope’s thermal performance and influencing a structure’s energy demand.
Thermal continuity
Conduction is a fundamental process of heat transfer. Since the rate of heat transferred through a material is a function of its thermal conductivity, it is important to limit the opportunities for transfer through wall and roof elements by reducing conductive connections between the two environments.
A thermal bridge, or a cold bridge, is a condition where a penetration of the insulation layer by a highly conductive or non-insulating material takes place in the separation between the interior (conditioned space) and exterior environments of a building assembly.
Since a thermal bridge is a component in the building envelope that transfers heat at a significantly higher rate than the surrounding insulated area, it can be a significant cause of heat loss and underperformance of insulation assemblies in commercial buildings.
The locations of highly conductive materials such as steel studs, flashings, or fasteners need to be carefully considered, since their presence can significantly reduce the assembly’s overall thermal efficiency. Areas with comprised insulation, such as those created by joints and gaps, are also important.
It is also important to evaluate interfaces between different envelope components, such as windows or walls. With heat flow following ‘paths of least resistance’ for consistent thermal separation between interior and exterior environments, building designs should strive for thermal continuity of insulation at transitions between building envelope components such as wall-to-roof intersections, wall-to-floor or foundation intersections, or wall-to-wall intersections. It is important to incorporate proper detailing for these transitions to minimize heat loss through thermal bridging.
Using ASHRAE 90.1
To help ensure energy conservation policies are achieved, energy codes provide minimum standards and compliance requirements to assist in achieving a high-performance envelope, regardless of region or weather to which the building is subjected.
In North America, the most accepted energy-efficiency standard for commercial construction is the American Society of Heating, Refrigeration, and Air-conditioning Engineers (ASHRAE) 90.1, Energy Standard for Buildings Except Low-rise Residential Buildings. The 2010 edition was recently adopted in British Columbia, effective in December of this year, for Part 3 buildings (i.e. large residential, industrial, commercial, and institutional). Even though design for energy efficiency in Canada is necessary due to the harsh climate, British Columbia acts as a reference for the rest of the country in terms of high-thermal performance in buildings.
NECB and ASHRAE 90.1
The following are the major differences in approach between the 2011 National Energy Code of Canada for Buildings (NECB) and the ASHRAE standard.
- NECB uses incremental capital construction cost and annual energy savings for cost/benefit analysis, while ASHRAE 90.1 employs total lifecycle costing in the form of scalar ratio;
- NECB does not codify economics/social policy by having different requirements for various energy sources, while ASHRAE 90.1 does by establishing an Energy Cost Budget Method (i.e. performance path);
- NECB does not have different requirements for various constructs (e.g. different U-values for wall and roof constructions), while ASHRAE 90.1 does;
- NECB applies to new construction and additions, while ASHRAE 90.1 requirements also apply to alterations to existing buildings;
- NECB has a trade-off route with lighting, HVAC, and service water heating, while ASHRAE 90.1 does not; and
- ASHRAE 90.1 has one trade-off path, while NECB has a simple and detailed trade-off for building envelope.
Historically, ASHRAE 90.1 has been referenced or adopted with amendments throughout much of the United States. The 2007 version was adopted by 31 states, while 10 others having adopted earlier versions. Figure 1 shows the overall impact of NECB 2011 on performance improvement for energy used in Canadian buildings.
ASHRAE 90.1 is used by the International Code Council (ICC), along with provincial and local building code entities, to create energy codes by defining minimum standards for building construction, HVAC performance, and lighting. Included in these minimum standards are requirements for the amount of insulation necessary to meet the building’s proposed energy use. These are organized in tables, based on the region, or Climate Zone, where the building is being constructed, as well as the specified materials (e.g. steel-framed studs, wood-framed, or pre-engineered steel). The eight Climate Zones range from hot and humid Zone 1 to sub-arctic Zone 8. (Zones 7 and 8 are applicable for Canada.)
Continuous insulation
With ASHRAE 90.1 comes a concept that has stirred up debate—continuous insulation (ci). ASHRAE defines the concept as:
insulation that is continuous across all structural members without thermal bridges other than fasteners and service openings. It is installed on the interior or exterior or is integral to any opaque surface of the building envelope.
The problem is with how this definition is interpreted.
Continuous insulation is not a new concept; it has been in practice for more than half a century. However, design professionals and builders are progressively mindful of the value of ci in helping achieve desired thermal and moisture protection for all types of construction. Modern building standards and energy code requirements emphasizing ci likely have something to do with this. Continuous insulation standards on commercial exterior wall applications are prescribed in Climate Zones 3 through 8 in the standard.
There are two methods of compliance acceptable to determine the minimum thermal performance of opaque areas on the building envelope according to the ASHRAE standard.
These methods are:
- maximum U-factor for the entire assembly; and
- minimum rated R-value of insulation for the thermal resistance of the added insulation in framing cavities and continuous insulation only.
Per ASHRAE 90.1 definitions, U-factor (i.e. thermal transmittance) is “heat transmission in unit time through unit area of a material or construction and the boundary air films, induced by unit temperature difference between the environments on each side.”
In the context of ASHRAE 90.1, the assembly’s U-factor describes the thermal performance of the whole wall, roof, or floor. It accounts for materials commonly used and any typical thermal bridges.
U-factors are a measure of heat conductance. Since the inverse of conduction is resistance, the inverse of the U-factor is the more familiar R-value, or thermal resistance.
It is important to remember, however, the R-value derived from taking the inverse of the U-factor is the R-value of the wall or roof assembly. Because it applies to the whole assembly, and not just one of its components, this is commonly known as the assembly’s ‘overall R-value’ or ‘effective R-value. It considers the thermal resistances and configuration of all assembly components.
Table 5.5-7 (Figure 2) in ASHRAE 90.1-2010 for Climate Zone 7 (the largest in Canada) provides maximum U-factor values for different envelope assemblies, based on defined construction categories. ASHRAE further defines the basis of the construction categories in Appendix A of 90.1-2010.
The second part of the table provides the corresponding R-values of the insulation material required to achieve the prescribed U-factors. These recommendations account for the thermal bridging expected when using the defined construction.
The issue arises when adding additional insulation values to a defined construction, particularly since it is desirable to reduce the thermal bridging of the construction and/or impractical to add more insulation material within the constraints of the defined construction assembly.
One solution is to provide the additional insulation to the assembly as a non-bridged, continuous layer (i.e. continuous insulation).
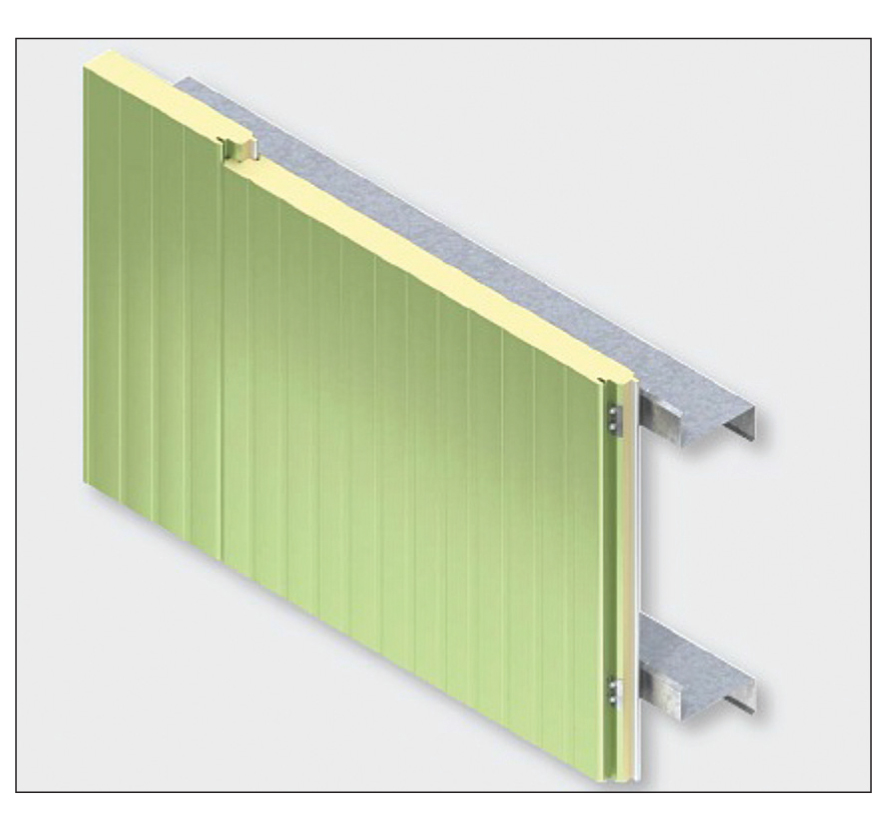
Within Canada, continuous insulation is used with ASHRAE 90.1 and provincial codes, with the intended purpose of providing a continuous layer of insulation that has an effective R-value equal to or close to its nominal R-value of insulation (i.e. minimal thermal bridging). It is often specified in energy codes alone, or in conjunction with thermally bridged nominal insulation, to achieve higher effective R-values and reduce impacts of thermal bridging.
In their attempt to continuously improve building performance, ASHRAE publishes revisions to the 90.1 standard every three years. Increases in performance required by NECB will be determined through the normal national Canadian consensus-based process with policy guidance from the provinces or territories. Often, each new revision increases the U-factor requirements.
Since most people are more familiar with the ‘R-value’ term than the more comprehensive (but more complicated) ‘U-factor’ term, there is a natural tendency to gravitate to the ‘minimum R-value requirements’ tables, rather than evaluating what is necessary to meet the U-factor requirement. By doing so, they encounter the continuous insulation requirements and begin searching for materials that satisfy the definition. It is critical to understand the purpose of the ci requirement, and look at materials and assembly designs meeting this purpose.
Insulated metal panels
Walls perform differently depending on how they are put together. Insulated metal wall and roof panels are a factory-built assembly well-suited to achieve high standards for building envelope thermal performance. Insulated metal panels (IMPs) have gained wide acceptance in Europe and are beginning to see increasing design opportunities in North America.1
IMPs are two sheets of coated metal with insulating material—usually polyisocyanurate (polyiso) or expanded polystyrene (EPS)—filling the void in between. They are moulded in various sizes and styles to accommodate numerous functional and esthetic applications. They are factory-manufactured using either a foamed-in place process or laminating process, both which are factory-controlled to create a uniform thickness providing consistent insulation performance. IMPs are used in many commercial, industrial, institutional, and cold storage applications because of their excellent performance characteristics and competitive costs.
These single-component systems allow for faster building completion in all kinds of weather, without risk to system integrity. Multiple installation steps for other insulated systems can make the building susceptible to premature system failures due to elemental exposures. Since IMPs combine the elements of a multi-component system into one installation, the installation process also requires fewer passes around the building.
IMPs are manufactured to meet performance and testing requirements of the latest model building codes and therefore carry ratings for fire, structural, thermal transmittance, foam core properties, water leakage, and air infiltration. They are installed outside the metal stud cavity or other structural support system. This minimizes thermal bridging, while efficiently incorporating a water, air, and vapour barrier using a single-unit wall assembly that eliminates the need for other materials and construction trade co-ordination. Since the U-factor is the sum of all R-values of each component in a system (i.e. stucco, insulation, gypsum wallboard, paint), the single component IMP system is the U-factor of all those components in one.
One of the main features of IMPs is the insulation value. The foam core of the panel provides R-values generally ranging from R-7 to R-42 as tested with ASTM C1363, Standard Test Method for Thermal Performance of Building Materials and Envelope Assemblies by Means of a Hot Box Apparatus, in thicknesses from 25 to 152 mm (1 to 6 in.) for wall systems. The test specimen includes a panel side joint to account for any thermal inefficiency that may occur even though the side joints of virtually all panel designs have a natural thermal break between the outer and inner metal facers. In other words, when considering IMP effective R-values, the test results reflect the expected thermal performance of the assembly as if it were providing a continuous thermal barrier.
Conclusion
When compared to other product options in both metal and non-metal, insulated metal systems offer a cost competitive, high-thermal performance system that answers current demands for an energy-efficient building enclosure while offering a wide range of design and performance features, all within a shorter installation time.
The trend toward energy efficiency in buildings will continue and the energy performance of the building enclosure will be a focal point for improved performance. IMPs are a technology solution for sustainability consideration with practical advantages that may not meet ASHRAE’s technical definition, but do provide thermal continuity on the building’s exterior.
Notes
1 Paul R. Bertram Jr., CSC, FCSI, CDT, LEED AP, and Ian J. Manser, CEM, were awarded Construction Canada’s F. Ross Browne Award for the March 2012 article, “Envelope and Efficiency: Meeting Code Requirements with Insulated Metal Panels.” (back to top)
Paul R. Bertram Jr., CSC, FCSI, CDT, LEED AP, is the director of environment and sustainability for Kingspan Insulated Panels North America. He represents the company on various U.S. Green Building Council (USGBC), American Society of Heating, Refrigerating, and Air-conditioning Engineers (ASHRAE), ASTM, International Code Council (ICC), and National Institute of Building Science (NIBS) groups. Bertram is also a past-president of the Construction Specifications Institute (CSI) and a member of Construction Specifications Canada (CSC). He can be contacted via e-mail at paul.bertram@kingspan.com.
Ian J. Manser, CEM, is the North American manager for Kingspan’s energy services department. A Green Associate under the Leadership in Energy and Environmental Design (LEED GA), he has more than 18 years of experience working with industry experts and design professionals in the advancement of building energy conservation and generation. Manser can be reached at ian.manser@kingspan.com.