Curtain walls and energy codes
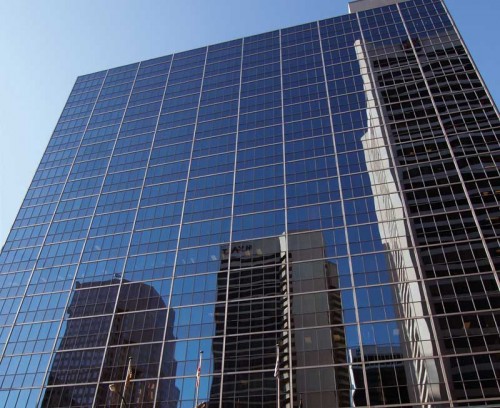
By Geoff McDonell, P.Eng., LEED AP
A curtain wall is a cost-effective building exterior enclosure system, and can be an esthetically pleasing envelope for many building types. From high-rise residential to office buildings, glass curtain wall cladding can provide architecturally eye-catching and highly marketable views for occupants. However, it is not an exterior cladding normally associated with high thermal and solar gain performance for reduced building energy use.
The last two decades of architectural design culture in many areas of Canada has led to an increasing trend for the maximized use of vision glass, with some use of insulated spandrel panels and, in some cases, ceramic fritting for solar gain control. The most common commercial building curtain wall systems consist of sealed double-glazed windows in an aluminum frame that may or may not incorporate any kind of thermal break. Insulated spandrel panels generally consist of an insulated metal pan installed in the same framing system as the windows.
Even in some of the country’s most extreme climates, it has been acceptable practice to continue to use double-glazed window panels, albeit with improved thermal and solar performance with low-emissivity (low-e) coatings and argon fills. The local designers usually pay attention to specifying a better degree of window thermal performance in more extreme winter climate zones, mainly to prevent indoor surface condensation and frost.
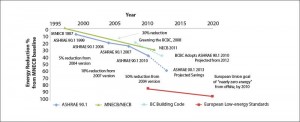
Image courtesy Cobalt Engineering LLP
Nationally, Canada has had an energy code (i.e. Model National Energy Code for Buildings [MNECB]) since the early 1990s, but this has only been applied and enforced for federally owned buildings on land under federal jurisdiction. Ontario is the sole province to have adopted it as an enforceable section of its provincial code. The City of Vancouver, unique in having its own municipal charter, has incorporated American Society of Heating, Refrigerating, and Air-conditioning Engineers (ASHRAE) 90.1, Energy Standard for Buildings Except Low-rise Residential Buildings, as part of the Vancouver Building Bylaw for the last 20 years. It will be enforcing ASHRAE 90.1-2010 sometime in 2012. On the other hand, British Columbia has only recently incorporated ASHRAE 90.1-2004 with an amendment to its provincial code in 2008. As incredible as it might seem, no other provinces have an enforceable building energy performance standard referenced in their building codes at this time.
The construction community must wrestle with the differing building design standards in each province, as well as face the fact that, sooner than later, all provinces will be including and enforcing some kind of energy performance requirement. The question is, how will the drive for improved energy performance affect curtain wall systems and designs?
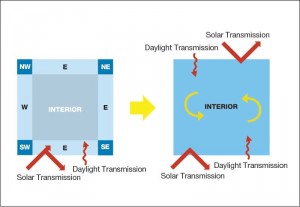
Images courtesy Geoff McDonell
Changing requirements at home and abroad
One of the key issues included in ASHRAE 90.1 (as well as the newly released 2011 National Energy Code for Buildings [NECB]) is a prescriptive maximum ratio of 40 per cent vision glass to opaque wall—the window-to-wall ratio (WWR). When the design employs a higher ratio, then a performance compliance path must be followed, requiring a detailed energy model to show the combination of other building systems (including mechanical and electrical) perform in such a manner to achieve equal or better energy efficiency compared to the reference building model designed with the prescriptive requirements. In fact, the trend going forward is to further reduce the WWR to 30 per cent in some climate zones.
ASHRAE 90.1-2013 will be released by 2014 and is anticipated to be 20 per cent more stringent than the 2010 standard. The U.S. Department of Energy (DOE) has required all states adopt ASHRAE 90.1-2010 (or an equivalent performance) by 2013. It will be interesting to see how this move affects Canadian energy codes, as it appears we tend to follow the Americans, considering a great deal of the glazing products are based on U.S. company supply chains. This definitely sets a bottom level for Canadian building energy standards as a potential ‘business-as-usual’ baseline for any building project starting design this year.
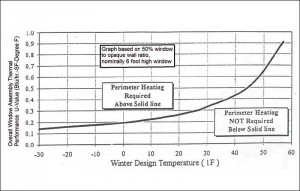
Data courtesy Don Holte
Many of the current European energy codes—such as the German Energy-saving Ordinance (ENEV 2009/German standard DIN V 18599), along with those for Sweden, Norway, and Finland—are about 40 to 50 per cent better than ASHRAE 90.1-2010, and an average of 80 to 90 per cent more stringent than the 1997 MNECB. Additionally, there are other prescriptive requirements for building envelope detailing and construction to minimize thermal bridging, as well as to prescribe minimum insulation values, window performance, and airtightness.
The European Union building energy use codes are being amended to reach a goal of “nearly zero energy” use off the grid by December 31, 2020, with the building energy primarily generated onsite with renewables. Stricter enforcement and oversight will be part of the European energy code developments toward 2020. (Visit www.europeanclimate.org/documents/LR_%20CbC_study.pdf for more information. The tables on pages 80–87 are helpful).
In Canada and the United States, the impact will likely mean realistic design approaches to more energy-efficient curtain walls will come into effect. Examples include:
- lower ratios of vision glass compared to opaque walls;
- triple and quadruple insulated glass (IG) units, including suspended film type products;
- significantly improved thermal break designs of framing systems;
- higher quality and thicker insulation of spandrel panels with 100 per cent vapour/air barrier to prevent condensation on the inside face of the outer panel, and integrate moisture control framing;
- glass tuned to the building orientation for better passive solar gains and reduced summer solar gains;
- ceramic fritting for solar gain control;
- exterior sunshades integrated with the curtain wall framing (these systems are ideally operable by occupants or motorized for automatic response);
- potential double-skin façade systems, carefully designed with effective passive ventilation and shading controls; and
- occupant-controlled operable windows—even in high-rises.
Thermal performance
Over the life of a building, the basic net result of improved window and curtain wall products will be:
- substantially lower energy bills;
- major reductions in capital cost of peak-load-sized mechanical and electrical systems; and
- significant reductions in lighting energy.
Properly tuned WWRs with glazing performance also eliminates commonly used (and often energy-intensive and high-capital-cost) perimeter compensation systems from the HVAC designs—no more perimeter baseboards, fan-coils, or induction units.
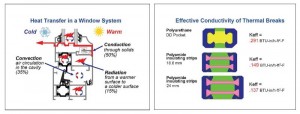
Images courtesy Technoform/Bautec
Extreme thermal loads inside the building imposed by the envelope (glazing systems, mainly) are commonly handled by supplying higher volumes of warm and cold air into the perimeter zone, where the heating and cooling loads are occurring. The fast-acting thermal transients, caused by poor thermal and solar performance envelopes, require a great deal of energy and responsive controls systems to maintain some level of human comfort. Such systems result in increased maintenance as well, incurring a high lifecycle cost and long-term high-energy expenses to operate.
The other intangible results of using better (i.e. higher thermal and solar performance) window systems will be significant improvements to occupant comfort around the perimeter zones through lowered mean radiant temperature (MRT) due to reduced internal surface temperature differences of the glass, as well as elimination of convective air currents from cold inner surfaces of windows. A design goal for climate-adapted design should be to select the glazing thermal performance based on maintaining an interior glass surface temperature above 17 C (63 F) at peak winter design conditions, and below 27 C (81 F) during peak summer conditions.
In a heating-dominated climate like Canada, this has great energy-reduction benefits—internal heat gains no longer leaking out of the bad envelope can be recovered via air-to-air heat exchanger systems to preheat the required ventilation air supplied to the occupied spaces. Further, there is plenty of colder air available for free cooling most of the year.