Curtain wall requirements imply teamwork
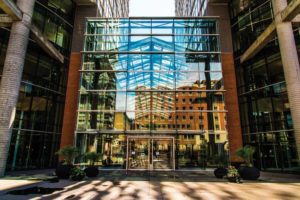
Deflection of glass-supporting frame members
The more the frame deflects under the load, the more stress is placed on the glass and the greater the likelihood of breakage. The general industry recommendation is to limit frame member deflection to maximum of L/175 of the unsupported span length (L) of up to 4.1 m (13.5 ft) in length, maximum L/240 + 6.3 mm (0.25 in.) at spans more than 4.1 m. The required deflection limit is determined by the specifier, who may discuss with the project’s structural engineer, but is often limited to 9.53 to 12.7 mm (0.375 to 0.5 in.).*
In Canada, aluminum work should be according to the Standards Council of Canada’s (SCC’s) CAN3 S157 Strength Design in Aluminum, with deflection under full design loads limited as noted above. Glass design should be according to CAN/CGSB-12.20 Structural Design of Glass for Buildings.
2. Provision for movement: Thermal expansion
Temperature differences must be considered, as they relate to differential expansion and contraction of various materials. Aluminum, the most common material choice for curtain wall framing, exhibits a relatively high coefficient of expansion in comparison to glass.
The potentially wide daily and seasonal fluctuations in the metal’s surface temperature can induce thermal expansion of typically 6.35 to 7.95 mm (0.25 to 0.3125 in.) in a 3.05 m (10 ft)* framing member. A contiguous sheet of glass will expand by less than half that amount. This disparity causes relative movement that must be accommodated without causing undue stress on glass, joints, and anchors, or without excessively reducing the frame’s ‘bite’ on the glass.
*SI/IP equivalent measurements are as quoted from the reference document or mathematically converted using standard formulae.
3. Weather tightness
Weather-tightness means protection against water leakage and excessive air infiltration. It depends in large measure on adequate provision for movement and is closely related to proper joint design.
Water penetration
Two methods have been developed for preventing leakage through the wall. One is referred to as the ‘internal drainage’ or ‘secondary defense’ system, wherein minor leakage can be shunted by a system of flashing, collection, and drainage devices. The other is the more sophisticated ‘pressure equalization’ method, which is based on the ‘rain screen principle.’ A rain screen system requires the provision of a ventilated outer wall surface, backed by drained air spaces in which pressures are maintained equal to those outside the wall.
The specifier may optionally specify pressure-equalized rain screen wall cladding (PRWC) systems that meet the requirements of AAMA 508-14, Voluntary Test Method and Specification for Pressure Equalized Rain Screen Wall Cladding (Panel) Systems, when tested in accordance with ASTM E331, Standard Test Method for Water Penetration of Exterior Windows, Skylights, Doors, and Curtain Walls by Uniform Static Air Pressure Difference. AAMA 508 and other AAMA references are documents of the Fenestration Glazing and Industry Alliance (FGIA).
Site checks for watertightness conducted during installation are highly recommended to verify the design and installation are satisfactory or to reveal deficiencies in the sitework. Consequently, they should be made early in the installation process, so any faults discovered may be remedied before much of the wall is in place. On tall buildings, the check usually is repeated once or twice at higher levels as an added assurance.
The newly installed curtain wall shall be site tested by an AAMA-accredited independent laboratory, as soon as practical after installation, in accordance with AAMA 503, Voluntary Specification for Field Testing of Newly Installed Storefronts, Curtain Walls and Sloped Glazing Systems.
AAMA Accredited Laboratories are qualified to conduct performance testing for air leakage, water penetration, deflection, and structural strength. Some of these laboratories are also qualified to conduct condensation resistance, thermal transmittance, and other performance tests. A current listing of Accredited Laboratories is available from AAMA.
Resistance to water penetration performance requirements will vary depending on the building’s height, geographic location, and exposure classification. In Canada, the CAN/CSA-A440 Standard includes a user’s guide, which recommends minimal performance levels for each major Canadian city based on geographic location and installation height, while in the United States, the resistance to water penetration rating is typically established as a function of the design wind pressure.
Specifiers should remember to check the NBC (Part 5) to see whether it differs from the provincial code or local jurisdiction. Exact project requirements must comply with, and may exceed, the applicable building codes based on the project’s location.