Critical considerations for replacing a flat roof
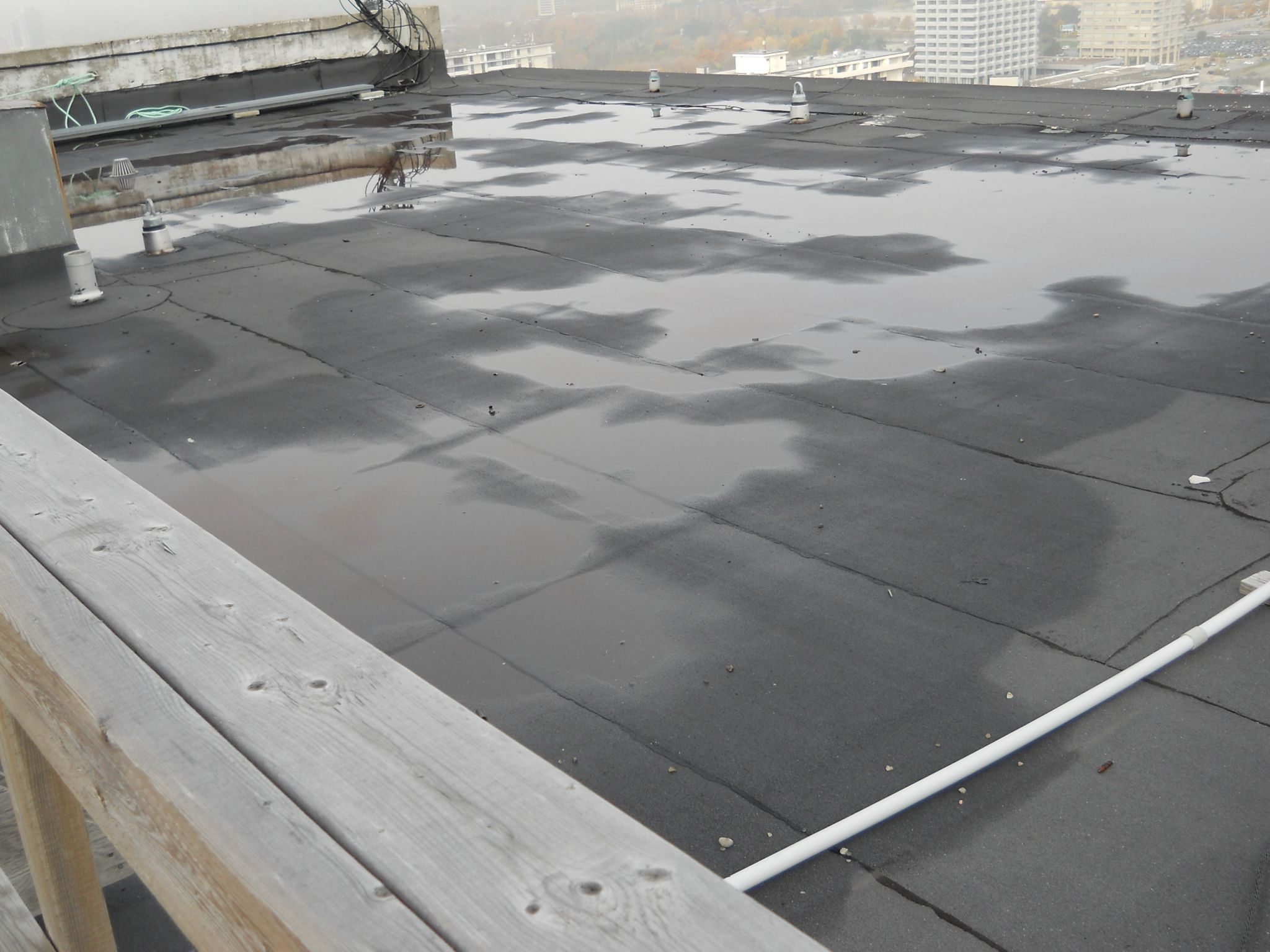
By Allen Lyte, B.Tech., A.Sc.T., RRO, and Cathy Lee, M.A.Sc., P.Eng.
Re-roofing can be one of the largest capital projects undertaken at a building. When it comes to replacing a flat roof, the options can be overwhelming—each choice comes with its own list of pros and cons. Without careful consideration at the time of design, there could be unexpected or costly consequences down the line. At best, poorly considered choices can pose a nuisance or result in an excessive maintenance burden over the life of the roof. At worst, overloading could lead to failure of the building structure or a tear-off of the roofing.
This article deals with four critical aspects to consider when replacing a flat roof: the structural deck, the membrane, drainage, and wind uplift.
Structural deck: consider the load
The term ‘roof’ is used to refer to an entire assembly, including both the roofing components such as the membrane, insulation, and vapour retarder, as well as the structural deck. The structural deck not only supports the roofing components, but it also supports any intended rooftop equipment (such as heating/air-conditioning units), as well as people and snow loads.
For flat roofs (also referred to as low-sloped roofs, since all roofs require some slope to drain), structural decks are usually constructed of concrete or steel. For the latter, the most common is fluted metal decking on open web steel joists (OWSJs). Roof decks are designed to support a particular load (or weight). Therefore, it is important any changes to the loading conditions be carefully assessed.
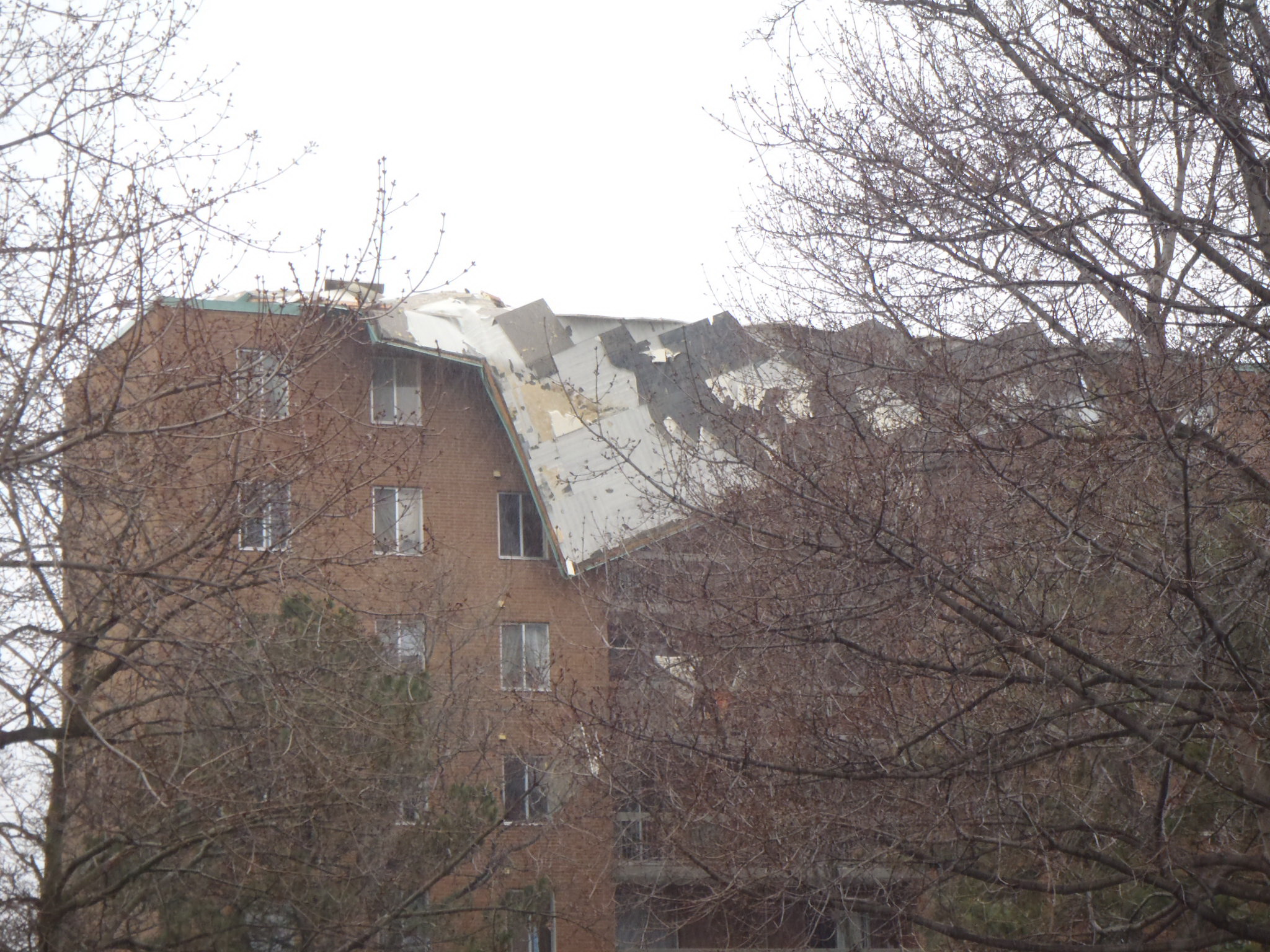
Cast-in-place reinforced concrete roof decks are typically seen in high-rise or multi-storey buildings. Concrete decks often have some amount of excess load-carrying capacity. In other words, they can usually support a little more weight than for which they were strictly designed, without structural distress.
In comparison, metal roof decks with OWSJs (commonly seen in industrial buildings, retail facilities, and low-rise multi-residential buildings constructed in the 1950s and ’60s) are designed to tight tolerances. They are frequently built to carry little more than the initial design loads.
Two common roof renewal strategies that affect loading conditions are overlays and conversion to a ballasted system. An overlay involves installing a new membrane (and often, insulation and/or a cover board) over the existing roofing assembly. If done correctly, an overlay can be an effective performance management strategy. However, overlaying a flat roof can be much more complicated than the common practice of installing another layer of asphalt shingles on sloped roofs, for example. Adding these new materials, without removing the existing components, can impose greater loads than those for which the structure was designed. It is therefore important these loading conditions be evaluated.
Similarly, converting to a ballasted roof system can have significant structural implications. A ballasted system involves adding material (such as gravel or pavers) to weigh down the membrane and insulation. Just 50 mm (2 in.) of gravel ballast can weigh about 0.6 kPa (12.5 psf). By comparison, a typical built-up roof (BUR) weighs about 0.32 kPa (6.7 psf). As metal roof decks typically have very little excess load-carrying capacity, the additional weight of ballast is significant. Generally, most metal roof decks are not capable of supporting these additional loads. Therefore, a ballasted roofing system should not be used to replace a non-ballasted system without a detailed structural analysis.
Membranes: select the right one
The membrane is what keeps the water out. There are many different types of membrane systems, but they generally fall into three broad categories:
- bituminous membranes, such as modified bitumen (mod-bit) or built-up felt and asphalt systems;
- liquid-applied coatings, such as rubberized asphalt or urethane-based elastomeric traffic deck coatings; and
- single-ply membranes, such as polyvinyl chloride (PVC), thermoplastic olefin (TPO), and ethylene propylene diene monomer (EPDM).
A wide selection of membrane systems is available, each with its own performance, cost, and durability characteristics.
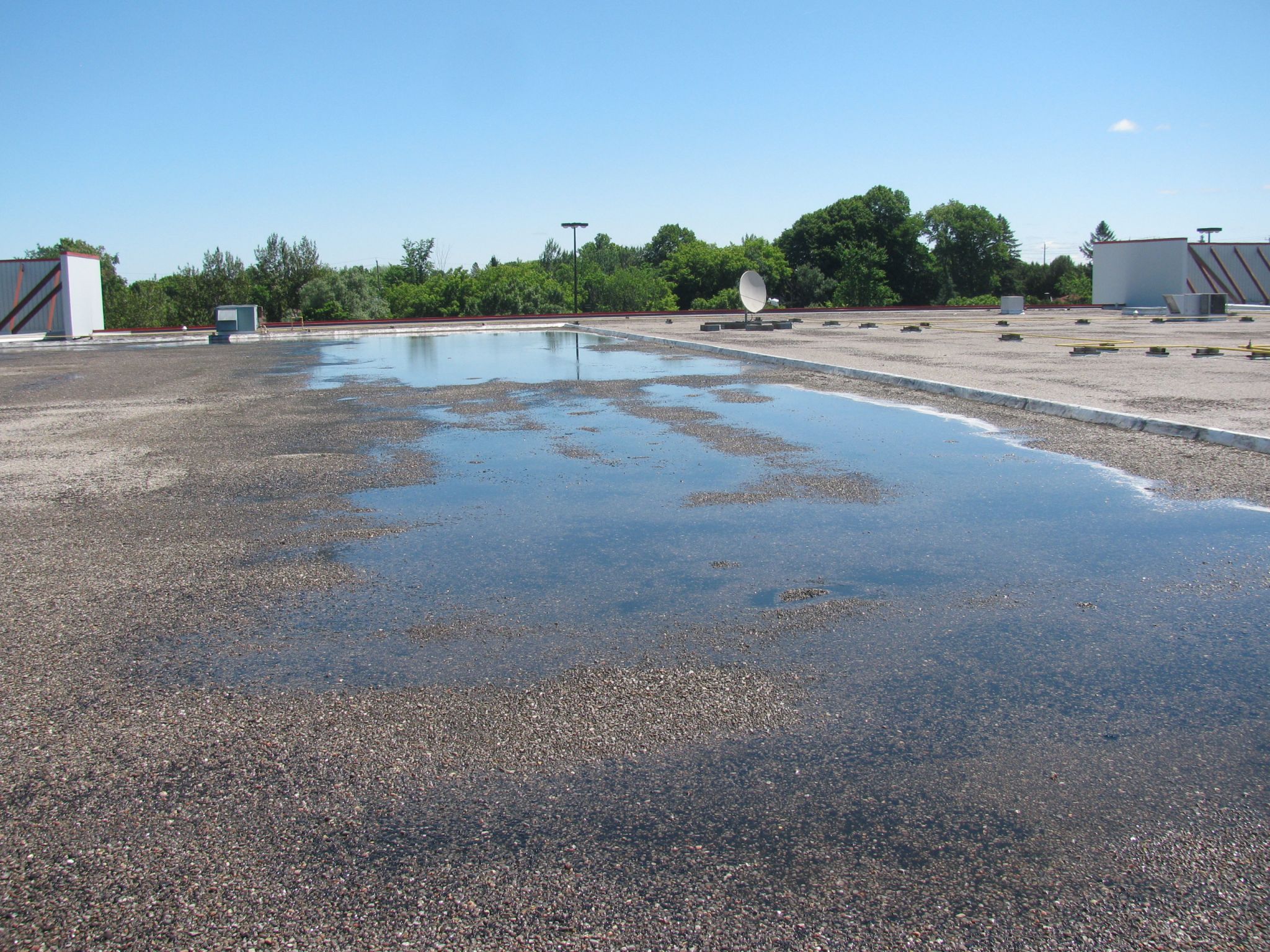
Some membrane systems are more resistant to ultraviolet (UV) exposure from the sun, while others stand up better to punctures, tears, abrasion, or other physical damage. Some membranes are more resistant to thermal fluctuations or severe climates, while others perform better from an energy perspective.
In selecting a membrane, it is important to carefully consider the service conditions. For example, an exposed single-ply membrane would not be advisable for a roof with a large amount of rooftop equipment as it would be less resistant to inadvertent punctures or physical damage caused by service contractors.
Another example of a service condition would be when the roof is readily visible (such as by occupants from overlooking windows). In these cases, it might be a good idea to avoid an exposed light-coloured membrane as it will look dirty, even with regular cleaning.
A further consideration when replacing a roof would be where mobilization or access forms a significant portion of the overall re-roofing cost, or any down-time associated with leakage would be critical. For such instances, investment in a premium membrane system with a longer expected service life might be warranted.
Geographical location can also impact membrane selection, as the availability of materials and/or the equipment and skill set required to install a particular roofing system can vary by region. Built-up membranes, for example, occupy a substantial share of the Ontario market because many relatively large, established roofers have invested in the kettles, tankers, and equipment required to install BUR systems. In contrast, mod-bit assemblies are more popular in British Columbia, and single-plies are more common on the East Coast.
When selecting the appropriate membrane system for a roof, it is important to consider not only the performance merits of the specific roofing materials, but also a host of other factors, including the roof geometry and structure, service conditions, and availability of materials and qualified installers.
Drainage: make it effective
Roofs are meant to shed, not hold, water. Large amounts of standing water sitting for long periods can increase the risk of leakage, and decrease the membrane’s service life. In certain situations, stagnant water can become a breeding ground for insects like mosquitos, or create a safety concern. For example, water can freeze, causing a slipping hazard for maintenance staff accessing the roof.
Effective drainage relies not only on an adequate number of drains, but also effective slopes to those drains. Drains, even if numerous, are useless if they are located at the roof’s high points.
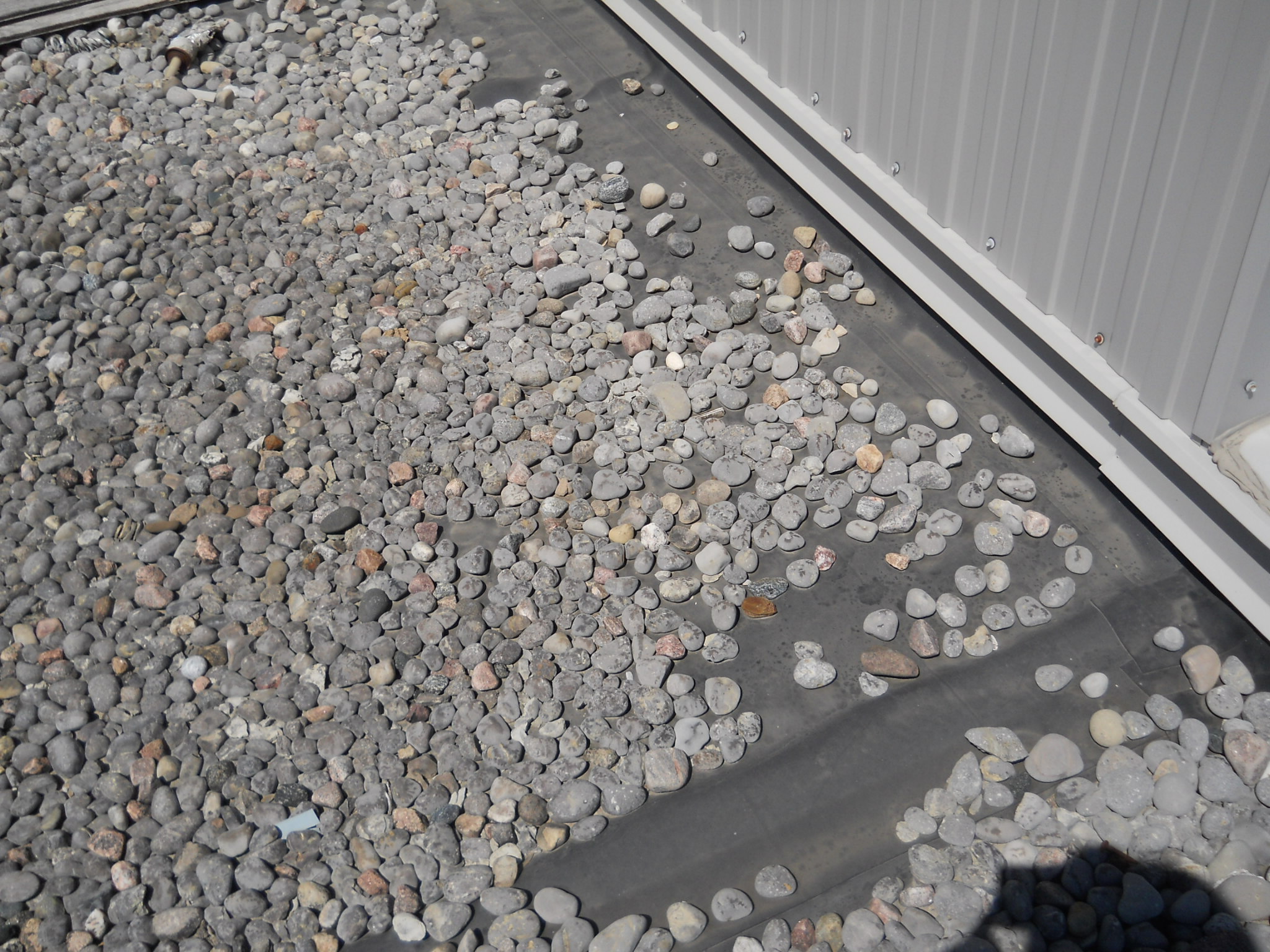
In conventional roofing assemblies, where the membrane is installed atop the insulation, tapered insulation boards are frequently used to slope the membrane surface toward the drains. In protected membrane assemblies, the waterproofing membrane is installed below the insulation; in these cases, effective drainage relies on the slope of the structural roof deck itself. For some instances, lightweight concrete toppings are used to provide slopes to drains. In other cases, as in poured concrete slabs, the top surface of the slab is simply finished to drain at the time of construction.
When a roofing system is changed, the impact on drainage must be considered. This is particularly important when switching from a conventional system to a protected membrane system. A roof that previously relied on tapered insulation to provide adequate slopes to drains is now limited by the structural roof deck’s slope. If the deck was not originally designed to slope, this could result in ponded water.
In some cases, drainage problems may be alleviated by installing additional area drains. However, it may not be practical to install new drains—for example, in the case of condo or apartment buildings where a large portion of the floor area is occupied by residential units.
Drainage can also be affected by changes to the thickness of the insulation. Increasing the thickness may cause problems with scuppers and overflow scuppers. As well, improperly designed overlays can affect drainage, particularly when installed on a roof that already had problematic drainage.
Wind uplift: go beyond manufacturers’ guidelines
Wind moving across a flat roof can impose suction forces that cause the assembly to lift off the structure. The membrane and perimeter flashings must be designed to resist wind uplift. Securing a roof is typically achieved by weighing down the roofing with ballast, mechanically fastening the assembly to the structural roof deck, adhering the roofing system components together, or a combination of the above.
Design standards to resist wind uplift are not well understood by many roofing applicators/installers. Contractors typically rely on manufacturers to provide rule-of-thumb guidelines for securing the roof system to resist wind uplift, but this means other important factors, like local wind speeds (based on geographical location), building height, and terrain exposure are often not considered. As well, most manufacturers’ guidelines to resist wind uplift were not created for Canadian codes. It should be pointed out, however, that some product providers do test to conservative standards, such as those established by Factory Mutual (FM) for loss prevention purposes.
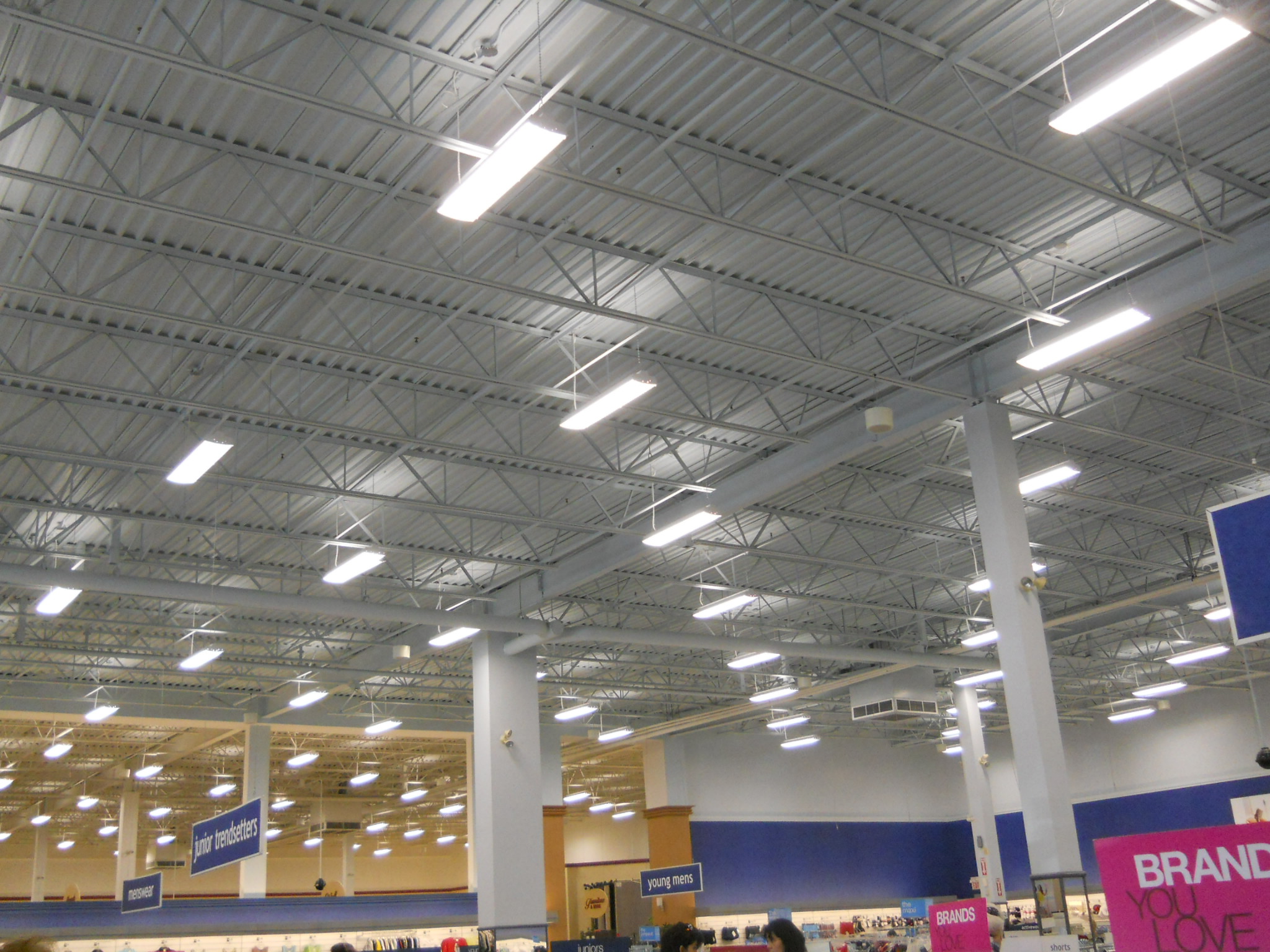
One area of the roofing system that requires special attention is the roof edges. This is because the highest wind pressures are at the perimeter and corners of the roof. If there is a failure here, catastrophic failure could result as the roof begins to peel. Therefore the roof system, including the sheet metal flashings that typically conceal the termination of the roof system at the roof edges itself, must be strongly secured. This involves carefully considering the sheet metal flashing profile as well as the type and quantity of fasteners to be installed where higher winds loads may be experienced.
The bottom line
Replacing a roof may appear simple, but, in fact, it involves numerous considerations critical to the success of the project. For best results, building owners should obtain the advice of experienced professionals. In particular, it is important to involve a structural engineer or another consultant familiar with the structural implications of re-roofing.
One should also confirm whether a building permit is required for roof replacement. Many roofs are simply designed and installed directly by contractors, for the owner, without engineering involvement. While this is not always problematic, it should be made clear from the beginning who is designing the roof replacement, and whether or not they carry professional liability insurance.
Finally, replacing a roof can present a great opportunity to protect and enhance an investment. While some building owners simply choose to replace like-for-like, many take the opportunity to change aspects of the system to improve durability and longevity, increase energy performance, and control costs. Again, an experienced professional can help navigate the structural, serviceability, and durability concerns to ensure the most appropriate system is specified for the specific building and budget.
Allen Lyte, B.Tech., A.Sc.T., RRO, has been with Halsall Associates since 1999, specializing in roofing technology and its application. As the manager of the Roofing Practice Team, he is also responsible for ensuring Halsall’s knowledge and processes with respect to roofing remains current and best-in-class. Lyte is a past director and president of the Ontario Chapter of the Roof Consultants Institute (RCI), and a member since 2002. He can be contacted at alyte@halsall.com.
Cathy Lee, M.A.Sc., P.Eng., is a senior principal and technical lead with Halsall Associates. Over the past 15 years, she has completed property condition assessments and capital plans for all types of buildings across Canada. Lee can be reached at clee@halsall.com.