Creating a fire-safe construction site
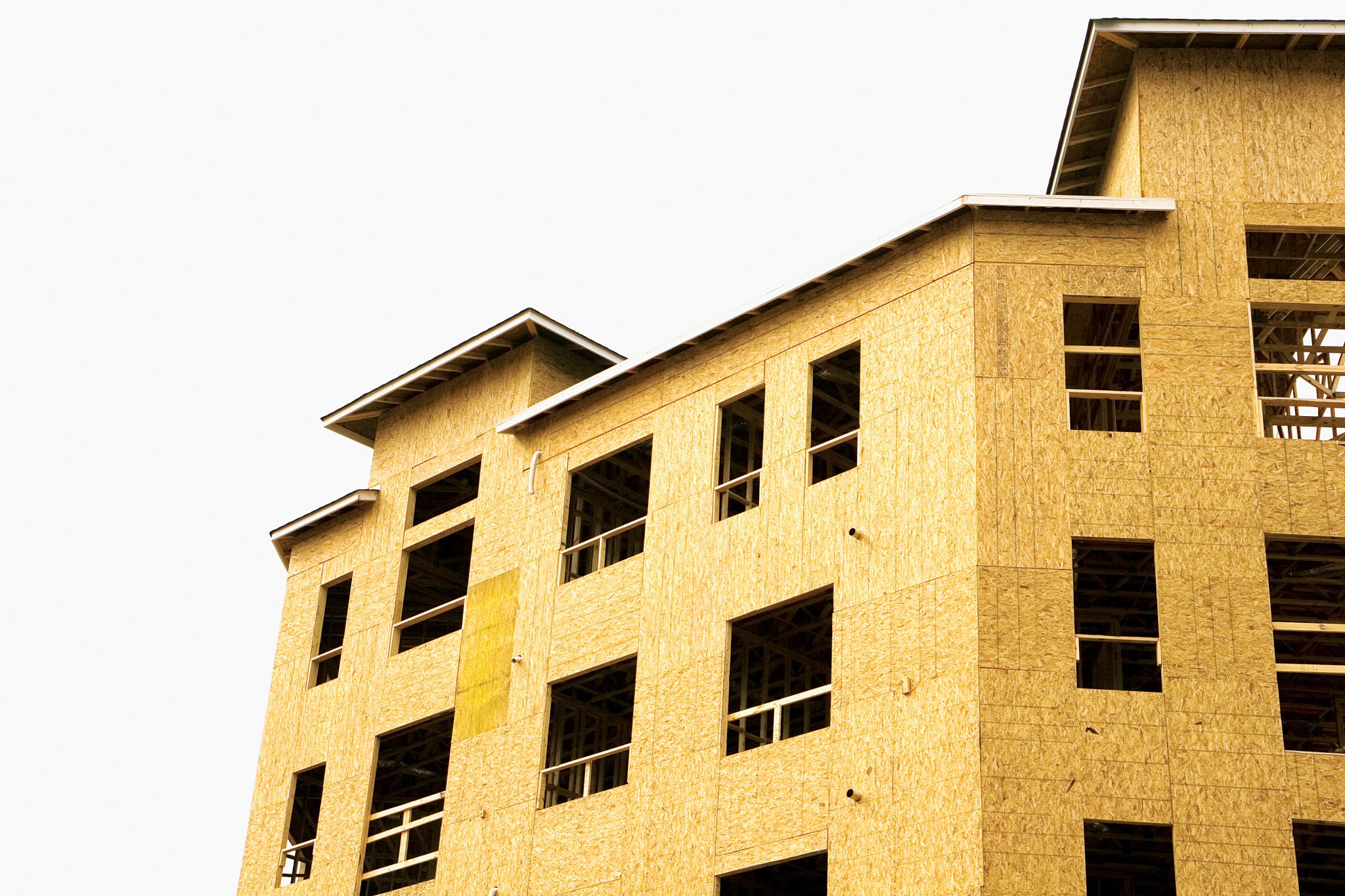
By Steven Craft, PhD, P.Eng, Ineke Van Zeeland, M.Eng., ASFPE, and Steven Street
Most construction site fires can be prevented. However, for those that do occur, the impact can be significantly lessened with knowledge, planning, and diligence. Understanding and addressing hazards and risks for each construction site requires education and training, as well as preparation and perseverance.
Conforming with local safety regulations is the foundation for establishing suitable construction site fire safety. Assessment, selection, and successful implementation of best practices, based on a site’s specific needs, build on this foundation and lead to a fire safety culture understood and practised by all.
Construction site fire safety has unique challenges. An understanding of fire hazards and their potential risks is the first step toward prevention and mitigation. The construction phase of any building represents a relatively short period in the structure’s lifespan during which fire risk scenarios are present. The risks and hazards found on a construction site differ in both nature and potential impact from those in a completed building, since permanent fire prevention and protection elements are not in place.
The next step in addressing construction site fire safety is determining local regulations applicable to the specific project, and then implementing the necessary measures to ensure compliance is in place. The National Building Code of Canada (NBC) and National Fire Code of Canada (NFC), both contain provisions related to construction site fire safety.
These include:
- 2010 NBC, Division B, Part 8, “Safety Measures at Construction and Demolition Sites;”
- 2010 NFC, Division B, Section 5.2, “Hot Works,” under Part 5, “Hazardous Processes and Operations” and;
- 2010 NFC, Division B, Section 5.6, “Construction and Demolition Sites,” under Part 5, “Hazardous Processes and Operations.”
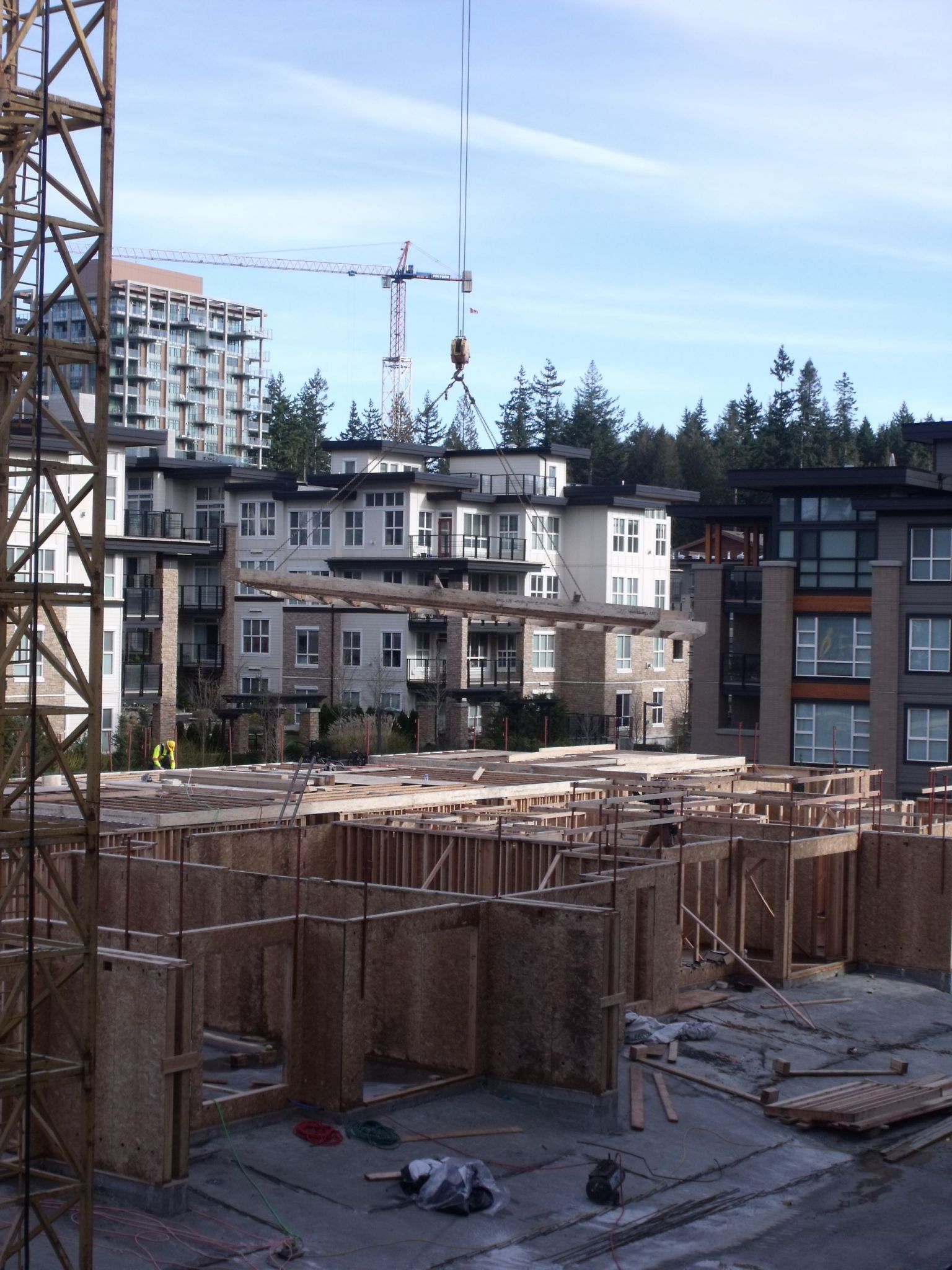
Every province in Canada adopts some variation of NBC and NFC—with the exception of Prince Edward Island, where larger municipalities have adopted NBC. The previously mentioned code sections relevant to construction site fire safety are largely adopted in most provinces, except for Ontario where provisions fall under the Occupational Health and Safety Act (OHSA).
However, even for Ontario, many fire safety requirements in OHSA are similar in intent to those in the NFC, apart from the most significant difference—lack of requirement for a fire safety plan (FSP) for construction sites, as discussed later in this article.
In addition to provincial building codes, other regulations may be applicable depending on specific systems, equipment used, and the processes and operations taking place on the building site. Local governments may also have specific laws, regulations, or requirements.
The specific, applicable regulations provide the base requirements for construction site fire safety. In many cases, a developers’ insurance provider will also have requirements for construction site fire safety precautions.
In other settings, safety on a construction site goes hand-in-hand with quality, productivity, and profitability. If this is understood, it can be considered an incentive to meet and exceed regulated standards. Therefore, an examination by the constructor of all possible factors and options can be beneficial. Consideration should be given to a project’s characteristics, objectives, goals, and how fire risks may impact construction during all phases of work. An understanding of fire safety basics and how to control risk during the construction period is important in reducing unexpected financial risk and is helpful in the decision-making process.
Fire basics
For any fire to start, oxygen, a source of ignition (i.e. an external source of sufficient energy, such as heat), and sufficient readily ignitable fuel is required. These three components makeup what is known as the ‘fire triangle.’ Take away an element of this triangle, and fire cannot start, or similarly, fire can be extinguished once it occurs.
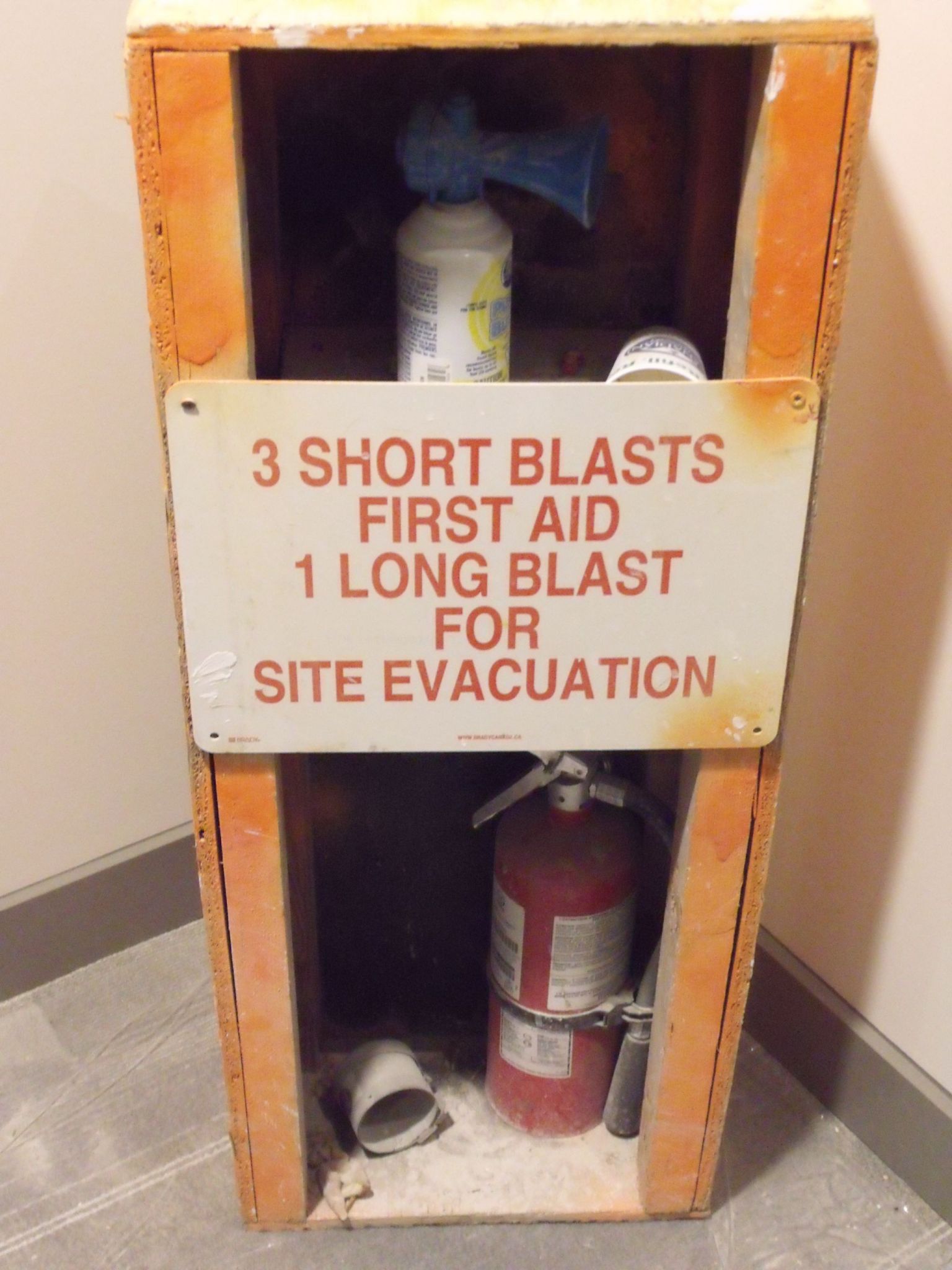
Construction sites tend to have a potential abundance of all three components. However, since it is rather impractical to control the availability of oxygen on a construction site, fire safety focuses on reduction and control of possible fuel and ignition sources.
According to National Fire Protection Association (NFPA) analysis, the first line of defense in construction site fire safety is reducing the potential for ignition. The three leading causes of fires in buildings under construction are:
- incendiary or suspicious (40 per cent);
- open flame, embers, or torches (21 per cent); and
- heating equipment (10 per cent).1
To a lesser degree, other causes include smoking materials, natural causes (e.g. lightning), electrical sources such as distribution systems, appliances or tools, and external fire sources (e.g. forest fires).
Many fires in the ‘open flames, embers, or torches’ category are started by ‘hot-work’ activities onsite. According to NFC, hot work involves open flames or produce heat or sparks, and include:
- cutting;
- welding;
- soldering;
- brazing;
- grinding;
- adhesive bonding;
- thermal spraying; and
- thawing pipes.
In many cases, it is possible to remove the need for various types of hot work by changing the design, removing potential hazards. For example, structural steel connections can be bolted rather than welded onsite, and available alternatives to torch-applied roofing materials can be used.
Designing and using a heating/drying system situating heating equipment outside the under-construction structure can also reduce ignition risk. When heating/drying equipment is situated inside, care should be taken to maintain adequate clearance around the equipment, and to ensure adequate ventilation to combustibles, as required by NFC, if fuel-fired appliances are involved.
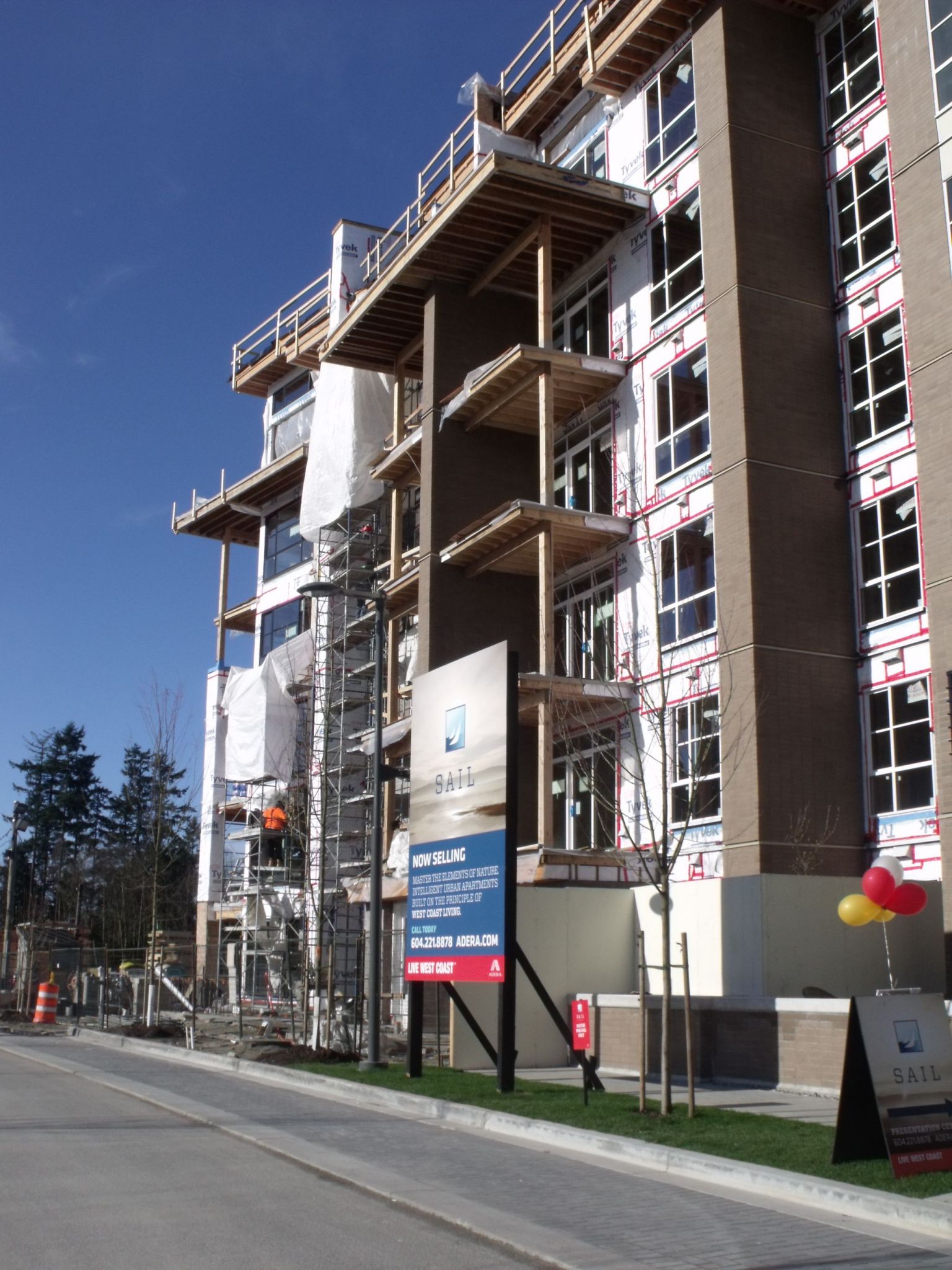
Fuel sources
The second line of defense in construction site fire safety is controlling readily ignitable fuel sources. This reduces the probability of an ignition source starting a fire, and limits fire spread when ignition does occur.
As with the handling of potential ignition sources, sensibly managing quantities of available, easily ignited fuel can significantly reduce frequency and impact of fire. While structural wood products, wood-based formwork, and scaffolding do not tend to catch fire easily, they may become involved if excessive quantities of readily ignitable waste materials—such as paper and wood shavings—are left lying around. Consequently, good housekeeping can be one of the most important factors in site fire prevention.
Proper storage and removal of combustible waste onsite reduces the risk of fires. The regular removal of construction waste can also help thwart opportunistic fire-setters. Strict controls on storage of combustible and flammable liquids and gases, as well as any refuelling activities, should also be observed.
There is often desire to continue construction year-round, resulting in numerous temporary site envelope enclosures. With these various systems in use, it is important to consider the fire performance characteristics of onsite materials, as some are more flammable than others. Contact of such systems with possible ignition sources should also be avoided.
These materials range from tarpaulins purchased at the hardware store to insulated and/or fire-retardant-treated systems In this vein, NFC requires fabrics and films used to temporarily enclose buildings be securely fastened to prevent them from being blown against heaters or other ignition sources.
Onsite fire procedures and equipment
Currently, in many jurisdictions there are no requirements for a dedicated person to oversee all fire-safety aspects on a construction site. However, it is considered best practice to designate a full-time ‘fire-safety coordinator’ or ‘fire-safety officer.’
In the past, such a role was sometimes assigned to site managers or supervisors as an additional function. However, it has been recognized the two functions are not mutually exclusive, and both have significant levels of responsibility. As there is typically a requirement for a construction safety officer onsite (under health and workplace safety regulations), it is possible this person can also assume the role of fire-safety officer.
Hot-work procedures
NFC requires precautions to prevent fire during hot-work activities. Requirements include:
- a fire watch be provided during hot work and for at least one hour after its completion; and
- a final inspection of the hot-work area conducted four hours after completion.
A key requirement of NFC is the removal or covering of combustibles in the area during hot work to prevent ignition. Fire-retardant covering materials, such as welding blankets, are available for this purpose. Since sparks can skip under covers, resulting in ignition, care must be taken in their use.
Combustible materials or building surfaces that cannot be removed or protected against ignition must be thoroughly wetted where hot work is carried out. The impact of water on the structure and finishes can be reduced by use of wet sand, fine water sprays, or pressure-washers to limit the quantity of water used. However, wetting should be sufficient to extinguish sparks on contact. It should be noted, in some cases wetting may be impractical, especially when trying to meet the maximum moisture limits set for a wood structure to proceed with the ‘closing-in’ construction phase.
It is a good idea to require a system of hot-work permits to be in place for work to occur onsite. This helps ensure operators are properly trained and necessary precautions are followed.
Extinguishers and standpipe systems
When it comes to fire-related equipment onsite, NFC Article 5.6.1.5, requires portable extinguishers be provided in various locations. Additionally, where NBC demands a permanent standpipe system be installed in the completed building, Article 5.6.1.6 calls for a temporary or permanent system be installed within one storey of the uppermost work level.
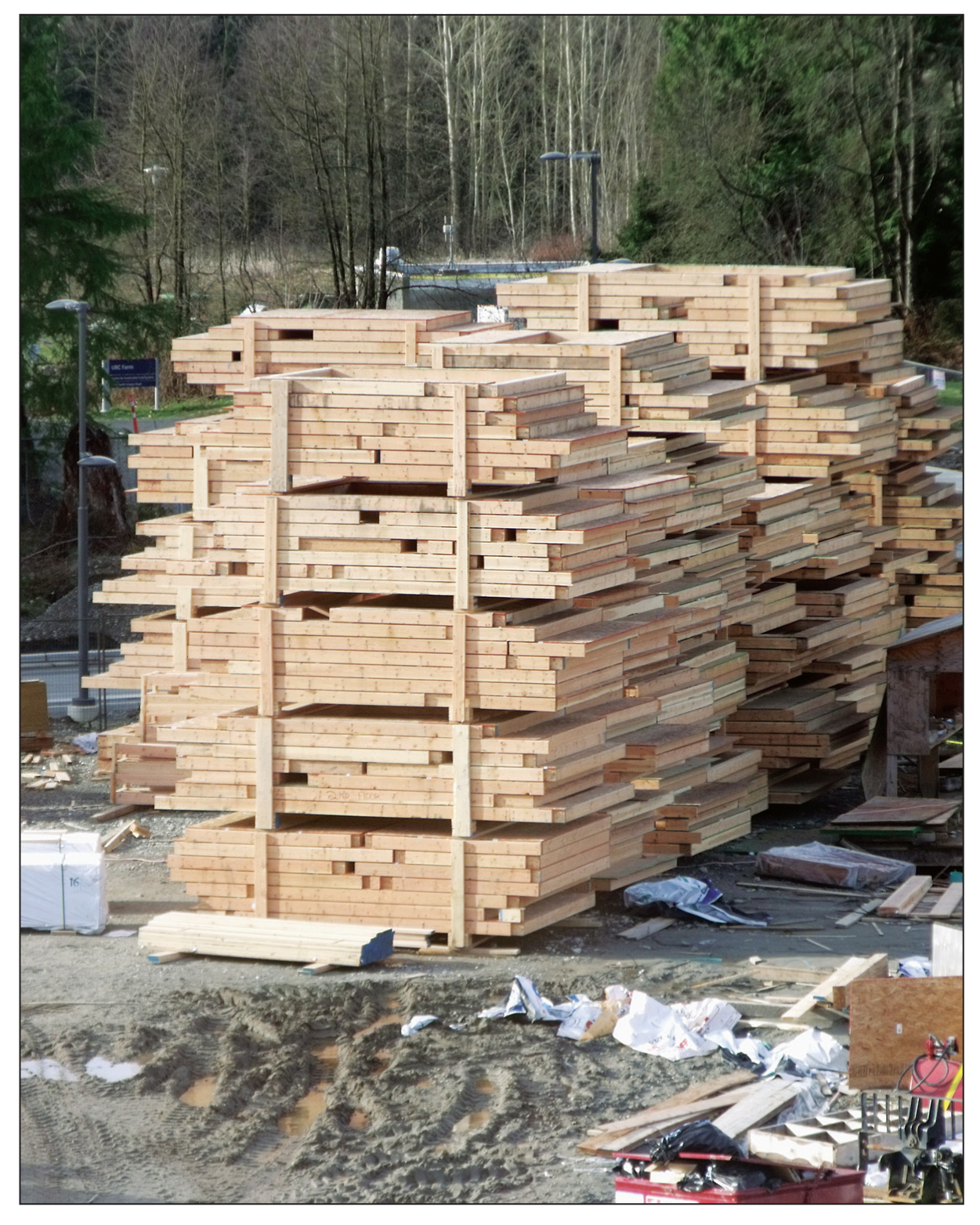
As a recommendation for best practice, plans and specifications should indicate when a standpipe is required during construction. In a cold climate subject to freezing, a ‘wet’ riser requires insulation and heat-tracing. Since the location of and access to a standpipe system may differ somewhat during construction from the final design, it is helpful to communicate this information to the local fire service.
Detection and alarm systems
If a fire occurs during construction site hours, the primary aim is to ensure everyone onsite reaches safety as quickly as possible. To this end, NFC requires a system capable of sounding an alarm to be heard throughout the construction site to alert personnel in the event of a fire—this could be as simple as an air horn next to the fire extinguisher on each floor. Such equipment and its associated response usually occurs in parallel with other emergency procedures to notify the fire service and respond to the fire.
Significant factors in reducing potential damage arising from a fire are detection speed and a reliable means of alerting emergency services. The amount of damage that can occur from a fire in a building under construction is impacted by the time it takes fire service to be made aware of it.
Numerous challenges exist in installing fire detection systems during construction. Some devices may be activated by operations conducted onsite. For example, hot work can generate products of combustion, such as heat and smoke. For this reason, some sites de-activate detection systems during work hours, reinstating the protection when the site is relatively unoccupied. Detectors can suffer physical damage due to handling and other construction activities, although the addition of guards to surround detectors can reduce the degree or frequency of damage. Regular cleaning or replacement of detectors may also be considered.
Fire sprinkler systems
Challenges similar to those described for fire detection/alarm systems and standpipes also apply to the installation of temporary or permanent automatic sprinklers at any stage of construction. There are specific sprinkler-related issues to be considered in contemplating either the early installation of a permanent sprinkler system—if one is to be present in the completed building—or installation of temporary sprinklers, which may be separate from, or make use of, a permanent system’s water-supply piping.
As access to a sufficient and reliable water supply is important for the sprinkler’s performance, water supply issues should be taken into consideration. A fire pump may be needed to provide appropriate water pressure to a sprinkler system protecting a building during construction. However, installation and fire pump commissioning for use during the construction phase can be complicated and expensive.
Temporary sprinklers are often recommended during both the construction phase and post occupancy. The temporary sprinklers commonly need to be replaced and new sprinkler heads are installed aligned with ceiling finishes. Systems can be protected by guards to enable a temporary level of protection during building construction, but some guards can affect sprinklers’ activation and performance.
In new developments, fire hydrants are often installed with other services before construction begins. However, it is important to ensure they are ready for use. In some jurisdictions, the municipality will not issue building permits until the fire hydrants are in place and charged.
Compartmentation and security
One of the most significant factors affecting the susceptibility of construction sites to large fires is the lack of compartmentation. This is provided in a finished building particularly those designed to meet a specific level of resistance by the walls, floors, doors, and other separating features slowing or preventing fire spreading from one room to another.
Therefore, if a fire starts in a building during an early phase where there is limited compartmentation in place, there is often little to prevent its spread. The construction sequence can be modified to provide limited compartmentation during construction. For example, the installation of gypsum board on one side of interior walls in key locations, such as between residential or commercial units, may slow a fire’s growth, allowing emergency personnel to manage it before an entire project is lost.
One hazard not currently addressed by building codes is arson. For the public’s protection, many municipalities require fencing or barricades around construction sites. Such features can also help prevent unauthorized access, controlling site entry of intentional or accidental fire-starters. Good site perimeter control and other security provisions can assist in reducing financial losses, including material and equipment theft. In addition to perimeter control, covering windows and installing temporary doors can secure the building after the first storey has been constructed, making unauthorized entry difficult. Other useful security measures include good lighting, electronic monitoring, and video surveillance.
NFC contains provisions requiring unobstructed access be maintained to onsite fire equipment such as fire hydrants, portable extinguishers, and fire department connections for standpipe and sprinkler systems. For instances with fencing, NFC requires provisions must be made for fire department equipment and personnel access. This can be accomplished in various ways, including key boxes installed at known or identifiable accessible locations.
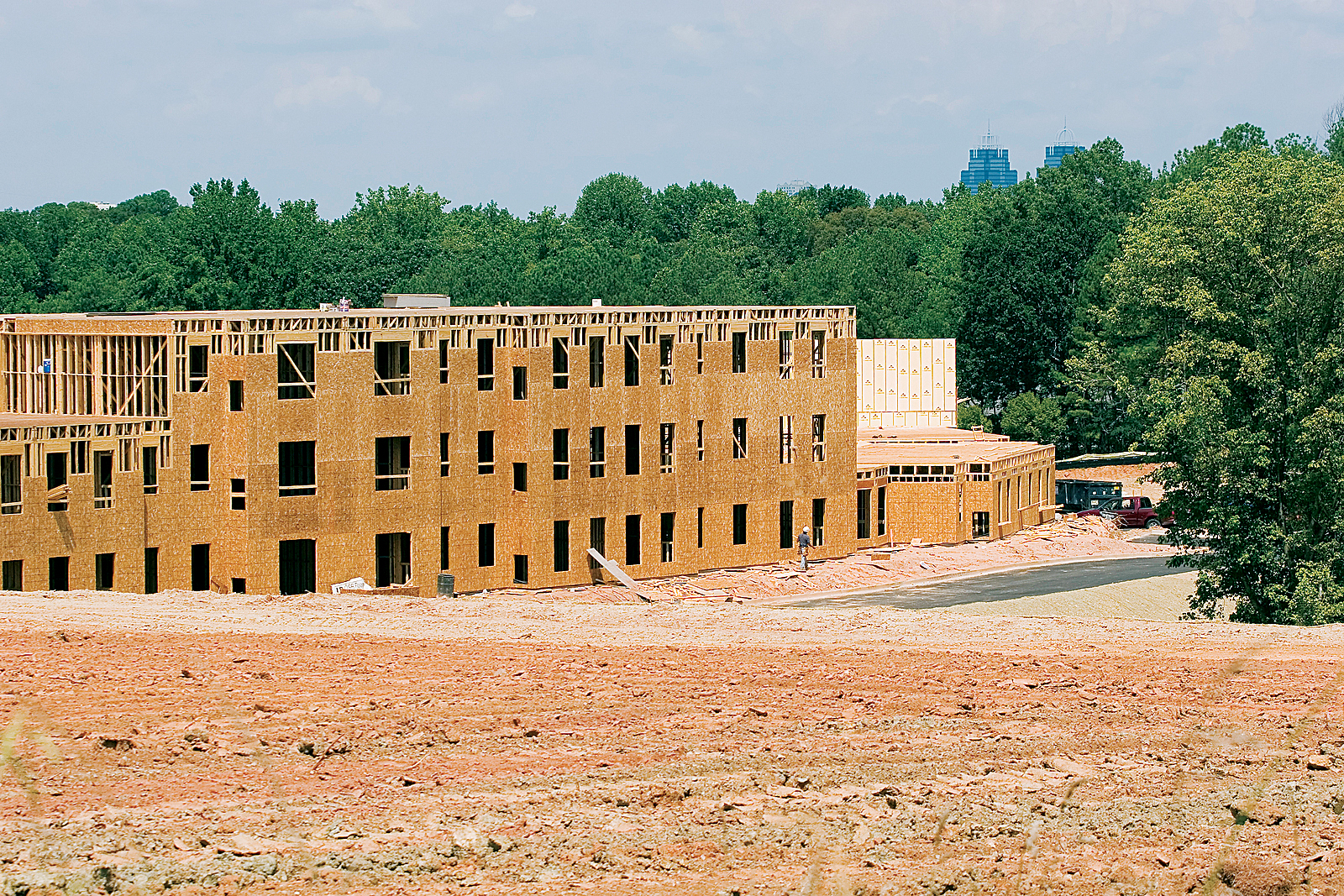
Temporary or permanent roads of appropriate width, free of obstructions (including parked vehicles), and made of all-weather material are important for efficient access of fire apparatus.
Site-specific considerations
As cities adopt policies encouraging densification, infill projects become increasingly common. During infill project construction, it may be necessary to consider additional ways to minimize the exposure to adjacent structures in the event of a fire. NFC states protection must be provided for adjacent structures that would be exposed to fire originating from a building under construction. For instance, temporarily covered window openings facing, and close to, adjacent structures may provide limited protection.
Alternatively, in large residential developments, some local by-laws or insurers require ‘fire breaks’ when numerous houses are under construction. As an example, a by-law may require no more than six consecutive lots in a development can be simultaneously built, and construction on the seventh lot cannot begin until the façade, roofing, and windows are installed on adjacent structures. This limits potential for fire spread and damage.
Fire safety planning
NFC requires all construction sites have a written fire safety plan. The FSP sets out everything that will be done on the project to minimize fire risk and protect workers onsite. It should take into consideration all relevant regulations to reduce the risk and impact of fire, and include as much information as possible regarding the expected stages of planned fire protection systems and procedures.
Consultants specializing in fire safety planning should be capable of carrying out a fire risk assessment of the site at various stages, identifying fire hazards, and mitigating factors and probable fire scenarios that can vary during the course of construction operations.
The key steps in the creation of an FSP are:
- Site analysis—including risks and factors arising from construction, operations, implementation schedule, and phases of work.
- Development of necessary policies, procedures, and systems to prevent and control risks.
- Analysis of available resources (on and off the site) including allocation of key staff to fire and emergency duties. This includes consultation with emergency services to obtain feedback and address concerns.
- Development of emergency protocol procedures for various individuals with roles and responsibilities in a fire emergency. This includes procedures for sounding the alarm, calling the appropriate fire and emergency services, and shut down of certain hazardous operations/services.
Conclusion
Developing a culture of fire safety on any construction site can take time, money, and effort. After all, personnel need to be trained, changes may need to be made to some long-standing construction processes and procedures, and maintaining good communication with fire safety stakeholders can be time-consuming. It is not always easy, but the benefits of taking these steps can outweigh the effort.
Fire safety on a construction site is all about teamwork. Explaining why certain policies and procedures are being implemented can go a long way to assuring workers understand their importance and the benefits to the project.
A work environment focused on fire safety can pay off in many ways. A well-implemented FSP based on a thorough analysis of fire risks can demonstrate to an insurance company the project managers and owners are committed to operating a safe site, which may result in better insurance rates. A reduction in fire incidents can also increase productivity and decrease direct and indirect financial losses related to a slow-down—or even shut-down—in the construction schedule. Increased avoidance of slowdowns or shutdowns of a site due to fire incidents also means continued employment and safety for everyone involved.
Notes
1 For more, see “Structure Fires in Vacant or Idle Properties, or Properties under Construction, Demolition or Renovation,” published in 2001 by the National Fire Protection Association (NFPA). (back to top)
Steven Craft, PhD., P.Eng., is a principal engineer with CHM Fire Consultants Ltd., and an adjunct professor in the fire safety engineering program at Carleton University(Ottawa) where he teaches courses in wood engineering, fire dynamics, and wood structures and fire safety. His professional interests are focused on performance-based fire safety design for buildings, fire testing, and forensic analysis of large loss fires. Craft can be contacted at steve.craft@chmfire.ca.
Ineke Van Zeeland, M.Eng., ASFPE, is manager of codes and standards at the Canadian Wood Council (CWC). Her areas of expertise include fire research, fire safety engineering, standardized fire safety and performance testing, building product certification, and building code and standards development. Van Zeeland participates in several technical committees for fire test standards and building codes, including theUnderwriters Laboratories of Canada (ULC) S100A Fire Test Committee, the National Fire Protection Association (NFPA) Fire Committee, the ASTM E05 Fire Test Committee, the Ontario Building Code (OBC), Part 3 Advisory Committee, and various task groups under the Standing Committees of the Canadian Commission on Building and Fire Codes. She can be reached at ivanzeeland@cwc.ca.
Steven Street has worked with Wood Works!, an industry-led, federally and provincially supported CWC project since 2007. In his role of technical director, he provides information and technical support to design professionals, helping facilitate the increased use of wood products in commercial, industrial, and institutional construction. Street commonly guest lectures at colleges and universities on issues such as mid-rise construction and cross-laminated timber, and is a regularly invited speaker at technical events presented by the Ontario Building Officials Association, Ontario Wood Truss Fabricators Association, and the Canadian Wood Council. He can be contacted via e-mail at sstreet@wood-works.ca.