Controlling thermal bridging with single-component wall assemblies
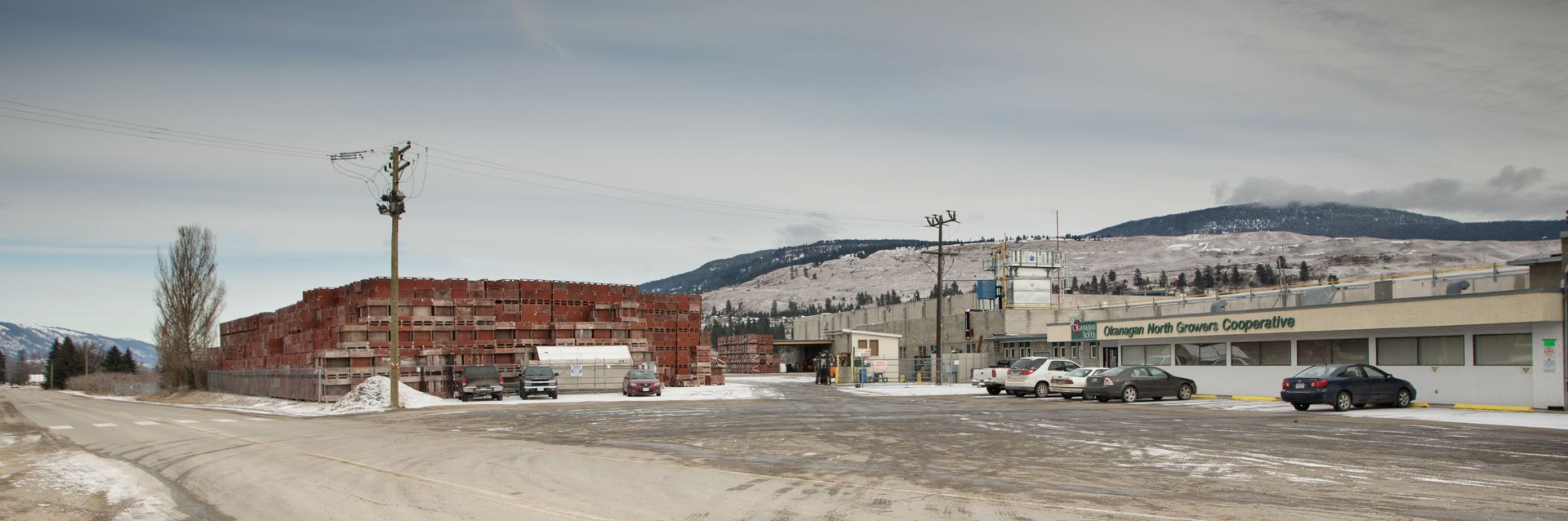
Thermal bridging on the roof
An integrated wall and roof panel system has many benefits. Standing seam insulated metal roof panels are rigorously tested to ensure they remain both airtight and weather-tight over a building’s life.
A single-component insulated metal panel roofing system provides enhanced performance, design flexibility, and a fast-track construction installation method. However, above all these benefits, it also offers a high R-value thermal performance and superior airtightness with no thermal bridging. It can also result in energy savings higher than given by conventional built-up roofing (BUR) systems, as a result of the thermal performance provided by each panel’s polyiso core.
Standing-seam insulated metal panels have resistance to outdoor corrosion. Unlike conventional roof systems, these panels will neither crack nor peel when exposed to the sun and rough weather. Insulated metal roof panels also eliminate the cost of re-shingling or replacing a BUR system. Made with recaptured low-weight metals, they weigh only 1.36 kg/m2 (3 lb/sf), reducing transport and installation energy costs.
Weather conditions are a significant concern in the construction process with most exterior envelope systems. However, IMPs can be installed any time of year because they create non-reservoir walls that do not absorb water. Exterior walls made of brick, precast concrete, or tilt-up absorb rainwater. If moisture enters a wall cavity and is not drained or vented, mould and mildew growth usually occurs.
The green factor
Installing the insulated metal panels will create superior airtightness and moisture control, as well as offer high R-value. It is the crucial initial design step if a building is to achieve Leadership in Energy and Environmental Design (LEED) certifications.
A roof built with insulated metal panels will help to reduce operational heating and cooling demands and, as a result, contributes to lowering the carbon footprint of a building. This can contribute to the LEED rating program’s Sustainable Sites (SS) credits, earning up to two points for reducing urban heat islands. IMPs can also satisfy requirements for the EnergyStar and cool roofs programs for reflectivity benefits. These metal panels, along with
their polyiso core, are completely recyclable, which offer multiple end-of-life reuse options—including creation of new IMPs.
Due to the fact IMPs are installed with a one-step method, onsite work hours can be reduced by as much as 50 per cent when compared to multi-component roof systems. Some insulated metal panels use a hidden-clip design that minimizes the need for through-fasteners that would otherwise penetrate the external facing, resulting in considerable degradation of panel performance.
Specialized buildings
The resolution of thermal bridging issues should be the leading concern in the design of all structures made for the built environment. However, there are certain building types where closing all thermal bridges is the primary concern. This is especially the case with cold-storage buildings.
For example, the BC Tree Fruits Cooperative (formerly Okanagan Tree Fruits Cooperative) in British Columbia was hampered by aging and out-dated facilities, combined with higher food safety standards that led to rising production and operating costs.
The existing refrigerated storage systems were antiquated and inefficient from an energy utilization standpoint. They required major upgrades with a more sustainable technology in order to significantly improve the quality of the product.
It commissioned TriCorp Developments (Vancouver Island) to assist with facility performance measures aimed at maximizing its growers’ fruit returns. TriCorp achieved this through creating 23 controlled atmosphere storage rooms at the group’s Winfield packinghouse. TriCorp, which specializes in the design and build of highly specialized controlled atmosphere rooms, specified IMPs to fulfil the insulation requirements and esthetic needs for a complete building renovation and upgrade. This reduced the building’s carbon footprint, lowered maintenance costs, and gave the building a modern appearance.