Controlling thermal bridging with single-component wall assemblies
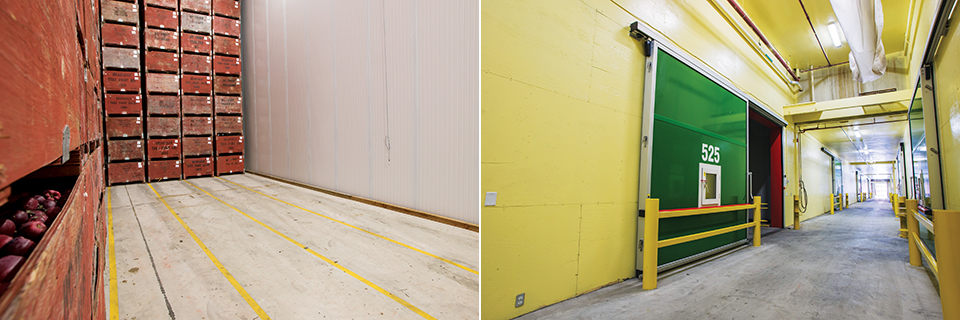
Even with its thermal performance capability, many designers choose to specify insulated metal panels because the installation process is simplified. Exterior cladding systems that require multiple components are more prone to construction delays—partly due to a need for scheduling multiple trades. A typical exterior insulated finish system (EIFS) requires at least 10 separate components and must be fabricated onsite. IMPs are a single-component product, which arrive ready to install, allowing for faster construction.
IMPs can be installed in almost any kind of weather without risk to system integrity, as opposed to multiple installation steps required for other insulated wall and roof assemblies. Insulated metal panels are installed with a concealed fastener system further reducing the number of field-assembled components. With this simplified process, IMPs can be erected quickly even for large commercial and industrial facilities.
When insulated metal panels are joined together with an interlocking system, the result is a solid exterior wall that reduces thermal bridging. Using these integrated side joints makes it easier to incorporate additional components such as sunshades or window systems. This seamless integration creates a thermally efficient building envelope with an esthetically pleasing appearance, weather resistance, and an increased lifespan.
The Ontario dilemma
To meet the Ontario Building Code’s (OBC’s) Supplementary Standard 10 (SB-10), “Energy Efficiency Supplement,” which governs thermal efficiency, many designers specify a costly high-efficiency mechanical system.
Initially adopted in 2007, OBC was revised in 2012. This excerpt is from the revision and states when thermal bridging regulations can be ignored:
Division 3, Chapter Two, Revision to American Society of Heating, Refrigerating, and Air-conditioning Engineers (ASHRAE) 90.1-2010, Energy Standard for Buildings Except Low-rise Residential Buildings, 5.5.3.7/8:
For the purposes of Section 5, the effects of thermal bridging are waived for:
- Continuous steel shelf angles (or similar structural element) used to support the building façade provided there is a thermal break.
- Structural connections of load-bearing elements where a thermal break cannot be achieved.
- Exposed structural projections of buildings where the total cross-sectional area of the exposed element does not exceed 2%.
- Ties in masonry construction, flashing, and top exposed portion of foundation walls, provided the exposure does not exceed 200 mm [7.8 in.].
However, this code might need further revisions again because all thermal bridges should be resolved, not ignored. Few new buildings in Ontario meet the requirements of the provincial code’s SB-10 energy efficiency requirements. This is because rather than find a way to reduce energy use, some projects have been designed with high-performance HVAC equipment to compensate for poor thermal performance.