Controlling condensation from air leakage and vapour diffusion
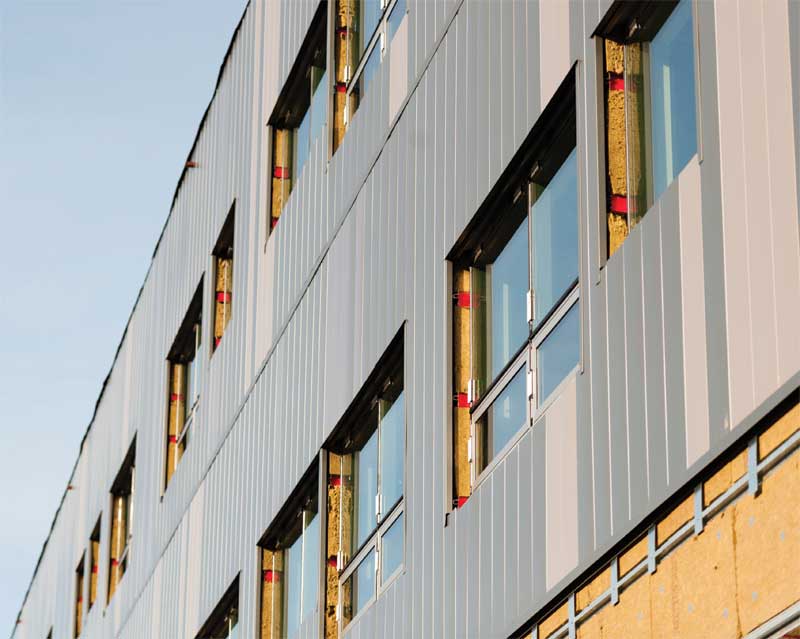
By Vincent Chiu
Water is the most significant factor in the premature deterioration of our buildings. Excessive moisture accumulation on porous materials can lead to water penetration, freeze-thaw damage, efflorescence, cracking, and façade soiling. Further, water penetration or interstitial condensation may lead to the chemical breakdown of organic materials (e.g. wood), failure of structural systems and fasteners, mould growth, and damage to interior finishes and furniture.
There are three main sources of moisture that affect buildings:
- exterior moisture (e.g. rainwater, groundwater, surface runoff, and melting snow);
- interior moisture resulting from occupants and occupant use (e.g. perspiration, respiration, and activities); and
- built-in moisture (i.e. manufacturing, construction, and naturally occurring moisture).
The three strategies to manage water penetration are known as the Three Ds: deflection, drainage, and drying. For example, the bulk of exterior rainwater can be deflected away using overhangs, flashings, and drip edges. Any rainwater not deflected can be drained away using drainage layers within the wall assembly, and away from the foundation wall using drains. Water capable of bypassing the two previous strategies must be capable of drying.
Numerous techniques have been employed by designers and builders to deal with bulk water. However, the transport of moisture through air or vapour diffusion is trickier and less understood. Condensation from air leakage and vapour diffusion on cold condensing surfaces within a wall assembly can lead to significant structural and indoor air quality (IAQ) issues that may cost more to repair than to prevent.
Controlling air and vapour flow
More than a half-century ago, assemblies did not require vapour barriers. They dried both outward and inward, were capable of managing leaky windows without flashing, and could be rained on during construction. The wall assemblies were also poorly insulated—this was actually the key to their moisture management, as heat flowing through the assembly helped dry the assembly of any built-in or accumulated moisture. The interior moisture levels were also low from the high dilution rates due to stack effect and the leakiness of the enclosures. (See Joseph W. Lstiburek’s “Macbeth Does Vapour Barriers,” published in the November 2013 Building Science Insights [vol. 73].)
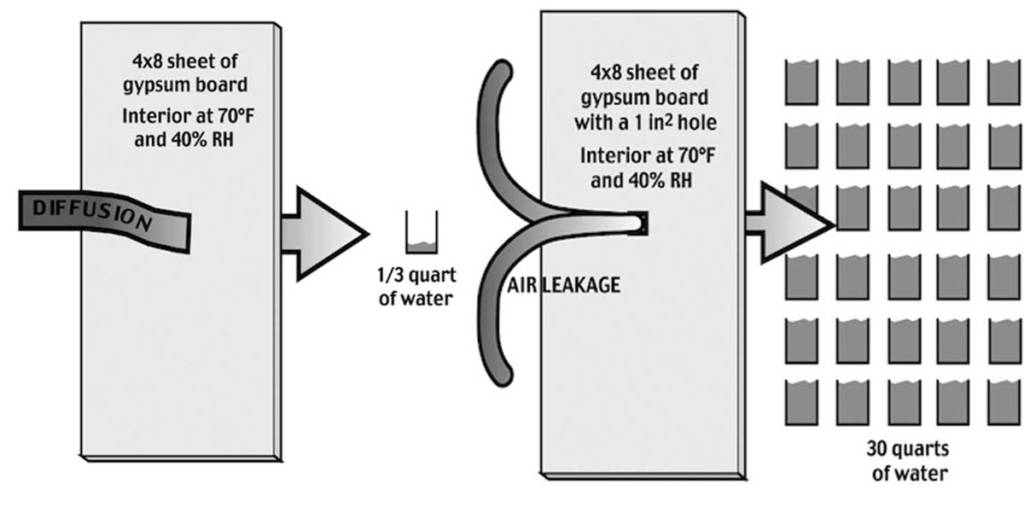
Images courtesy Building Science Corporation
A trend toward tighter enclosures with fewer air changes has resulted in lower dilution rates and higher levels of interior moisture. This, coupled with cavity insulation (which resists the flow of heat through the assembly), reduces the wall’s drying potential. Therefore, interior moisture should be handled at the source using ventilation fans and through the proper design, installation, and operation of the building’s HVAC system.
Interior moisture that cannot be eliminated must be controlled by employing an effective air barrier and vapour retarder/barrier. Despite the fact these two barrier systems are neither the same nor interchangeable, there is sometimes confusion in the industry, as a single material is often used for both functions.
Controlling the flow of air is more important than controlling vapour diffusion, as seen in Figure 1. During a heating season, air leakage through a sheet of gypsum board with a hole in the middle will result in 28.4 L (30 quarts) of water. Vapour diffusion through a solid sheet of gypsum board (i.e. no hole), however, will only result in 0.3 L (1/3 quart) of water.
Therefore, fastidious air-sealing of the wall assembly from the interior is critical in mitigating moisture-related problems in Canada’s colder climate. Caulked, glued, or gasketed gypsum board to framing can serve this purpose while still being vapour-permeable, allowing the wall to dry toward the interior. Coating the gypsum with a semi-permeable finish such as latex paint is usually adequate in controlling vapour diffusion in most buildings. However, vapour barriers such as polyethylene sheet are often required by codes (e.g. National Building Code of Canada [NBC]) and also used as the interior air barrier.