Controlling airflow for a healthy building
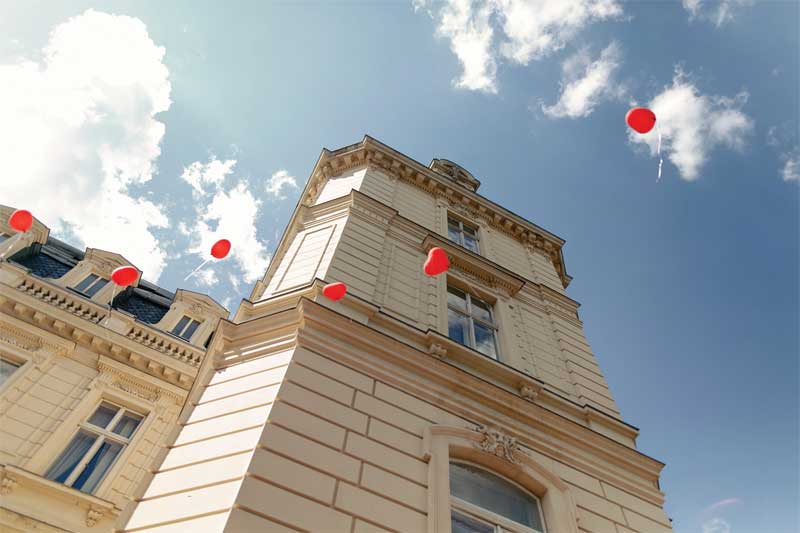
By Jason Smith
Balloons evoke childhood memories of a trip to the circus or a day spent at a local amusement park—the air that fills them is fundamental to life itself. Ironically, the same air that brings ‘life’ to a balloon (and us) causes headaches or worse for building owners, architects, and specifiers. In fact, air flow is the dominant force behind moisture transmission, spread of smoke, indoor air quality (IAQ) issues, and microbial deposition within building spaces.
Air barriers were developed to control airflow into and out of the building envelope. This article will help readers understand how controlling a building’s airflow through the use of coatings can keep the bad air out and the good air in.
Air quality impact of airflow leakage
Apart from the obvious means of ingress and egress (i.e. windows, doors, and ductworks), air flows through building materials by means of pressure differentials acting from the outside of the building inward and vice versa. The three sources of pressure differential are:
- chimney effect;
- wind pressure; and
- fan pressure. (This comes from North Carolina State University’s web article, “Infiltration [Also Called Air Leakage] Defined.” For more, visit energy.ces.ncsu.edu/infiltration-also-called-air-leakage-defined.)
The chimney effect, also known as stack pressure, occurs in all buildings, but especially those located in areas with hot summers and cold winters. In the winter, warm interior air rises and escapes through vents and windows, reducing the pressure at the base of the building. This creates a pressure differential on the wall’s surface. Even buildings without operable windows are never completely sealed—the air can flow through cracks under doors or through unprotected cracks in the walls. At the same time, higher pressure is exerted on the interior walls of the higher floors compared to outside. In the summer, the effect is reversed.
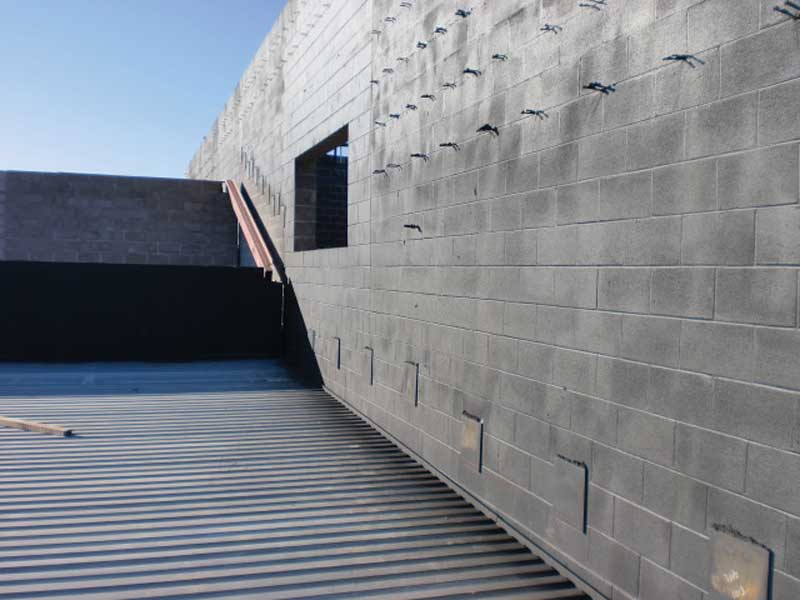
Images courtesy The Garland Company
The cooler indoor air sinks and draws hotter air from the vents on the roof. More pressure is exerted on the interior walls on the lower floors compared to the higher floors. These small but important pressure differentials are directly proportional to both the height of the building and the temperature difference between the inside and outside air.
The second source of pressure differential is wind, which can move into the building through cracks in the window seals or in the concrete or brick façade. Wind pressure causes the largest pressure differences on exterior walls, often 500 to 1000 Pa (about 10 to 20 psf), with gusts increasing the difference by as high as 2 to 2.5 times.
Fan pressure, the third major source, is caused by HVAC fans as they exhaust to introduce and circulate the air within a building. This pressure can be controlled positively (to meet the demands of stack-effect buildings, especially in tall structures) or negatively (to keep moist air from entering through exterior walls or the roof). The pressure differences caused by fan pressure are low, but must be considered during building design.
These sources of pressure difference create a means for air to flow. In most cases, the issue is not so much the air coming into the living or working space, but rather what that air carries with it. Air pressure differentials are capable of bringing hundreds of times more water vapour through a block of concrete than would otherwise naturally diffuse through. The vapour can carry micro-organisms that are then deposited within the building. Also, pollutants and allergens can be carried into the building through cracks via airflow, which create problems for people with asthma or other respiratory issues.