Condensation on curtain wall surfaces: An investigation
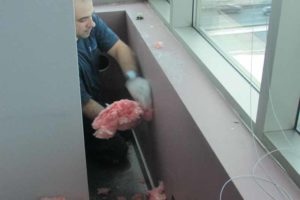
Analysis
The installation of batt insulation within the wall cavities of interior finishes is inadvisable, but is not an uncommon practice. Certain designers and builders sometimes feel compelled to stuff all wall cavities with insulation. However, experience has shown the placement of batt insulation within an interior wall cavity requires careful analysis and may significantly impact the condensation resistance of the wall assembly.
In regards to curtain wall installations, experience has also shown the placement of batt insulation within the wall cavity of interior finishing will affect condensation performance. The batt insulation isolates the curtain wall from the warming effects of the interior heated air. Consequently, a reduction of interior curtain wall surface temperatures within the spandrel area occurs. Given the thermally conductive nature of metallic curtain wall materials, the cooling of adjacent curtain wall components would be expected. Interstitial condensation may also occur within the batt insulation or on hidden interior curtain wall surfaces within the spandrel area if the dewpoint temperature of interior air is reached.
With interior air at 21 C (70 F) and 30 per cent RH, a computerized condensation analysis of a simplified representation of the curtain wall construction indicated the formation of interstitial condensation within the batt insulation at a rate of 1 g/m2/day at exterior temperatures of –17 C (1.4 F). The analysis further indicated the rate of formation of condensation increased to 8.5 g/m2/day as the exterior temperature approached –23 C (–9.4 F).
When the analysis was repeated for an interior air condition of 21 C and 25 per cent RH, interstitial condensation was reduced within the batt insulation to a rate of 0.7 g/m2/day at exterior temperatures of –17 C. The rate of formation of condensation also decreased to 1.9 g/m2/day as the exterior temperature was decreased to –23 C.
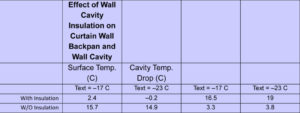
The analysis also indicated the presence of batt insulation within the wall cavity would also produce a temperature drop of approximately 16.5 to 19 C (29.7 to 34.2 F) within the assembly, resulting in a corresponding backpan metal surface temperature ranging from 2.4 to –0.2 C (36.3 to 31.6 F) for an exterior temperature varying from –17 to –23 C, respectively (Figure 7).
In comparison, a similar analysis of the wall assembly undertaken with identical temperature conditions and with the batt insulation removed from the wall cavity indicated a temperature drop of approximately 3.3 to 3.8 C (5.9 to 6.8 F) across the wall cavity. As a result, the backpan metal surface temperature would range from 15.7 to 14.9 C (60.2 to 58.8 F) for an exterior temperature of –17 C and –23 C, respectively (Figure 7).
Based on these comparisons, it became clear the presence of batt insulation within a wall cavity significantly reduced surface temperatures of curtain wall components and increased the potential for condensation and ice formation.
The computations also demonstrated the benefits of having reduced humidification levels during periods of extreme cold. The simulations indicate for a reduction of five per cent RH, interstitial condensation would only occur for exterior temperatures at or below approximately –22 C (–7.6 F).
The localized cooling effect produced within the spandrel sections of the curtain wall likely contributed to the cooling of apparent surfaces and the formation of condensation. Large, thermally conductive pathways provided by the mullions at the building corners likely provided a heat flow path to the colder, opaque sections of the curtain wall assembly, much like a heat sink. This phenomenon further decreased the temperature of exposed surfaces.
The computer simulations also suggested a reduced risk of condensation for the flat areas of the curtain wall assembly and condensation was not visibly apparent during site verifications. It was speculated the reduced levels of condensate production in the typical wall areas was actually stored and frozen within the insulation during periods of intense cold and these areas would subsequently thaw and dry out during warmer periods.
At the building corners, the compounding of condensation-promoting factors was sufficient to produce conditions that saturated the batt insulation. Once sufficient moisture had accumulated, moisture migration along surfaces occurred to eventually produce an accumulation on sills.
This time lag between the visible identification of condensation and the conditions that actually produced it may have contributed to the misdiagnosis of the condensation issue in the past.
Corrective work
To improve condensation resistance at the building’s exterior corners, it was clear the batt insulation within the interior wall cavities would have to be removed. A building corner was selected on the test floor for the removal of the wall cavity insulation and additional testing. To minimize the effects of heat sinking to levels above and below the test floor, the insulation from the wall cavities on those levels was also removed.
To gain access to the wall cavity insulation at the building corners and while minimizing cost and disruption to tenants, the complete dismantling of interior wall finishes was not an option. In lieu of the selective dismantling of finishes, a series of 102-mm (4-in.) diameter holes was cut within the interior wall finishes of one exterior corner below the curtain wall assembly and behind the obstructing structural columns at three floor levels of one particular building corner (with the middle level being the test floor). From these openings, any batt insulation within arm’s reach was extracted (Figure 8). Following removal of the insulation, round plastic vents were installed within the circular openings as an attractive finishing and to promote ventilation of hidden curtain wall surfaces (Figure 9).
The insulation situated within the suspended ceiling space was also removed by partially dismantling sections of the drywall. Following removal of the insulation, the drywall within the ceiling space was reinstalled.
The modifications to the existing wall assembly were completed in preparation for a period of sustained cold exterior temperature, when additional performance evaluations were undertaken.