Condensation on curtain wall surfaces: An investigation
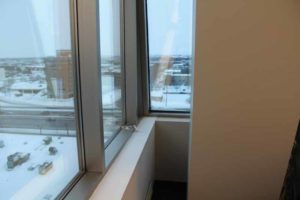
The investigation
Thermal scans and point surface temperature measurements confirmed the greatest condensation potential occurred on the curtain wall interior surfaces at the building’s exterior corners.
Interior surface temperature measurements at those corners obtained during periods of extreme cold (–18 C [–0.4 F]) revealed temperatures as low as –0.1 C (31.8 F) for areas with minimal or no perimeter heating. In areas where heating systems were in operation, temperatures as low as 2.4 C (36.3 F) were measured. In comparison, for similar surfaces within typical areas of curtain wall, temperatures were measured to be approximately 4 C (7.2 F) warmer. These measurements were taken on the surfaces of vertical mullions, at the junction of vertical and horizontal mullions (nearest sealed glass unit). The inside glass surface temperatures were consistently measured to be higher than the coldest aluminum surface temperatures.
The following specific issues were identified during the investigation as being problematic and likely to promote condensation on interior curtain wall surfaces at the building corners. Surprisingly, many of these issues are unrelated to the design of the curtain wall system itself.
Building geometry
The laws governing heat flow dictate the exterior corners of any building present an inherent thermal weakness due to geometry. During winter, an exterior corner mullion assembly creates a condition in which more exterior surface area is exposed for cooling in comparison to the surface area available from interior surfaces. Consequently, an exterior corner mullion assembly is generally subject to a thermal penalty in comparison to a typical wall mullion. As a result, slightly colder interior surface temperatures are expected. The opposite is generally true for interior corners where more surface is exposed—as a result, comparatively warmer temperatures are expected.
Interior building structural obstructions
The placement of the building’s structural columns in close proximity to the exterior corners of the building envelope was found to impede air circulation in those areas. Poor air circulation due to interference by the building structure was also found to be a contributing factor in reducing the energy available to heat interior wall surfaces at the building corners. Thus, building structural obstructions were a significant contributing factor to the low surface temperatures recorded (Figure 4).
Lack of perimeter wall heating at corners
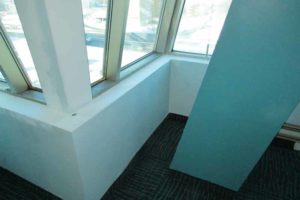
Perimeter heating was notably absent at the corners of the building. It is speculated the obstruction presented by the building structure may also have contributed to a decision not to install heaters directly at the building corners. In some instances, the temperature setpoint for the perimeter heating system was adjusted to a lower setting by the occupant and the existing heaters were found to not be in operation. In some cases, equipment failure was suspected and heating capacity was further reduced. Interior air temperatures at corner offices were measured as low as 18 C (64.4 F) due to these issues. The lack of perimeter heating was identified as one of the most important contributing factors in low interior curtain wall surface temperatures (Figure 5).
Erroneous HVAC RH measurements
Measurements of interior air conditions obtained at several floor levels were compared with values reported by the control system from the floor-level air returns. Lower than actual RH level readings were reported by the HVAC control system. In one instance, approximately 10 per cent RH error was noted to exist between a reading reported by a humidity sensor located in a return air duct and measurements made with a wet/dry bulb psychrometer within occupied spaces. As a result, a condition of over-humidification was noted to exist in certain areas.
Humidification schedules
As part of the normal building humidification process, humidification levels were initially found to be maintained at 30 per cent RH during periods of occupancy, regardless of exterior temperature levels.
Ventilation and heating system schedules
As an energy conservation measure, ventilation and perimeter heating systems were found to be in limited operation during unoccupied periods or not in operation in areas of certain floor levels due to vacancies. These practices were also found to be maintained under conditions of intense cold.