Concrete moisture and water-based adhesives
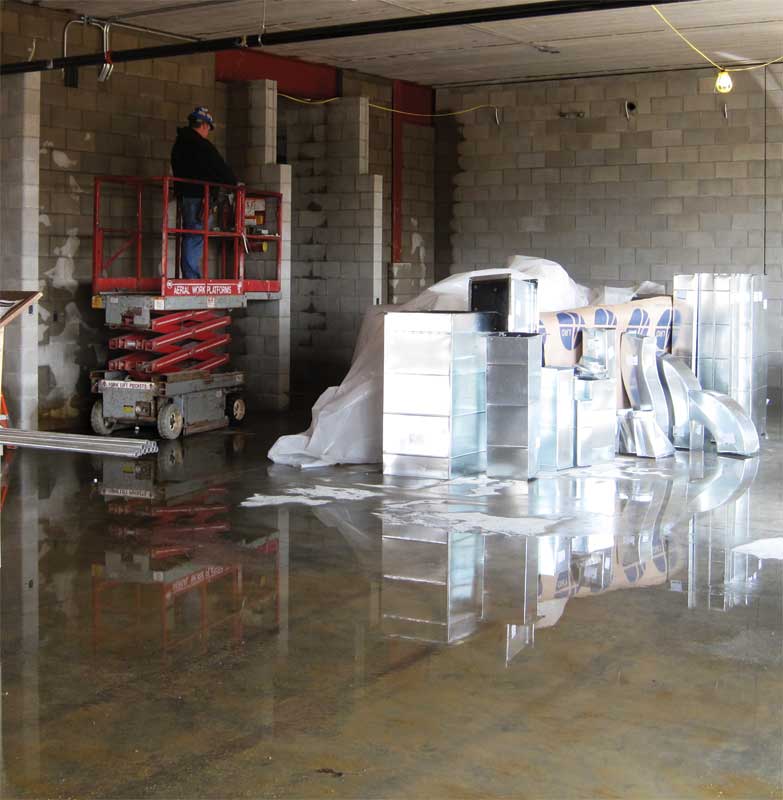
Rewetting concrete
Providing an enclosure to protect concrete from rainwater has already been discussed. The contractor must also take precautions against rewetting the concrete with construction operations. Using a power water-sprayer to remove membrane-forming curing compounds will introduce moisture into the slab and sets back the start of moisture-sensitive adhesives and floorcoverings.
Curing materials
Curing is the process of holding mixing water in the concrete long enough for near-complete hydration of the cement with water. However, to restart evaporation, the curing materials must be completely removed. Plastic sheet has the advantage in that once it is removed, evaporation begins immediately. Membrane-forming curing compounds may be more appropriate, depending on circumstances, but removal of the compound requires some mechanical means if the floor is completely sheltered from sunlight.
Moisture testing
Excess water gathers in the pores of concrete, first as a liquid (when the concrete is wet), then as moisture vapour (during the curing process). Surplus moisture vapour not hydrated with cement is locked in the gel and capillary pore structure of the hardened concrete, taking months to evaporate to levels safe to apply adhesives. Moisture vapour produces a measurable level of relative humidity in the concrete that can serve as a good barometer of when the concrete is safe for the application of moisture-sensitive adhesives.
The anhydrous calcium chloride test to establish the moisture vapour emission rate (MVER) was once considered the industry standard for determining the moisture in concrete, but its failure to predict the incidence of water-based adhesive failure has become well-known. Manufacturers have been slow to recognize the limitations of this test and have not universally revised their installation instructions to direct the use of the more reliable RH tests. Today, the MVER test is considered a superficial methodology, measuring, at best, the moisture in the top 25 mm (1 in.) of the concrete while overlooking the relative humidity deeper within the slab that will eventually come to
the surface. (A Concrete Construction article entitled, “Slabs on Grade Concrete Floor Moisture Tests,” has more. )
The quantitative RH probe test (which is described in ASTM F2170-11, Standard Test Method for Determining Relative Humidity in Concrete Floor Slabs Using In-situ Probes) measures the internal RH of the slab. Today, more manufacturers require RH testing; but if the RH test is not included in the instructions, a meeting becomes necessary to resolve the issue.
The RH test equipment is expensive and requires training to be done properly. This is better done by an independent agency with the calibrated equipment and skills to perform the test. Such agencies should be contracted by the owner and not the contractor; further, they should not be given ‘go or no-go’ authority—that judgement must remain the responsibility of the floorcovering installer so as not to undermine the risk relationship between the parties.
Conclusion
All parties bear responsibility for the incidence of moisture-related floorcovering failures following the introduction of water-based adhesives. Most manufacturers were slow to connect the dots and did not use their network of sales organizations to get architects and engineers involved in solving the problem and few manufacturers stayed on top of the connection between water-based adhesive failures and the limits of the MVER test to prevent them. At the same time, many architects and engineers did not recognize that standards for designing concrete that made structural sense were not necessarily effective at preventing floorcovering failures.
Further, few owners and construction managers faced up to the adjustments in the sequence of construction and the duration required to get concrete dry enough for applying the floorcovering. The wait-time duration may not always fit well into the owner’s occupancy expectations, but it is necessary if the owner is to avoid inheriting legal responsibility for floorcovering failures. Concrete contractors must exercise care installing the vapour barrier and resist the temptation to add water to concrete at the site. Finally, floorcovering contractors must insist on waiting until the RH tests prove it is safe to install the floorcovering or request a written directive from the owner’s representative to proceed under adverse conditions.
Paul Potts is a technical writer, owner’s representative, and construction administrator. He has worked in the construction industry as an independent contractor and administrator for architects, engineers, and owners in Michigan. Potts can be contacted via e-mail at paulpotts1@comcast.net.