Concrete moisture and water-based adhesives
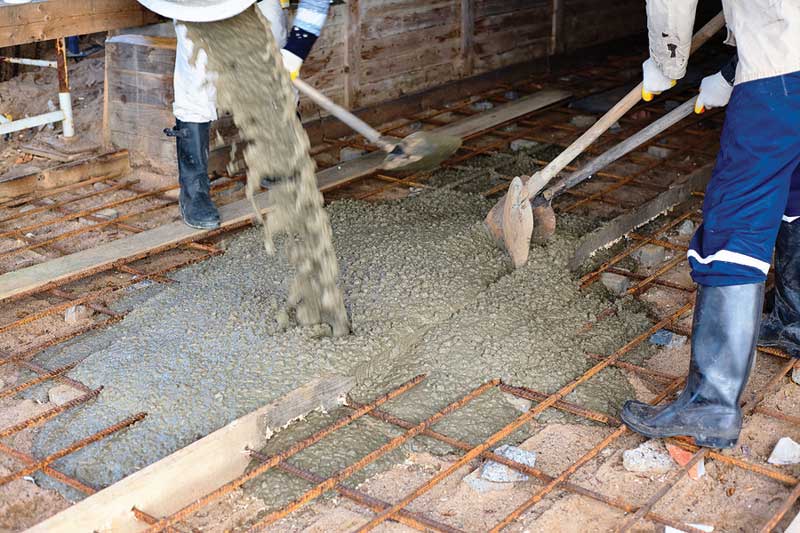
Photo © BigStock.com
Many architects and structural engineers design concrete as though strength and slump were the only important factors, even though a lower strength requirement is directly related to excessive surplus water—the lower the strength, the higher the water content. From a structural standpoint, slab-on-grade concrete with 24 MPa (3500 psi) compressive strength is adequate for the expected loads in commercial buildings and eases placement; however, it will have a w/c ratio of 0.6, with a lot of surplus water. The extra water increases the shrinkage potential of concrete, making it prone to cracking and curling, and increases the wait-time for drying concrete by months.
An optimal water-cement ratio of 0.45 will result in an average compressive strength of 31 MPa (4500 psi), with enough water for complete hydration of cement and adequate surplus water to compensate for moisture lost to evaporation before curing is started. With this w/c ratio, there will be minimal surplus water left behind to evaporate before scheduling the application of floorcovering. Under these conditions, curing should be started as soon as possible because there is a minimal amount of moisture to lose. This optimal w/c ratio also results in concrete that is stiff and difficult to place. The architect or engineer should include a minimum requirement for a mid-range water reducer in the mix design to discourage workers from adding water at the site.
Ambient humidity and extra means of drying concrete
Concrete containers will hold water, but water vapour readily passes through concrete. Regardless of its appearance, bare concrete is constantly exchanging moisture with the atmosphere. When the relative humidity (RH) of the ambient air is greater than the humidity of the concrete, the latter absorbs moisture. (When the humidity conditions are reversed, the concrete absorbs moisture.) It may be useful to cover the slab with a temporary vapour barrier if high ambient humidity conditions are slowing the drying process.
The building HVAC equipment or separate portable dehumidification equipment is quite useful in any program to dry concrete and reduce the wait time. Even circulating the air is helpful, but running the air-conditioning system is much more effective. Unfortunately, lowering the air temperature also reduces the moisture carrying capacity of the air, reducing the efficiency of the system. Some building HVAC systems can be operated with both cooling and heating coils active at the same time; thus, cooling the air to wring out the moisture and reheating it to make it as efficient as possible. Portable dehumidifiers are also very effective at reducing the ambient air relative humidity and accelerating drying.
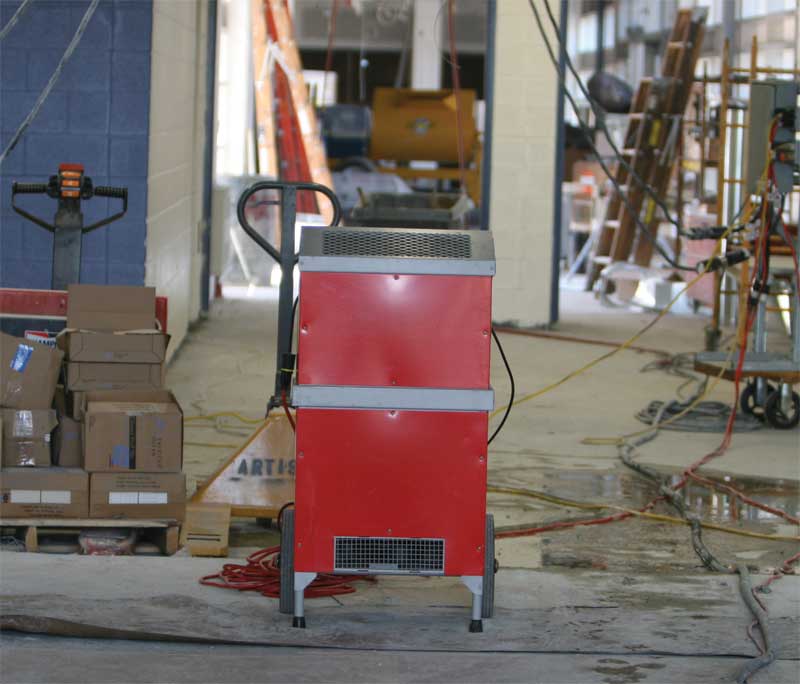
Photos courtesy Paul Potts
Soil moisture and groundwater
Soil moisture and groundwater move through concrete to the adhesive layer by capillary action—that is, the ability of a liquid to flow in narrow spaces (capillary pores) without the assistance of, and in opposition to, external forces like gravity. (A good working definition can be found at en.wikipedia.org/wiki/Capillary_action.) Moisture moves readily to the surface of concrete at a rate that depends on that material’s porosity and permeability. (It is worth noting these properties are improved using a low w/c ratio mix design.)
A functioning vapour barrier directly under the slab will cut off most soil moisture and groundwater from entering the slab. The American Concrete Institute (ACI) once recommended to place a blotter layer of aggregate between the vapour barrier and concrete, but this is no longer suggested except in specific circumstances. (For more on where to place the vapour barrier, see American Concrete Institute [ACI] Report 302, Section 5.2.3.2 [“Vapour retarder/barrier location”].)
A correctly placed vapour retarder or barrier will be continuously lapped 150 mm (6 in.), with taped seams, turned up at the edges, and provided with special fittings to waterproof mechanical and electrical pipes and equipment poking through the plastic sheet. ACI 302.1, Guide to Concrete Floor and Slab Construction, differentiates between vapour retarders and vapour barriers. Retarders are sheets up to 0.25 mm (10 mil) thick with a perm rating not greater than 0.2085 metric perms (0.3 U.S. perms). Vapour barriers are defined as sheets 0.38 mm (15 mil) thick with perm ratings of 0.00695 metric perms (0.01 U.S. perms). The thicker sheet is less likely to be punctured during construction operations. A single 13-mm (½-in.) hole in the vapour barrier will allow gallons of water to accumulate between the sheet and concrete.
There is an industry discussion taking place that for a vapour barrier to be defined as such, the material should have a rating of 0.0 metric perms (0.0 U.S. perms); all other products should be referred to as ‘vapour retarders,’ with an efficiency rating on a sliding scale from the most porous of 0.2085 metric perms (0.3 U.S. perms) down to 0.0. Plastic sheet used for a vapour barrier must meet the standards described in ASTM E1745, Standard Specification for Plastic Water Vapor Retarders Used in Contact with Soil or Granular Fill under Concrete Slabs. More detailed information on the selection and application of vapour barriers can be found in CSA A23.1, Concrete Materials and Methods of Concrete Construction, and ACI 302.2R, Guide for Concrete Slabs that Receive Moisture-sensitive Flooring Materials (i.e. requirements for vapour barrier materials that meet ASTM E1745 standards installed in accordance with ASTM E1643, Standard Practice for Selection, Design, Installation, and Inspection of Water Vapor Retarders Used in Contact with Earth or Granular Fill Under Concrete Slabs).