Concrete moisture and water-based adhesives
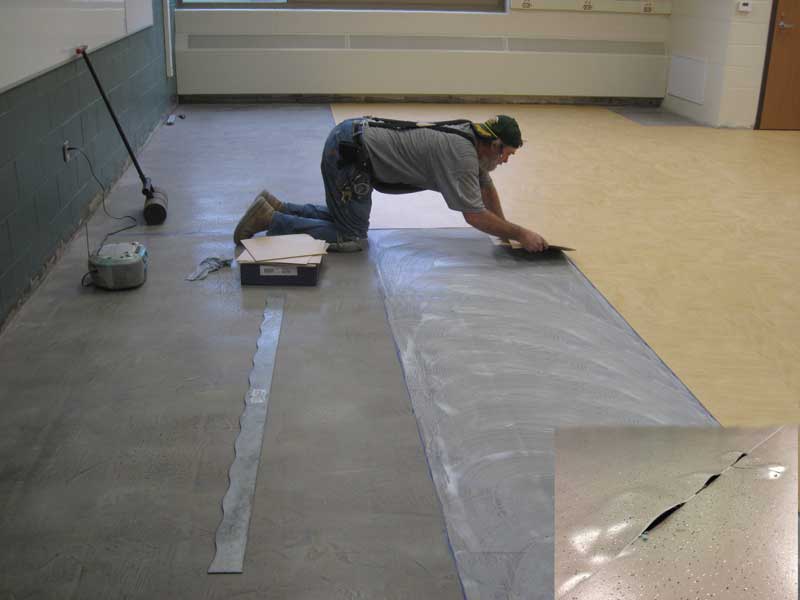
By Paul Potts
Government regulations requiring co-ordinated changes to manufacturing, design, and construction practices with a single regulation are difficult for the industry to assimilate successfully. The banning of solvent-based adhesives was one such example.
In 2009, along with similar regulations in the United States, Environment Canada issued new rules to reduce ground-level ozone—a significant source of smog. The rule committed both countries to banning products emitting volatile organic compounds (VOCs) in solvent-based adhesives (as well as hairspray propellants), as this contributed to ground-level ozone.
Floorcovering adhesive manufacturers responded by developing water-based adhesives that did not produce as many VOCs. Unlike the traditional solvent-formulated products that were unaffected by moisture, these new adhesives could be degraded by surplus moisture in concrete, causing delamination of the floorcovering. This anomaly caught many in the industry off guard, resulting in numerous floorcovering failures before awareness of the problem began to flow through the industry from manufacturers to designers, specification experts, and construction managers.
More than a decade after it became known water-based adhesives were susceptible to deterioration when brought into contact with surplus moisture in concrete, manufacturers, architects, engineers, construction managers, and contractors have still not made a thorough effort to minimize the risks of adhesive degradation through moisture contact. What is needed is an acceptance of responsibility by each party for their part of the solution.
Floorcovering manufacturers deserve some of the blame for this slow response. Few made an effective use of their marketing networks to communicate the dimensions of the problem to architects, engineers, and interior designers. Further, to this day, not all manufacturers have adopted clear and effective installation instructions to determine when the moisture conditions in the slab are safe for applying their products.
Construction schedule and the critical path
The most significant ramifications for the owner and the construction manager are the changes in the critical path and an increase in the duration before floorcovering can get started. The critical path must be organized to provide an enclosure for the concrete to prevent rainwater from rewetting the slab and continuously setting back the start date for floorcoverings.
Further, the duration in the schedule—waiting for the concrete to dry to a safe level—must be planned in terms of months, not weeks, regardless of any special techniques employed for shortening the wait-time. The traditional practice of scheduling floorcovering 30 days after concrete has cured is no longer advisable.
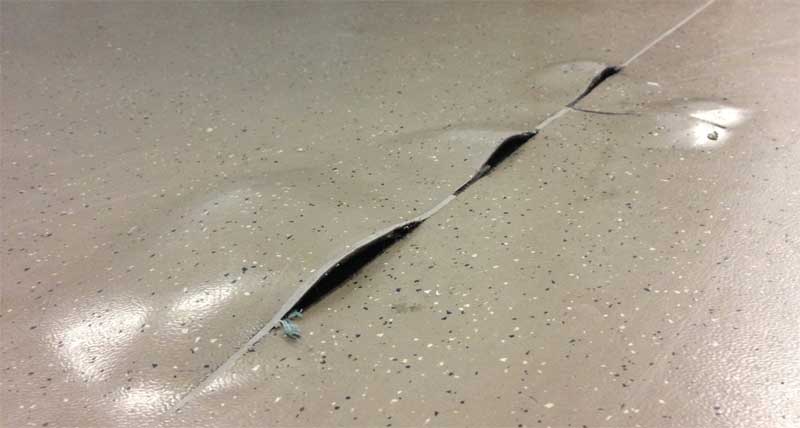
Photo courtesy Chris Maskell, NFCA
Moisture and wait-time
There are four sources of moisture in slab-on-grade thatcan be harmful to water-based adhesives and delay the start of floorcoverings:
- surplus water not hydrated with cement;
- ambient humidity;
- soil moisture and groundwater; and
- rain or construction operations that rewet the slab.
Surplus water
Excessive surplus water can extend the wait-time for concrete to dry by several months. Surplus water is the water that is not hydrated with cement and must evaporate before concrete is safe for moisture-sensitive adhesives. It is the specifier’s loosely written water-cement ratio (w/c) design that is responsible for most excess surplus water. A correct w/c ratio specification would provide enough water to bring about complete hydration of cement, leave enough surplus water to allow for placement, and account for the rapid evaporation of moisture in the first few hours before curing is started. Thus, while a certain amount of surplus water is needed, this surplus must be thoughtfully calculated. The w/c ratio should not be viewed solely as a tool for easing placement—which is a function of water-reducing admixtures (WRAs)—but should be written to minimize surplus mixing water.
Specifiers can have a direct effect on shortening the wait-time by specifying the lowest practical w/c ratio (0.45 w/c or lower) and reducing the cement paste requirement with an optimal selection of aggregates. ( For more on aggregate selection, see this author’s article, “Critical Threshold for Concrete Moisture Content,” published in the December 2017 issue of The Construction Specifier, the official magazine of CSI. Visit www.constructionspecifier.com.) Reducing the cement paste reduces total water in the mixture.
Concrete does not harden by drying, but becomes a solid mass when the water in the mixture hydrates with cement and encloses and adheres to the aggregate. As the concrete hardens, surplus water that has not hydrated with cement or evaporated is encapsulated in the gel system of the concrete, becoming a source of internal humidity—a long-term hazard to moisture-sensitive adhesives and floorcovering.