Concrete flooring: Mitigating vapour-related failures
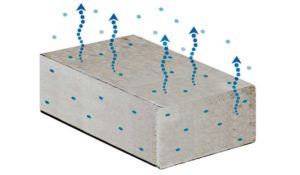
Pre-emptive moisture mitigation
Pre-emptive moisture mitigation has become commonplace in hospital settings because a flooring failure resulting in downtime is far more costly than the price of moisture mitigation as an ‘insurance policy.’ While this practice is extremely effective, it has not been widely adopted across commercial construction because adding $5 to 9 per square foot to the overall budget is frequently not an option. Instead, contractors install the slab, wait as long as possible before testing it, then deal with the problem if testing reveals high vapour emissions or moisture content.
Therefore, moisture mitigation has had to evolve and improve. Owners were shocked to hear fixing their floors would cost more than the original floor finish installation. Floor prep and flooring manufacturers started releasing products which did not require mitigation or testing. While many of these products work, they do not address the underlying moisture, which will remain a concern for every future finish flooring change. When it comes to moisture, it is generally accepted across the industry that it is best to fix the source of the problem, thus floor prep manufacturers began exploring more cost-effective moisture mitigation technologies.
Sodium silicates hit the scene as a solution for moisture emissions about 10 years ago. Sodium silicates are added to the concrete at the batch plant or onsite as the concrete pour is happening. These products have worked in certain settings, but overall have had mediocre success due to potential bond issues. Many flooring manufacturers do not recommend them underneath products. As such, their warranties generally require the presence of someone onsite to make sure their product is installed properly to prevent a moisture or bond failure.
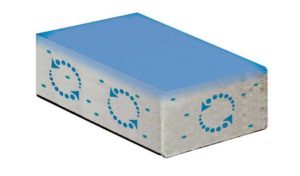
Single-component mitigation technology
Single-component mitigation technology has been an area of advancement driven by excessive cost associated with installing a two-part epoxy moisture mitigation system. While some of these products have proven to perform as well as two-part epoxies, there has been pushback from architects and general contractors who are looking to adhere to ASTM F3010, Standard Practice for Two-Component Resin Based Membrane Forming Moisture Mitigation Systems for Use Under Resilient Floor Coverings. ASTM committees create several different types of documents, such as testing methods or practices for the industry. Standard test methods are procedures that generate test results defined to provide a uniform method for collecting specific data. ASTM F3010 is often perceived as a standard test method; however, it is a standard practice, which is a set of instructions that does not generate a test result.
ASTM F3010 does reference ASTM E96, Standard Test Methods for Water Vapor Transmission of Materials. This standard test method is the key to ensuring a system can block moisture vapour emissions, and it is used across a variety of industries to test a broad range of products, including moisture mitigation systems, tape, food, and pharmaceutical packaging.
The major advantage of a one-component product is its price advantage. A one-component product can be installed for several dollars less per square foot than a two-part epoxy system. Single-component moisture barriers generally only require an open surface to be installed. Instead of an aggressive CSP of three to five, achieved through shotblasting, proper surface preparation can be achieved through the less intensive process of grinding. Single components are installed in two coats. However, the second coat also serves as the primer for the underlayment or flooring, which eliminates the need for an additional primer or sand broadcast. Because a single component is not activated by a chemical reaction, as with a two-part epoxy, the installation process is more forgiving.
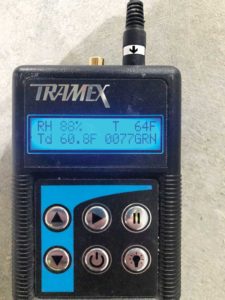
Moving forward
With reliable, cost-effective moisture mitigation solutions now available, some general contractors are realizing the extent of the benefits a moisture mitigation system has on projects—primary of which is the opportunity to reduce the construction timeline. The drying process in concrete starts the day the building is enclosed, and the HVAC starts running. Until this happens, the slab is subject to water intrusion through weather conditions, water from other trades, etc. Once true drying site conditions are achieved, the concrete will dry at a rate of 25.4 mm (1 in.) per month, so a 203.2 mm (8 in.) slab will take eight months to dry in optimal conditions.By this standard, the slab should be fully dry by the time installation starts. By installing a moisture mitigation system over green concrete, contractors are no longer beholden to the moisture content of the slab when scheduling flooring installation.
Developers are buying into these solutions because of the reduction in risk they represent. A cost-effective moisture mitigation system helps to avoid major budget impacts, timeline delays, and the risk of litigation associated with unforeseen moisture problems. It is always easier to take care of a problem on the front end, as construction will not have to be stopped and the floor cleared to address the issue, which can take upwards of a week to resolve. The time impact alone pays for some newer one-component solutions.
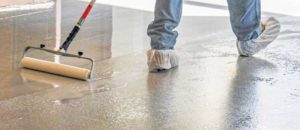
Many products being developed in the floor finishing industry are not moisture sensitive. These are great alternatives, but as the problem is not addressed, the issue will need to be revisited if the floor covering is changed. Mould, mildew, finish and/or joint filler discolouration are also issues. With the introduction of reliable, affordable moisture mitigation solutions, it is possible to rethink the construction schedule and leverage a moisture barrier to reduce timelines and risk. Correcting the source of potential problems from the beginning may prove to be the best insurance policy money can buy.
Author
Heather (Yario) Rice has spent the last 18 years working in some capacity of floor prep and moisture mitigation. She has worked for two major flooring contractors and three large floor prep manufacturers, gaining extensive knowledge of moisture mitigation; Portland, hydraulic, and gypsum cements; as well as sound and fire ratings. Rice is a certified concrete moisture testing technician through the International Concrete Repair Institute (ICRI) and keeps up to date on the latest technologies and advancements.