Concrete Cracking Problems: A modern-day phenomenon?
What factors influence the magnitude
of volume change?
In addition to the effect of water content, autogenous shrinkage is very sensitive to cement composition, content, fineness, and temperature. However, the materials used in modern concrete, such as specialty admixtures and supplementary cementing materials (SCMs), can also have an influence on the magnitude of autogenous shrinkage.
From traditional to modern concrete
Less than a century ago, conventional concrete typically consisted of four basic ingredients—cement, sand, graded coarse aggregate, and water. To meet the demands for improved resistance to the actions of freezing and thawing, the first commercially available chemical admixture products were predominantly air-entraining agents. These were followed by water-reducing admixtures (WRAs), which typically provided moderate reductions in mixing water so workability could improve or cement content could be reduced. A variety of products subsequently become available, typically formulated by the manufacturers to modify setting properties (i.e. retard or accelerate), provide waterproofing properties, and improve cohesiveness for pumping.
However, before the commercial availability of admixtures, another important change had taken place. This change was initiated by the cement manufacturers in response to the increasing demands for more rapid setting and strength development properties of concrete for taller, thinner buildings, structures with wider spans, and faster construction times. This led to changes in the chemical composition and fineness of cement, so the desired hardened concrete properties could be achieved by a refinement of the hydration reactions.
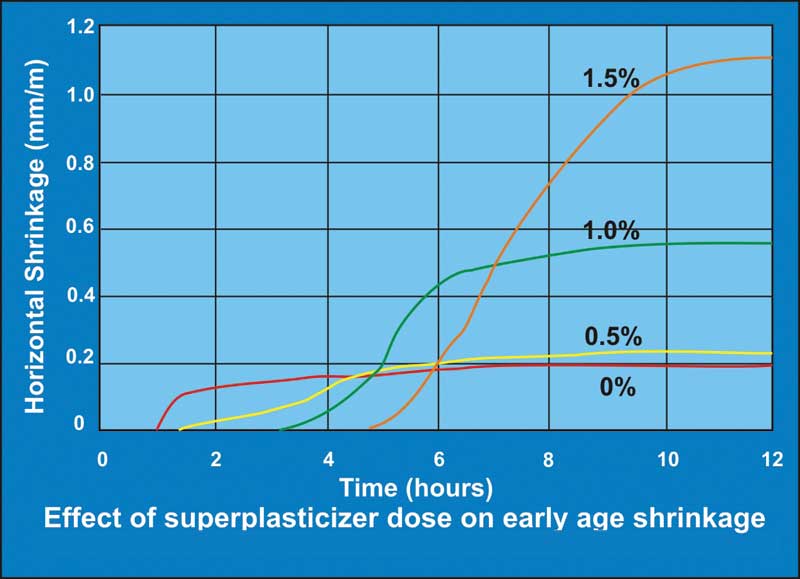
Unfortunately, after these changes were introduced, cracking problems began to occur. It was determined the causes were linked to inadequate strength of the hardened concrete to resist the development of shrinkage, although it is unlikely the influence of self-desiccation and autogenous shrinkage were specifically evaluated during the investigations. Further, this led to changes being made to codes and specifications regarding maximum w/c ratio, minimum cement contents, and minimum compressive strength requirements. One of the main driving forces for the changes was the American Association of State Highway and Transportation Officials (AASHTO), which modified its specifications to require a maximum 0.445 w/c ratio (down from 0.53), a minimum 362 kg/m3 (610 lb/cy) cement content, and a minimum compressive strength of 30 MPa (4500 psi) at 28 days. For 40 years prior to the changes, AASHTO had required a compressive strength of 20 MPa (3000 psi) at 28 days.
The next major event that influenced the magnitude of autogenous volume change was the development and the commercialization of high-performance concrete (HPC), which was originally called high-strength concrete.
High-performance concrete
The evolution that led to today’s concept of HPC began about 45 years ago with the development of superplasticizing admixtures in Germany and Japan. Until that time, high-strength concrete—generally classified as having greater than 40-MPa compressive strength at 28 days—had been produced using high- cement contents, often supplemented with fly ash and traditional water-reducing admixtures. This practice continued well into the late 1970s in North America with compressive strengths limited to about 70 MPa at 28 days—until the introduction of superplasticizing technology.
As superplasticizer’s raw material manufacturing costs were high and the rates of addition considerably more than conventional products, it was not initially perceived that these new admixtures could be commercially feasible for increasing compressive strength, particularly as cement was relatively inexpensive at the time. Thus, they were originally used for producing highly fluid concrete without the need for additional water. However, the oil crisis of the mid-70s led to higher cement costs—while the increased international sales volume through the ’80s contributed to more economical manufacturing costs for the admixtures. Therefore, it became economically feasible to utilize the superior fluidizing properties of superplasticizers to considerably reduce mixing water and thereby significantly increase compressive strength, without compromising placement properties. Unfortunately, much higher dosage rates of superplasticizer were required to achieve the large water reductions to obtain these increases. This also increased the magnitude of early age shrinkage (Figure 2).
The next major advancement in HPC technology occurred during the ’80s, and took advantage of the beneficial properties provided by supplementary cementing materials, such as fly ash, ground granulated blast-furnace slag (GGBS), and silica fume. Although the benefits of fly ash and GGBS were known before this time, it was really the highly reactive properties of the micro-fine particles of silica fume that provided the giant leap forward. Today, it is generally recognized that silica fume can be a prime ingredient in HPC mix design, but there are alternatives and often benefits by substituting all or part of the silica fume content with fly ash or slag. Sometimes, a combination of two or more SCMs is used to gain a synergistic effect. Also, today, the use of the modern materials and technologies means concrete can be routinely produced that develops well in excess of 100-MPa compressive strength.
Unfortunately, studies have confirmed the use of SCMs can intensify self-desiccation and this process begins very early. In particular, the refined cement paste pore structure created by the micro-fine particles of silica fume generates a considerably lower internal relative humidity. Pozzolanic reactions further influence this effect. Silica fume also induces acceleration of hydration reactions of cement at early ages, although experimental data has indicated the resulting self-desiccation can continue for several months.

It is well-known the refined cement paste pore structure produced by the use of silica fume also prevents the natural bleeding that otherwise occurs with conventional concrete. Under rapid drying conditions and without adequate precautions being taken, the result can be the formation of plastic shrinkage cracks. Later, when the effect of volume change caused by self-desiccation occurs, these originally narrow and shallow cracks can widen, deepen, and lengthen (Figure 3). This phenomenon led to the introduction of techniques for use during what is now known as initial curing; these practices attempt to reduce the potential for rapid drying of the immediate concrete surface, prior to the application of conventional curing techniques. (Initial curing techniques typically include the use of evaporation retarders and/or mist-spraying [fog-misting].)
Other factors that can influence shrinkage cracking
A critical aspect of autogenous volume change is—since it occurs within the mass—it can only marginally be influenced by surface-applied water-curing techniques. Liquid-applied curing membranes can have no influence on autogenous self-desiccation. Based on the wealth of available research studies, it is therefore highly unlikely that even the most efficient curing techniques will be able to prevent cracks from forming within concrete susceptible to high levels of internal self-desiccation. If improved durability is a critical requirement, it is therefore important the range of factors that can influence whether a particular concrete could crack are thoroughly evaluated.
Any material or construction parameters that cause a delay of setting will prolong the period when early-age autogenous shrinkage occurs. Delays in setting can be caused by the use of retarders, some superplasticizers, fly ash, and GGBS. Placing concrete during cold weather can also provide delays in setting and the time of hardening. Some researchers have reported increasing levels of GGBS as a partial cement replacement greatly increases autogenous shrinkage at the same w/c ratio.