Concrete’s cobra effect: unintended results of embodied carbon reduction
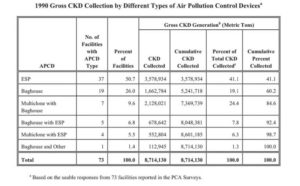
Repairing new concrete
Bad concrete is hard to mistake. Curling, cracking, crazing, deflection, spalling, and concrete’s cancer, alkali silica reaction (ASR)1 are all easy tells to detect poor material. Many of the problems in concrete are the direct result of insufficient curing.2 Change orders in concrete are from poor curing. The wasted hours in responding to requests for information (RFIs) and testing the patience of all project team members come from poor curing. Data centres, school districts, and all manner of facility types spend billions of dollars on superfluous densification mobilizations, multiple patch and repair engagements, and lengthy schedule extensions, never to be recouped because the concrete is not being cured. It is a simple question: how can mechanically grinding millions of square feet of slab back into floor flatness tolerances, and then need to coat that concrete because that grinding has forever compromised integrity and serviceability of the slab be even remotely sustainable? What is the embodied carbon of the millions of square feet of epoxy, urethane, or acrylics placed atop that new, damaged slab?
If newer, low-carbon concrete is to be successful with less crazing, dry-shrinkage, deflection, spalling, and lower permeability, builders must learn the ways in which it is fundamentally different from the concrete of the past.
What is in new concrete?
Calls for reducing concrete’s embodied carbon are a focal point in modern construction. This is no surprise as concrete can represent 50 per cent or more of the overall global warming potential (GWP) of a building’s structure. Additionally, concrete’s carbon impact could be as much as eight per cent of global carbon dioxide (CO2) emissions.
Standard concrete is a composite of water, sand, aggregates, and Portland cement.3 The largest amount of embodied carbon in concrete has historically come from the production of cement. Currently, fuel consumption in kiln-fired production of PC, along with CO2 emission during calcination of carbonaceous rock and use of cement, uses a significant amount of energy and produces large amounts of greenhouse gas (GHG) emissions. In 2010, 2.9 billion tonnes (3.2 billion tons) of CO2 were emitted to the atmosphere from the production of 3.5 billion tonnes (3.9 billion tons) of cement and has climbed since. While cement suppliers have been working diligently on thermal efficiencies of kilns and cooler systems, and even alternative fuels as countermeasures, the easiest solution to meaningfully reduce embodied carbon has been to reduce cement content percentage (i.e. the main culprit of CO2 release). The three most common materials to replace cement have historically been slag, fly ash, and more recently, limestone cement.
The suggestion to replace cement with these materials is not new—as early as the 1960s, the potential of GGBS as a cement replacement material was discovered.4 Earlier than this, fly ash was known to have similar properties,5 even though the reason was not fully understood until more recently.6