Closed-cell spray foam: Flexibility for complex architecture
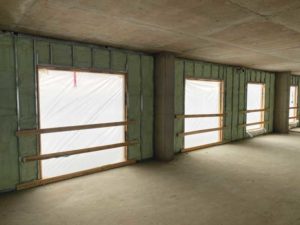
The installation process
One of closed-cell spray foams greatest strengths is the speed and ease of its installation. Some spray foam brands will have a network of elite contractors, ready to expertly deploy spray foam for a variety of projects. The National Building Code of Canada (NBC) and the installation standard for the SPF product, CAN-ULC-S705. 2 (closed-cell) and CAN/ULC S712. 2 (open-cell), mandates polyurethane foam installers to be certified to install the product. Some brands put high emphasis on safety and personal protection, helping installers make it a priority on-site. They also have service representatives and offer the latest training information through training/education programs to assist installers exhibit safe behaviour, which can help achieve a zero-incident job site.
The speed of the installation process means even if weather conditions are unfavourable, the insulation can still be sprayed, left to dry, harden, and be ready for the next step of construction in-between periods of intense weather. Once the foam is installed, it becomes water-resistant and is not at the same risk of damage, say, fibreglass insulation is.
Since spray foam can expand its initial volume in seconds up to 30 times, it is able to quickly fill gaps, small joints, and crevices. If building engineers, architects, or developers have questions, certain spray foam insulation suppliers will have experienced technical teams ready to address questions and concerns. There are also third-party software available to certify applicators. A survey, commissioned by Procore Technologies Inc., a construction management software provider, and conducted in 2021 by international research firm IDC, revealed that within the construction industry, projects are, on average, 70 days late, compared to their original estimate.5 Therefore, choosing a provider who is prepared to go the extra mile is important.
Some suppliers have developed proprietary installation and assembly methods, designed specifically to facilitate spray foam application, regardless of temperature or wind conditions. Spray foam can be installed completely from the interior with innovative techniques, such as cutting the thermal bridge of a wall’s studs by filling the gap between the exterior sheathing panel and the studs. The size of this gap can change depending on the insulation values a project needs to achieve and is created with Z-bars installed directly on the exterior face of the studs before the exterior sheathing panels are installed.
The spacing and size of Z-bars will change depending on the structure and the cladding. This method eliminates potential delays due to weather conditions, as the spray foam insulation is applied completely from the interior. It also reduces rental costs associated with scaffolding, hydraulic elevators, associated logistical work, and accident risks. The walls can be insulated as they are built, speeding up installation and requiring fewer workers overall. Some manufacturers have completed detailing and testing, such as fire compliance and U-value assembly results. The mechanical and electrical (M&E) components can be installed before or after the SPF. If a perforation needs to be made after the SPF installation to run a duct or a wire, it can easily be sealed back with canned foam. This will also save heating costs for construction projects taking place during Canada’s harsh winters.
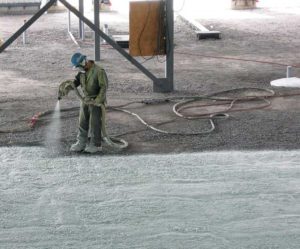
Insulation in any architectural feature
While traditional forms of insulation must be cut to size from pre-fabricated panels, or loosely blown into cavities, spray foam can effectively insulate even the most complicated of structural features (e.g. thin walls, multi-faceted roofing, curved foundations, complex slabs). The previously mentioned case study, Îlot Rosemont, had architectural features such as many slanted and thin exterior walls. Due to spray foam insulation’s high thermal resistance, thinner walls are not an issue, and can save construction costs. Roof framing can be done with thinner framing members, as spray foam provides the same thermal resistance as traditional insulation materials with less thickness.
Irregularly shaped spaces and tight corners can abound when spray foam insulation is specified for projects, so architects can execute on beautiful, creative, boundary-pushing designs which enhance the visual appeal of communities and provide gorgeous interior working and living environments. Beyond beautiful architecture, the completely sealed building envelope creates unparalleled comfort for occupants and contributes to green building standards and sustainability mandates put forward by the federal government.
Conclusion
In an industry plagued by ever-increasing project deadline delays and costs, labour shortages, doing whatever possible to expedite construction and lower expenses is important. Closed-cell spray foam can solve issues facing today’s architects, building engineers, and developers, with speedy installation, simplified specifying, high-quality benefits to building strength and comfort, safety standards, and reduced environmental impact. Closed-cell spray foam does more with less. Altogether, it acts as insulation, an air barrier, a vapour barrier; and is flexible in how it can be applied to structures.
Notes
1 See Îlot Rosemont, huntsmanbuildingsolutions.com/en-CA/tech-library/ilot-rosemont.
2 Read further about the results of the Canadian survey, www.renewcanada.net/5000088747-2/.
3 Learn more Canada’s goal to reach net-zero emissions by 2050 www.canada.ca/en/services/environment/weather/climatechange/climate-plan/net-zero-emissions-2050.html.
4 See this CCMC Canadian code compliance evaluation to learn more about radon protection. www.huntsmanbuildingsolutions.com/en-CA/sites/en_ca/files/2023-02/CCMC%2014280-R_e.pdf
5 For more information, visit at www.idc.com.
Maxime Duzyk is the director of building science and engineering with Huntsman Building Solutions. He holds a background in architecture and has been in the spray foam industry for the last 12 years. Duzyk is involved with different building envelope committees and associations in North America, such as CSC, SFC, SPFA, CCMC, and ULC Standards.