Closed-cell spray foam: Flexibility for complex architecture
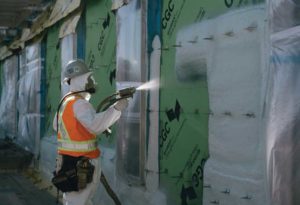
Spray foam insulation: Interior and exterior
Spray foam insulation can be installed on the outboard of the exterior sheathing or in an interior application, such as in the stud cavity. Installation can be performed quickly and at very low temperatures, allowing contractors to effectively insulate projects, sequence their work, and meet deadlines. At 25.4 mm (1 in.), spray polyurethane foam (SPF) insulation can be installed by one person at a rate of 46 m2 (500 sf) per hour. Other products may take more time.
Builders confirm, compared to other insulation systems, they can save up to six weeks of construction time, depending on the assembly. Further, closed-cell spray foam insulation has a comparatively higher RSI-value than other forms of insulation, allowing walls to be thinner and more complex or curved, as the architect may have originally intended.
The total RSI-value always depends on the total thickness installed but some HFO products offer a 1.94 RSI-value for 50 mm (1.9 in.), meanwhile others can offer a 1.49 RSI-value for 50 mm (1.9 in.). The flexibility and resulting versatility of closed-cell spray foam insulation is particularly valuable when it comes to designing, specifying, and building the building envelope, especially when it comes to roofing.
When a roof is being designed, whether it will be a flat roof, cathedral roof, or something less traditional, there are many features and details to be considered. Roofs could contain skylights, recessed lights, plumbing vents, chimneys and, most importantly, air and vapour barrier continuity.
Air and vapour barrier continuity can be understood as building envelope continuity—ensuring the building envelope extends to exterior walls, foundations, below slab, and properly accounts for various roofing styles and design elements. Neglecting proper building envelope continuity for roofing can lead to several issues that will affect performance and durability. Roofs lacking proper insulation or air and barrier continuity can be at risk of moisture retention, which can eventually lead to mould growth; this could damage other aspects of a structure and be costly to rectify. A poorly insulated roof can also lower a building’s energy efficiency, as heating and cooling efforts can be made less effective it is able to leak through the roof with ease.
Closed-cell spray foam insulation can solve all these issues, without placing extra burdens on architects, building engineers, contractors, and developers. It can simplify the specification process as it can provide a continuous building envelope. This means a sole product can serve multiple functions for a project, and an experienced insulation contractor can manage all aspects of a building envelope quickly and efficiently.
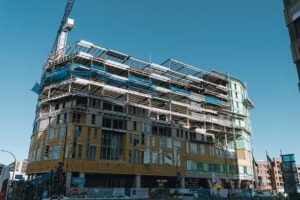
Case study: Îlot Rosemont
Recently, the Office Municipal d’Habitation de Montréal (OMHM) undertook a social housing project: Îlot Rosemont. Îlot Rosemont provides 193 housing units for low-income centres, while, functioning as an administrative centre with nearly 300 employees.1 During its development, the project had fallen behind schedule, and its unique architecture posed further challenges. Some of these features included: two divided wings, a 10-storey wing on the west side, an eight-storey wing on the south side, a V-shaped support column two-storeys high, supporting the building with connecting beams, and many beams on the third level, including five with post-tensioning work. Another feature of this project is the slab on a steel deck over a large area on level two, and a concrete structural slab on level three over the entire surface of the building. The local climate of Quebec also affected the project’s completion schedule, and the thermal resistance also needed to be high. SPF ensured the building envelope requirements were met.
Îlot Rosemont made use of closed-cell spray foam and was able to get back on track quickly, without compromising on the architectural vision, and providing unparalleled comfort for the future residents of the project.