Climate change makes waterproofing vital
External approach
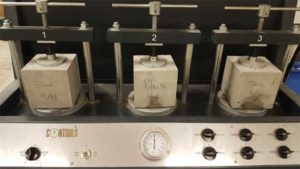
The external approach uses membranes applied to the surface of the concrete. Membranes are divided into two categories—fluid-applied and sheet-applied. Fluid-applied products are typically used as dampproofing, while sheet membranes are required when there is an increased risk from hydrostatic pressure and other environmental properties. The concept of waterproofing is easy—the membrane forms a barrier, thereby preventing water from touching the concrete.
However, there are drawbacks to this method. Traditional waterproofing membranes are usually installed after the concrete is placed. In vertical applications, extra space is required around the perimeter. This can significantly reduce the building’s footprint and limit its design. For example, taking 1 m (3 ft) of space away from the property line can result in a significant loss in building footprint. This loss is amplified as the structure gets higher, and can equate to millions of dollars in lost revenue. The acceptance of structural shotcrete has allowed membranes to be used in blindside applications and gets around this limitation, but puts a significant amount of risk in the installation of the membrane, which is why multiple waterproofing systems are typically used in areas where hydrostatic pressure exists.
Additionally, highly skilled labour is required to apply the membranes in dry weather after the concrete is cured.
Surfaces have to be properly prepared and the application needs to be precise. Fluid-applied systems are dependent on the installer spraying consistently. Although quality control steps, such as measuring mil thickness and manufacturer training programs, can be undertaken, the waterproofing comes down to the capability of a single person installing in perfect conditions. With sheet-applied systems, every seam needs to be installed 100 per cent correctly or the area will leak. The larger the project, the more detail is required and higher the chance of error or damage during installation.
Even if installed perfectly, traditional surface-applied waterproofing is susceptible to damage and tends to deteriorate over time. Early punctures can take place from backfilling or other work during construction. There is no way to inspect the membranes after backfilling has been completed. It is challenging to inspect the membranes after installation and impossible after backfilling. Excavating to repair is also a costly process.
External waterproofing is an installed product, and construction schedules suggest it is time-consuming. It can add days, weeks, or on large complex projects, months to the schedule. While these are not completely hidden costs, there is very little understanding on the true expenses that are associated with installing and repairing membranes over the life of a concrete structure. A general contractor will understand the cost to him for the physical installation, and typically build a conservative schedule to accommodate. However, the costs that are associated with building time into the general construction schedule are usually unknown. If waterproofing was not needed, it would be easier to schedule and fast track construction and better understand the actual cost of waterproofing.
Internal waterproofing
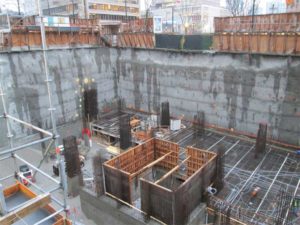
Also known as integral waterproofing, internal waterproofing is the method of adding the waterproofing component to the concrete at batching stage. These include densifiers, hydrophobic admixtures, and crystalline admixtures. However, not all of these components are suitable for waterproofing against water under pressure.
The American Concrete Institute (ACI) classifies admixtures for concrete as permeability reducing admixtures (PRAs) and then groups them as either PRA for non-hydrostatic conditions (PRAN) or PRA for hydrostatic conditions (PRAH). The former is suited for dampproofing and the latter for waterproofing. PRANs are classified as unreactive while PRAHs are reactive.
Crystalline admixtures under the PRAH category are recommended for long-term waterproofing in hydrostatic conditions and intended to replace the need for conventional labour-intensive membrane systems. With crystalline admixtures, the insoluble crystals are produced in the presence of water and reduce the permeability of the interior concrete matrix over time. The crystals grow throughout the concrete resulting in permanent waterproofing impervious to damage and deterioration. The key benefit is the admixture becomes a part of the concrete. This not only removes the need for a membrane, but also eliminates the risks of punctures, installation, and deterioration that can occur in external membranes used for waterproofing.
According to ACI, a PRAH waterproofing admixture must have the ability to lessen water under pressure and reduce concrete’s permeability by 50 to 90 per cent. Concrete permeability and water penetration tests like DIN 1048-5, Testing concrete; testing of hardened concrete (specimens prepared in mould), and EN BS 12390, Testing hardened concrete. Depth of penetration of water under pressure, take crystalline-treated samples and compare them against control samples by applying 0.5 MPa (72.5 psi) of water pressure for three days. Both samples are cracked open and water penetration is measured. The treated sample is then calculated as a reduction in permeability over the control. As mix designs differ, results will too—this is why ACI provides such a broad range.
Another ACI guideline is PRAH must be able to self-seal the micro-cracks that may form in the concrete over its life. Since a crack can become a gateway for water, and small cracks could turn into large ones, self-sealing is a critical property. The more reliable the long-term reaction of the crystalline admixture, the lower the life-cycle costs.