Climate change makes waterproofing vital
by Kris Till
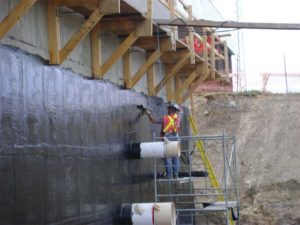
Waterproofing structures has always been an important and often costly consideration for designers and builders. Canada’s weather can be extreme, and climate change poses additional challenges for those involved in protecting the structure from water damage.
Whether one is trying to keep water in or out of the structure or protect the concrete itself from the deteriorating effects of water, the decisions made during construction have major cost implications over the long term. This creates financial stress for building owners, facility mangers, and developers.
Waterproofing structures
Concrete is one of the world’s most widely used materials. It is the choice of many building professionals because of its durability, versatility, unique engineering properties, and availability of constituent materials.
However, as a porous and permeable material, concrete is vulnerable to water penetration. Water passes through pores, voids, and capillaries, especially under hydrostatic conditions. It also cracks, thereby allowing water to pass freely into the structure and flood, or through to the reinforcing steel to start the corrosion process.
The damage water does to concrete used in infrastructure projects and in below-grade foundations is staggering. The Construction Waterproofing Handbook says, “Water continues to damage or completely destroy more buildings and structures than war or natural disasters” (Read the Construction Waterproofing Handbook by Michael T. Kubal).
Through long-term deterioration like freeze-thaw cycles and corrosion of the reinforcing steel, water infiltration can weaken the structural integrity and shorten a structure’s lifespan. Rising sea levels and other long-term effects of climate change, as well as the expectation concrete structures will last longer, make waterproofing concrete more essential than ever. Designs made during construction will affect future spending.
Types of waterproofing
There are two industry approaches for waterproofing: external and internal. Membranes usually last one to 10 years, and manufacturers would warrant the product will be free from defects. However, since the material is installed, it is never warranted against leaks. Having said that, some manufacturers work with installers to offer two- to three-year extended warranties.
Crystalline manufacturers offer 10- to 25-year warranties on their products. Furthermore, some manufactures offer 10-year labour and materials warranty to undertake repairs.