Choosing SPF as an effective air barrier component
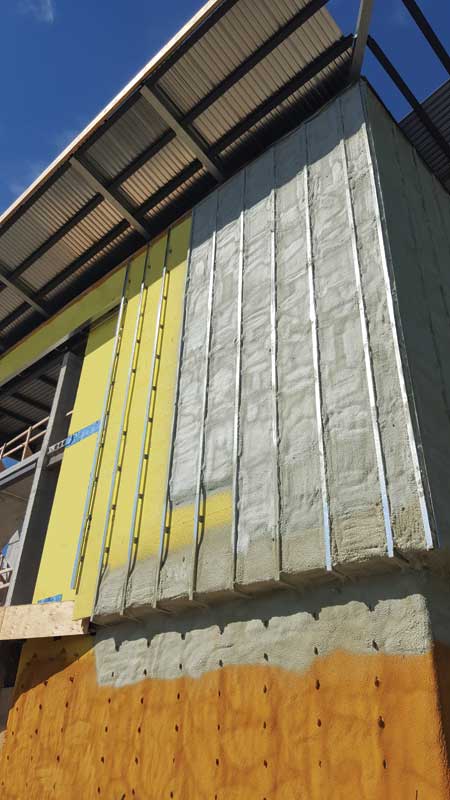
Air barrier system evaluation
Since the late 1990s, CCMC has published its Technical Guide for Air Barrier Systems for Exterior Walls of Low-rise Buildings. The resource describes all physical testing and administrative items necessary to technically evaluate and confirm the effective field delivery of an air barrier system. It is jointly issued to the proponent of the system and the third-party laboratory identified by them. The Technical Guide was among the first such comprehensive documents; it precedes the aforementioned ASTM and CAN/ULC standards.
ASTM E2357, although similar in approach, uses slightly less maximum pressures. (That is, positive and negative 300 Pa [43 lb/sf], as compared to positive and negative 500 Pa [72 lb/sf].) Assembly air leakage criteria that can be found in U.S. building codes and standards, based on testing to ASTM E2357, is often not as stringent as in Canada. Aside from some programs particular to some jurisdictions or building portfolio owners/managers, having an acceptable assembly air leakage rate of no greater than 0.2 L/s.m2 (0.04 cfm/sf @ 1.57 lb/sf) is not uncommon. (This would be a factor of approximately 10 times less airtight than the typical air barrier criteria for any individual material.)
Prior to the CCMC Technical Guide, there were only air leakage requirements for individual materials. These still appear in building codes, with the requirement typically being a sheet or panel should have an airtightness no less than 0.02 L/s.m2 at 75 Pa pressure (0.004 cfm/sf @ 1.57 lb/sf). Based on modelling, the permissible leakage rates for an assembly were established, linking the requirements to the water vapour permeance of the outermost (non-vented) layer of the wall assembly. An interior winter relative humidity (RH) of 35 per cent was assumed. For typical sprayfoam air barrier systems, this maximum permissible air leakage rate would be 0.05 L/s.m2 at 75 Pa pressure, for an outermost layer of low water vapour permeance. (In a wall assembly, such an outermost layer of low water vapour permeance would be greater than 15 and less than or equal to 60 ng/Pa.s.m2.)
For air barrier systems incorporating sprayfoam as the principal plane of airtightness, the proponent must first have a CCMC Evaluation Report or listing for the primary function of the material—that being thermal insulation. Additionally, the factory must be under control by an accredited quality assurance agency or have a registered International Organization for Standardization (ISO) 9000 series Quality Management System.
The CCMC Technical Guide outlines the rigorous testing required. For each substrate, for example, exterior gypsum sheathing, several large assemblies (i.e. 2.4 x 2.4 m [8 x 8 ft]) are constructed and subjected to air leakage testing. These assemblies variously represent:
- an opaque wall;
- a wall with standardized penetrations; and
- an opaque wall/concrete foundation interface.
Other components of the wall system, such as cladding and interior finish, are generally excluded.
An air leakage rating is established for the entire system using the opaque wall without penetrations as the baseline. The other two walls are required to have an air leakage rate no greater than 10 per cent of the baseline wall. The walls are subjected to both positive and negative pressure loading as per a continuous schedule, representing sustained, cyclic, and gust loads. An option of increased wind pressures is possible to qualify the assembly for geographical areas where wind design values may be more demanding.
Durability
Durability in service of all air barrier system components is an important consideration, and evaluated by the CCMC Technical Guide. Robust criteria exist for the durability for the sprayfoam, requiring a specific retention of thermal resistance (i.e. 90 per cent retention) and air leakage characteristics (i.e. less than or equal to 110 per cent of the original value) after weathering
(i.e. irradiation and rain) and heat-aging exposure. The stringency of this evaluation is further enhanced by the fact the baseline condition for these characteristics is after conditioning.
All other types of components also have durability criteria, in terms of individual tests. In most cases, the tests are aggregated within a consensus material standard. No further tests are usually necessary if it can be confirmed the component meets such a standard.