Cement and concrete, still outperforming in the sustainability era
Raw materials
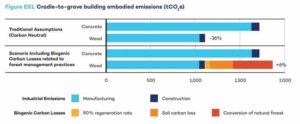
The materials used for concrete construction are locally sourced, and readily available and mined from the earth’s crust, resulting in low-impact resource extraction and transportation. Aggregate, which comprises the largest proportion of material in concrete, requires little processing and is naturally occurring and locally available. Mineral extraction is tightly regulated, and sites can be restored to deliver a biodiversity gain to the surrounding environment.
Durability and resilience
Concrete is durable and able to provide a long service life in a variety of natural climates and environments, resisting weathering action, chemical attack, moisture, and abrasion while maintaining its engineering properties. Additionally, reinforced concrete offers resistance to natural disasters and a changing climate. Concrete is sometimes used in areas where it is exposed to substances that can cause deterioration. In such situations, high-durability mix designs using a low water-to-cementitious materials ratio and a high quantity of Supplementary cementitious materials (SCMs) can be enhanced by application of protective coatings or membranes (refer to the “Effects of Substances on Concrete and Guide to Protective Treatments” by Beatrix Kerkhoff). However, consideration must be given to the Living Building Challenge’s Red List.
Energy efficiency and healthy living environment
Concrete offers advantages to energy performance such as reduced heating and cooling costs through its excellent thermal mass, with a high heat capacity for storage (around 1000 J/kgoK) and moderate thermal conductivity (around 0.5 to 3 W/moK). Additionally, concrete can result in mitigation of the urban heat-island effect, and increased lighting efficiency due to an albedo reflectance of around 0.35 and solar reflective index greater than the threshold value of 29 required for hardscape in most green building standards and rating systems. It also offers improvements in air quality due to negligible levels of volatile organic compounds (VOCs) and elimination of uncontrolled through-wall infiltration, which can be enhanced through the use of photocatalytic cements that remove and decompose contaminants from the air. Concrete also offers effective sound attenuation, with concrete masonry units (CMUs) offering sound transmission classes (STCs) from 40 to over 60 depending on thickness, density, and design.
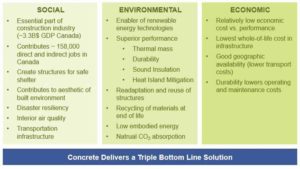
Images courtesy Lehigh Hanson
Adaptability
The use of concrete not only reduces maintenance and operational costs of buildings over their service life, with up to 10 per cent lower annual operating GWP than alternative designs, but also provides the option to repurpose, reuse, or recycle structures and the materials at the end-of-life, decommissioning stage.
Absorption of CO2
Just like trees, concrete naturally absorbs CO2 from the atmosphere. Science shows concrete absorbs the equivalent of up to 25 per cent of the emissions generated in creating it over its lifespan.
Low-carbon innovation
Innovations in the cement sector ranging from lower carbon cements and low-carbon fuels and materials from the waste stream to investment in carbon capture utilization and storage technologies are putting concrete on a path toward carbon neutrality. These effects could even transform the material from a significant emitter of carbon into a carbon sink.
Environmental impact of concrete
The primary environmental concerns regarding concrete are related to its CO2 footprint and the amount of energy required for manufacturing. These impacts are predominantly associated with concrete’s active ingredient, cement. Concrete is formed when cement is mixed with water, which binds the aggregate into a strong, cohesive structure. Cement production is energy- and CO2-intensive, but the product itself accounts for only 10 to 15 per cent of the volume of a concrete mix. The other ingredients in concrete consist of aggregates, taking up 60 to 75 per cent of the volume, and water, which accounts for around 15 per cent of the volume (Figure 4).
Cement is manufactured by heating a mixture of ground limestone and other minerals containing silica, alumina, and iron up to around 1450 C (2642 F) in a rotary kiln. At this temperature, the oxides of these minerals chemically transform into calcium silicate, calcium aluminate, and calcium aluminoferrite crystals. This intermediate product, called clinker, is then cooled and finely ground with gypsum (added for set-time control), limestone, and specialized grinding aids, which improve mill energy consumption and performance to produce cement (Figure 5). Those calcium silicates chemically react with the mixing water in concrete, through a process called hydration, to form an extended network of bonds. These bonds bring the aggregates together and give concrete its characteristic strength and durability.
On average in Canada, 1 tonne of cement can results in approximately 0.78 tonnes of CO2. Approximately 1/3 of this is from the energy and heat requirements for manufacture, and 2/3 is from the calcination of calcium carbonate into calcium oxide and CO2.