Carbon, Environmental Product Declarations, and Brickwork: Reducing footprints through masonry
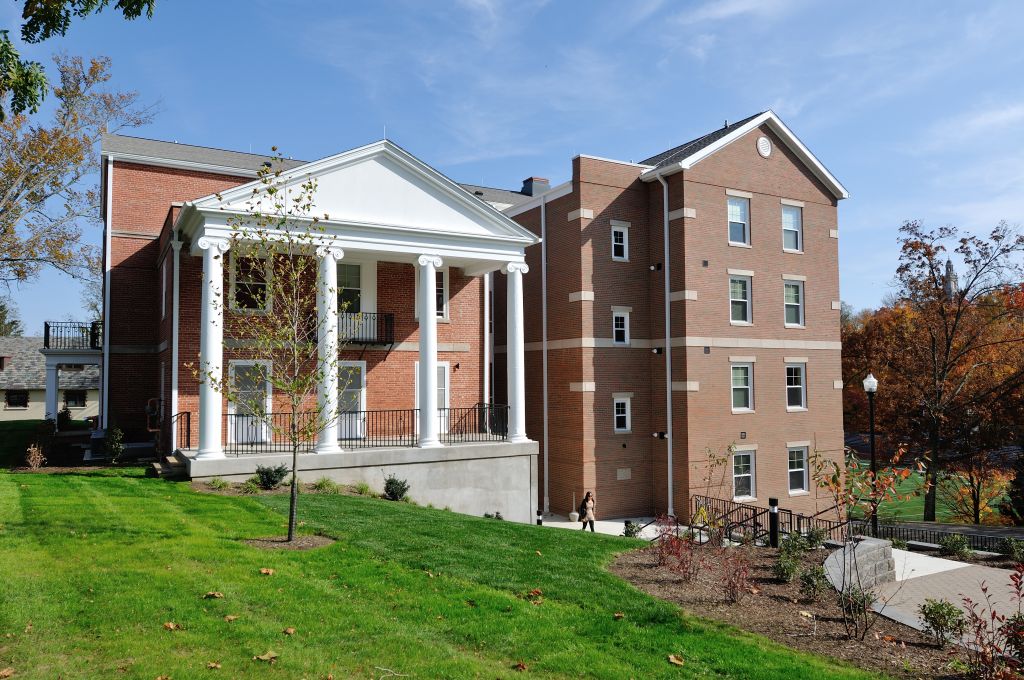
By Maranda Bennett
A primary component of Canada’s built environment, brick masonry is one of the oldest construction materials, and has been in use for millennia. Its durability has helped it stand the test of time, and its esthetics continue to make it a desirable, in-demand option in many locales.
Clay brick is inherently sustainable in some ways. It has a long lifespan and a high thermal mass, and it is often locally extracted and manufactured. However, clay brick is less sustainable when it comes to the amount of energy consumed and greenhouse gases (GHGs) emitted during production.
In recent years, the brick industry has sought new ways to reduce these environmental burdens. A few brick plants have switched to alternative fuel sources for their manufacturing, and some companies incorporate recycled materials into the bricks.
While these efforts are certainly laudable, they do not address some of the most urgent environmental threats: intensive consumption of fossil fuels and associated emission of GHGs (e.g. carbon dioxide [CO2]), which are primary causes of climate change.
Clay brick hardens through firing, typically in tunnel kilns operating continuously at about 1100 C (2000 F) for up to four days. During normal operations, these kilns are rarely shut down, except for maintenance. Kilns are typically fired with natural gas, coal, or petroleum coke—all of which emit significant CO2 in their combustion.
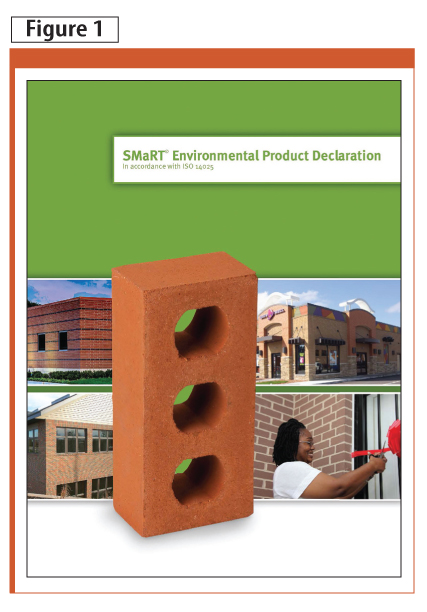
Why carbon matters
To fully measure the environmental footprint of buildings, it is essential to understand the manufacturing processes behind all construction materials. With green buildings, much attention is paid to operational energy and GHG emissions: How efficient is the HVAC system? Are the lights on motion sensors? Is there adequate daylighting? Is energy drawn from renewable sources?
These elements are important, but a strictly operational focus neglects the energy required to produce a structure’s materials—embodied energy—and the carbon associated with their manufacture, transport, and installation, which is collectively known as the ‘carbon footprint.’ It is estimated by groups like Architecture 2030 that the materials’ carbon footprints can account for as much as 20 per cent of a project’s total carbon emissions.
According to the U.S. National Institute of Standards and Technology’s (NIST’s) Building for Environmental and Economic Sustainability (BEES) database, the average cradle-to-gate embodied energy for a conventional fired clay brick is about 6.6 MJ (6250 Btu). ‘Cradle-to-gate’ refers to all processes from raw material extraction through departure from the factory. Each conventionally fired clay brick is responsible for the release of about 0.37 kg (0.81 lb) of carbon dioxide into the atmosphere.
Reducing masonry’s carbon footprint through fly ash
There are innovative products that perform the same as traditional brick, have a similar esthetic, and also reduce environmental burdens. Fly-ash brick is a composite of non-clay materials, a high-percentage of which is ash recycled from coal-fired electric power plants. These units neither use ordinary portland cement (another material with a high carbon footprint) nor a firing process.
When coal is burned, approximately five to 10 per cent of it is turned into ash. Fly ash is a lighter ash product that would ‘fly’ away if not captured in the power plant chimney. Traditionally, it would be disposed of in landfills, but, for many years, it has been used as a partial cement replacement in concrete, creating more durable, higher-performance concrete, and reducing the amount that is landfilled.
In fly-ash brick, fly ash (up to 37 per cent of the brick), water, sand, and some chemistry act together to form a solid unit. No clay or portland cement is used. The resulting units meet the same performance requirements as conventional clay and concrete brick, but with a fraction of the embodied energy and carbon footprint.
Along with the diversion of waste from landfills, using fly ash as a replacement for clay in brick eliminates the need for energy-intensive firing. Rather than firing at 1100 C (2000 F) for several days, fly ash brick is cured below 100 C (212 F) overnight. The result is a manufacturing process requiring just 1.3 MJ of energy per brick instead of 6.6 MJ—an 81 per cent energy savings—and that emits 0.06 kg of CO2 per brick versus 0.37 kg—or 84 per cent less CO2 per brick.
To put these measurements in perspective, it can be helpful to consider what this means in North America. According to the Brick Industry Association (BIA), there are 9 billion bricks produced annually in the United States alone. If those units were replaced with fly-ash bricks, the energy savings would add up to 47.8 million MJ—equivalent energy to power 366,000 homes for a year. The emissions savings would be approximately 1.4 million tonnes of CO2—the same as removing about 546,000 cars from the road for a year.
Additionally, replacing those clay units with fly ash brick would divert more than 6 million tonnes of waste. The brick manufacturing process binds the fly ash, transforming it from an environmental burden into a useful material.
Comparing products using product benchmarking
One difficulty in considering the carbon footprint of building materials is a lack of information and reporting, making it challenging to accurately compare products and understand the true environmental impacts for each product’s various stages of life.
Historically, evaluation of environmental impact relied on supplier claims, with some stakeholders researching specific aspects of a product’s composition and manufacture. Now, product category rules (PCRs), independently conducted lifecycle assessments (LCAs), and third-party-verified environmental product declarations (EPDs) are emerging as key tools for comparing some of the environmental attributes of similar products.
Product benchmarking provides standardized methods for verifying manufacturers’ environmental claims and allows for accurate side-by-side product comparisons from extraction of raw materials to end-of-life disposition. Product benchmarking includes three central concepts that work in concert—LCAs, PCRs, and EPDs. Product category rules are developed first; a lifecycle assessment is performed according to the PCRs; and an environmental product declaration publishes the results of the LCA.
LCAs
A lifecycle assessment is an analysis of every component of a product’s manufacture and use. This includes raw material extraction and transportation to manufacturing site (i.e. extraction phase), manufacturing, transportation to jobsite, and construction (i.e. construction phase), use, and end-of-life phase.
In the case of fly ash and clay brick, the biggest differences in lifecycles come in the extraction and manufacturing phases. Raw materials for clay bricks are mined from a clay pit and then transported, often modest distances, to the clay brick plant. For fly-ash bricks, fly ash is taken from a power plant silo and transported to the brick plant. As extraction energy and transportation distances are different for every brick plant (whether clay or fly ash), a separate LCA should be conducted for each individual plant.
The most significant difference between the environmental impact of clay and fly-ash bricks comes during manufacturing, where the latter eliminates firing and has the subsequent carbon and energy reductions previously described. The manufacturing phase includes all operational energy required to run the manufacturing plant, as well as all upstream energy to create the operational energy. (This is significant because for standard grid-delivered electricity, about two-thirds of the energy is lost during transmission. That is, for every 1 MJ of electricity used at the manufacturing site, about 3 MJ of electricity are made.) For product-specific LCAs and EPDs, this phase specifically accounts for local energy grid sources.
PCRs
A product category rule is the standardized method for conducting and reporting an LCA. The PCR ensures all products in a certain category (e.g. bricks, ready-mix concrete, or roofing products) are measured the same way and environmental impacts are quantified in the same way, in each lifecycle phase.
The PCR defines boundaries for measurement—such as cradle-to-gate or cradle-to-grave—as well as the functional unit measured (e.g. 1 m3 of concrete or 1 square of roofing material). PCRs are developed by industry experts and stakeholders using a consensus-based, collaborative, transparent process. They are then verified by an expert review panel.
EPDs
An environmental product declaration is a document created by the manufacturer to show results of a lifecycle assessment (Figure 1). It is verified by an expert and approved by a program operator, such as Underwriters Laboratories Environment (ULE) or the Institute for Market Transformation to Sustainability (MTS).
It is important to note the boundaries in LCAs and associated EPDs. Simply put, where does the product system start and stop? Does the LCA consider the electricity used to power the plant and also the energy required to create that electricity? (It should.) Does the EPD include cradle-to-grave impacts (raw material extraction through end of life) or only cradle-to-gate (raw material extraction through departure from plant) impacts? For instance, if one manufacturer has published a cradle-to-gate EPD and another has published a cradle-to-grave EPD, the user should look at cradle-to-gate impacts for both products to make a meaningful comparison.
Impact categories
Impact categories describe the effect of a product lifecycle—or individual phases—on specific areas of concern. Impact categories include:
- global warming potential (i.e. carbon footprint);
- acidification;
- eutrophication;
- smog;
- fossil fuel depletion;
- metal depletion; and
- water depletion.
PCRs define which impact categories must be reported in each EPD. Of course, EPDs can always report more impact categories than required by the PCR. Design professionals and owners should consider which impact categories are of greatest interest for their projects. For instance, while carbon footprint is likely always a concern, impact on water resources might also be of specific consideration in particularly arid areas.
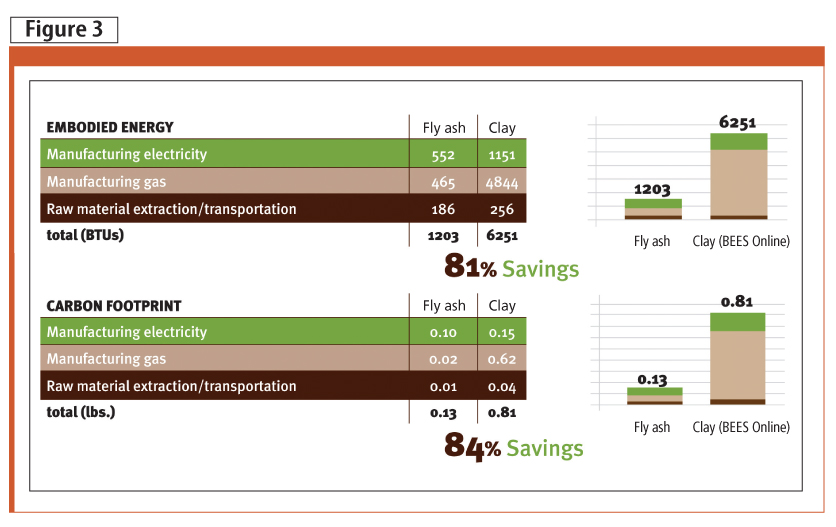
International Organization for Standardization (ISO) 21930, Sustainability in Building Construction: Environmental Declaration of Building Products, has requirements regarding which impact categories must be included in EPDs.1 For example, Figure 2 shows an impact category table from an EPD for fly-ash brick. The items highlighted in purple are categories required by ISO, while the blue categories are additional categories required by the specific PCR used for the LCA for this EPD. As discussed, PCRs ensure EPDs (in the product category) show impacts in the same categories, determined using similar methods.
Before environmental considerations became paramount, design professionals typically chose products based on specific features such as esthetics, technical performance, and price. EPDs provide further information for consideration, allowing specifiers to include carbon footprint or embodied energy in the material selection criteria. Using EPDs, some environmental impacts can be compared directly. Figure 3, for example, shows results of a recently completed EPD of fly-ash brick, comparing the carbon emissions (global warming potential) with clay.
Conclusion
The brick industry continues to seek ways to make its products more sustainable. However, the fundamental process for fired-clay brick—fusion under intense heat—makes a high carbon footprint seem inevitable. Innovative brick makers are attempting to break through this barrier by lowering the heat of firing, if not eliminating it altogether. Non-fired fly-ash brick achieves similar performance as traditional fired-clay brick (in terms of strength, durability, and thermal mass) via chemical reaction instead of heat fusion, resulting in a dramatic reduction in carbon footprint, without compromising performance or price.
The next step in green construction is adding environmental impacts such as these as selection criteria for materials. This requires knowledge of the environmental impacts of products throughout their entire lifecycles. Environmental product declarations and LCAs provide key data beyond traditional considerations, such as strength and esthetics, while providing an opportunity for side-by-side comparisons.
The consideration of a structure’s embodied energy and carbon footprint can play a significant role in reducing a building’s environmental impact before a single tenant takes occupancy. EPDs are only now beginning to gain traction. As design professionals increasingly ask for environmental impact information—and as the demand grows for independent, standardized, verified product information—more EPDs will become available.
Notes
1 ISO 21930 is not recognized as a recognized standard in Canada by the Standards Council of Canada (SCC), and is therefore not a mandatory requirement. However, this should not discourage use of the standard as a reference; given no other reasonable measurement standard, it provides the best measurement of performance. (back to top)
Maranda Bennett is the Canadian market development manager for CalStar Products. She educates and builds relationships with architects, developers/owners, and brick distributors throughout Québec and Ontario. Bennett has more than 15 years of experience in residential and architectural sales in the brick industry. She is a Certified Green Brick Specialist through the Brick Industry Association (BIA). Bennett can be reached at mbennett@calstarproducts.com.