Calgary’s Bow: An iconic skyscraper revisited
Tower construction
The construction logistics developed by the fabricator and erector required the general office area with the service core and outside finger cores to be built before the atrium screen wall. This base construction could be used to establish the column and diagonal grid node locations to facilitate erecting the atrium screen’s long diagonal members.
It was determined early on that the project required three tower cranes to provide full coverage to the vast site, offer sufficient crane capacity for the mega-nodes and atrium framing (up to 65-tonne lifts), and support an aggressive construction schedule. All three cranes were internal climbers supported by temporary vertical braced cores to provide lateral support.
Unlike conventional structures with a reinforced concrete or structural steel core, the diagrid perimeter system did not have the advantage of a central erection base to which the perimeter framing could be anchored and adjusted. It was also anticipated the erection of the atrium screen wall would take longer than that of the office portion due to the 10.2-m (33.5-ft) offset of the atrium wall from the office space’s edge slab.
In design studies, a strong core scheme was found to trigger a dead load drift of the tower as a result of the side-core location. This saved steel tonnage.
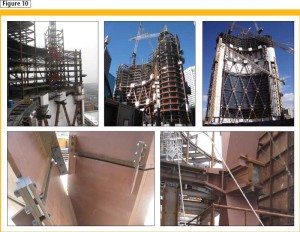
Photos courtesy Walters and Yolles, A CH2M HILL Company
To achieve the erection of the atrium screen wall at a later date, temporary frames were constructed to span the atrium plenum at various levels as a means of stabilizing the entire wall. These temporary frames were removed and reused as the atrium wall construction progressed up the building. Generally, the atrium wall erection was approximately six storeys behind the office area construction. This delay also helped avoid some of the gravity load creep from the office areas, which would happen with a structure of this nature (Figure 10).
Construction tolerances and atrium AESS
Foster + Partners had established a plan tolerance for all slab edges and the atrium diagrid of ±25 mm (1 in.) of the theoretical position over the tower’s full height. This criterion is to a large extent more stringent than the traditional +50/–75-mm (+2/–3-in.) tolerance specified by the American Institute of Steel Construction (AISC) for high-rises, and thus required highly accurate shop fabrications and special measures in the field.
To ensure the atrium was constructed to this tolerance, each AESS member between it and the tower was custom-trimmed before erection, and the atrium’s entire height was ultimately installed within 15 mm (0.6 in.) of the theoretical plan location.
As a Class A office tower, the finished floors also needed to meet very stringent floor flatness criteria. Due to the more heavily loaded interior, columns would ‘shorten’ to a greater degree than the perimeter framing; therefore, the interior columns were super-elevated by approximately 2 mm (0.08 in.) per floor. Adjustments to column elevations were made by adding shims to the bolted or welded column splices locations.
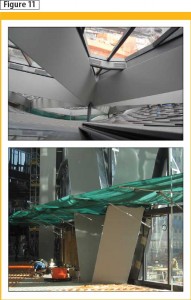
Images courtesy Walters
The architect required a very high standard of fit and finish for the fully exposed atrium diagrid framing structure (Figure 11). This was achieved by developing a system of jigs and fixtures at the fabricator’s manufacturing plants to ensure seamless joints where the members joined in the field.
Modular washrooms
Another unique aspect of this project was the provision of more than 100 fully pre-fabricated modular washrooms (Figure 12).
Steel frames were custom-designed by Feature-Walters (a member of the Walters Group) and fit-out with all interior finishes, vanities, ceilings, lighting, electrical, and mechanical services, granite flooring, and back-painted glass. These modules were then shipped from the manufacturing facility in Ontario to the construction site and hoisted by the crane to the appropriate floor level and moved into position.
This cost-effective solution ensured the highest standards of fit and finish, but more importantly moved a significant body of work off-location to help ease jobsite congestion and accelerate construction progress.
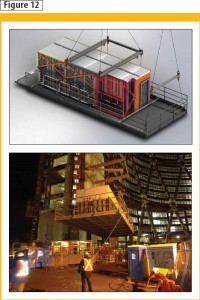
Building the Bow: The Project Team
At the early stages of the project, the client acquired the land for the development, selected the architect and consulting team, and developed the concept to the schematic drawing phase. Following a developer/owner proposal call, H&R REIT were successful in negotiating the purchase of the property and the project, with the client signing a long-term lease for its space. The conceptual development of the project started in late 2005, with the assignment of Foster + Partners of London as the signature design architect and Zeidler Partnership Architects of Toronto and Calgary as the executive architects. Other project team members include:
- Yolles, A CH2M HILL Company
- Ledcor Construction Ltd., construction manager;
- Matthews Developments Alberta, development manager; and
- SWJV (equal joint venture between Supreme Group [Edmonton] and Walters Group [Hamilton]), structural steel fabricators and erectors, and temporary works and construction engineering.
Conclusion
As of October 2012, the construction of the main building structure and the envelope is complete, along with the interior fit-out work, completion of the landscaping areas, and pedestrian path link bridges. The building has been signed off for occupancy to the 40th floor.
From the design team perspective, this unique building proves to satisfy the vision and objectives the client had when it entered into this venture. The unique design aspects of the project on the structural side include the unique crescent-shaped floor plate, sophisticated hybrid lateral system, exposed atrium screen, and numerous construction logistics aspects.
Neb Erakovic, M.A.Sc., P.Eng., is a principal in Yolles, A CH2M HILL Company’s Toronto office. He has successfully performed technical design and management roles on some of the firm’s largest and most notable buildings in Canada, the United States, and overseas. Erakovic’s work focuses on complex structures and collaboration with signature architects. Erakovic can be contacted via e-mail at neb.erakovic@ch2m.com.
Walter Koppelaar is president of Hamilton’s Walters Inc., and directed the company’s transition from a regional steel fabricator to a vertically integrated steel contractor of architecture, infrastructure, and heavy industry projects throughout North America. He established the groundwork for the committee that completed the development of the Canadian Institute for Steel Construction (CISC) standard for architecturally exposed structural steel (AESS). Koppelaar currently serves as a board member of the Ontario Erectors Association, and has served as the past-president of the Hamilton Halton Construction Association. He can be reached at walterk@waltersinc.com.