Building up with lightweight wood frames
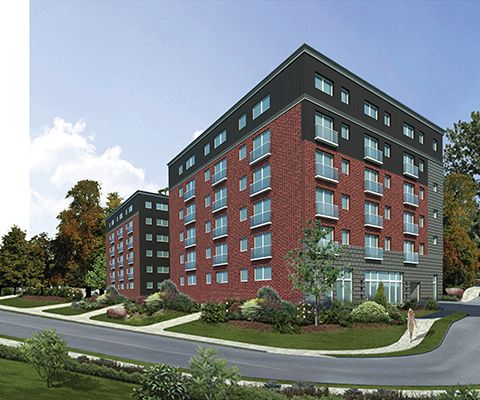
By Michael Baldinelli, P. Eng., MESc.
Lightweight wood-framed (LWWF) construction has gained significant popularity over the past decade as a sustainable, cost-effective solution for low-rise multi-level buildings in Canada. More recently, the push has been to extend use of LWWF to mid-rise construction for increased density on urban or rural projects. In 2009, British Columbia amended its building code to allow five- and six-storey residential wood-framed buildings; in September 2014, legislation was passed so the next Ontario Building Code (OBC) amendment (effective January 1, 2015) would permit wood-framed buildings up to six storeys.
Up until now, very little research has been focused on the three-dimensional behaviour of these structures under lateral loads. Additionally, the current structural analysis and design of these LWWF buildings is performed on an element-by-element basis, neglecting the overall behaviour of the building’s structural system. The result of this lack of information led to the development of a three-dimensional structural analysis program for LWWF
created by Strik Baldinelli Moniz Civil and Structural Engineers. The program:
- calculates all wind and seismic loading on the building;
- takes into account both rigid and flexible
floor diaphragms; - calculates the overall building deflection and inter-storey drift at any point in the building;
- accounts for the stiffness of other building materials (e.g. concrete masonry units [CMUs], cast-in-place concrete, and steel cross-braced framing);
- calculates building natural frequency (NF), overcapacity ratio (OCR), and torsional sensitivity;
- takes into account the cumulative effect of hold-down anchor slippage and nail slippage in deflection calculations;
- meets Canadian Standards Association (CSA) O86-14, Canadian Wood Design Manual, and the 2012 OBC code requirements; and
- optimizes shear wall selection based on material and labour costs.
One-dimensional design approach to multi-level LWWF buildings
In the past, the structural design of smaller (i.e. four storeys or fewer) LWWF buildings demanded a less robust design approach. Internal spreadsheets in conjunction with the Canadian Wood Design Manual and the OBC were used to assist in the design.
A one-dimensional approach was taken with each shear wall isolated and reviewed, without incorporating the interaction of other shear walls in the design. The shear loads were distributed assuming a flexible diaphragm distribution. Once they were assigned to each wall, strength and deflection checks were completed. While the one-dimensional approach may have been satisfactory in the past for smaller LWWF buildings, it is no longer valid with the advent of taller, larger buildings.

The need for a three-dimensional, robust, accurate and all-encompassing design program is required for the design of six-storey wood buildings under wind and seismic events. When the developing firm evaluated the marketplace for such a program, limited options were available.
The approach: fixing the problem
In developing a plan to fix the problem, the first step was to model a LWWF building in existing finite element (FE) programs—the same program used to model concrete and steel structures. Researchers found the FE program could not properly model nail slippage and hold-down elongation. Additionally, the interaction between the floor diaphragm and wall elements was not always accurate. The interaction of nail slippage and hold down elongation account for 25 to 35 per cent of the total building deflection, and thus must be properly modeled.
The researcher’s next objective was to conduct a detailed literature review. The group poured over approximately 60 papers/articles to gather as much information on the topic as possible. A majority of the papers complied were from Europe and the United States where these types of buildings have been approved and constructed for more than 20 years. The group found little research had been conducted on the three-dimensional lateral design of six-storey LWWF buildings. While there were excellent articles on localized one-dimensional analysis of wood shear walls, there was no research on the design process, from beginning to end. Additionally, limited software existed to assist in developing a three-dimensional approach to these types of buildings.

Image courtesy National Research Council Canada
Once the literature review was completed, highlights of each paper/article were compiled for possible use in the design of the program. A detailed flow chart (a simplified version is shown in Figure 1) was developed by the group. It was instrumental in designing the working parts from beginning to end, and it allowed several different components to be designed individually which were then checked, debugged, and incorporated into the main design software.
The program
How the program concludes structural design for lightweight wood-framed buildings can be broken down into five steps.
Step one: Shear wall layout
First, the user must define a shear wall layout. A wood shear wall is a wall composed of wood studs, wood sheathing, nails, and tension/compression devices. The layout has x, y, and z components to provide a three-dimensional design approach to the problem. The first layout of shear walls may change depending on the building’s performance (e.g. added or subtracted shear walls). This initial layout is used as a starting point based on the firm’s LWWF experience and is ‘tweaked’ once the program has completed its design (Figure 2).
Step two: Calculate building loads
The program calculates the seismic and wind loads on the building using OBC requirements. In regards to the seismic loads, one of the main benefits of wood-framed buildings is their reduced mass (i.e. dead load). Wood buildings, generally, have a dead load—three to four times less than other conventional building materials. The seismic shear loads are directly proportional to the mass of the building, thus inducing much smaller loads on the building. Additionally, the ductility factor (RdRo) for wood-framed buildings is more than two times larger when compared to concrete or steel. This increased ductility reduces the shear loads even further, making a strong case for LWWT mid-rise construction.