Building to last with BURs
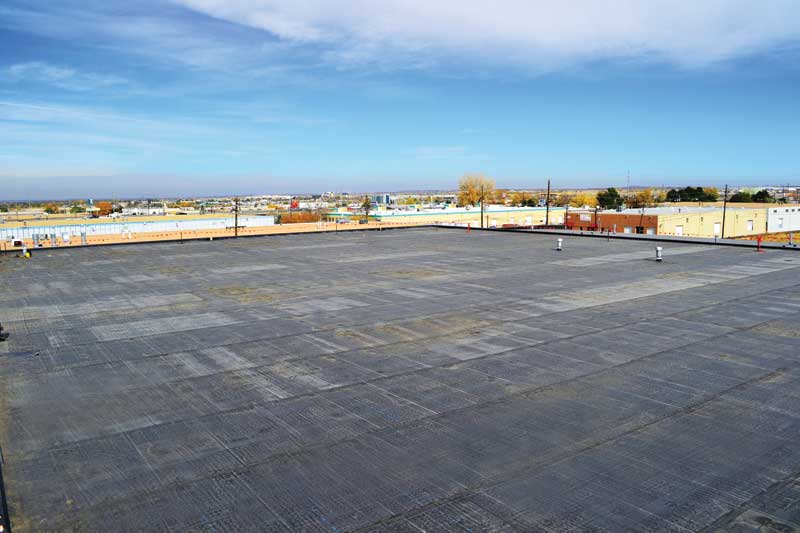
BUR repair and maintenance
To some extent, the life expectancy of a BUR system depends on the property owner’s commitment to routine maintenance. All roof systems can benefit from an owner willing to undertake a proactive management plan. BUR installed over an insulation package lends itself well to non-destructive testing (e.g. infrared) as a means to maximize service life.
“Asphalt roofing systems have the potential for a very long life, and preventive maintenance is the key to realizing that potential,” says Hitchcock.
The goal is for problem areas to be detected and fixed before they develop into leaks. Inspections can reveal potentially troublesome situations, such as a loss of gravel surfacing, which could lead to felt erosion or brittleness. Less commonly, punctures and cuts to the membrane can occur, so it is wise to remove sharp objects and debris from the roof. Clogged drains or poorly sealed flashings also present problems that are repaired easily. The effects of chemical exhausts on roofing materials should also be monitored.
On the positive side, BUR has a long history of proven performance in Canada, where snow and ice buildup are common. Perhaps more than any other roof membrane, the system shrugs off minor abuse. When facilities managers feel the need to shovel snow off the rooftop (though this method is rarely recommended), BUR’s puncture resistance rises to the forefront.
Nevertheless, preventive maintenance actions can help catch problems before they damage larger areas of the roof system. Inspections should be performed not only on aging roofs, but also on new roofs to guard against errors in installation, design, or specifications.
BUR has proven to be a low-maintenance roofing system, and can also be effectively repaired when needed. This means property owners can usually get more life out of a BUR. The ability to enhance the performance of existing BUR membranes with coatings, mod-bit cap sheets, or flood coats of asphalt explain the long service lives of these systems in demanding applications. These BUR maintenance and repair solutions are typically more involved than peel-and-stick patching on some single-ply systems. However, like BUR, these repair options have proven to work well over time.
Non-gravel BUR surfacing options include aggregate, mineral surface cap sheet, or a smooth, surface-coated membrane. After many years of exposure to the elements, these surfacing materials may need some attention due to possible aging and weathering of the BUR surface. The loss of protective surfacing or coating from weathering may give the BUR a cracked appearance known as ‘alligatoring.’ This form of BUR aging is much less common in Canada than in warmer climates.
Any moderate alligator cracking can be treated by cleaning the surface of the roof, applying a primer, and resurfacing with an asphalt emulsion. Bare spots resulting from wind scour or water erosion require the removal of dirt and loose aggregate. These areas can then be primed and recoated before new aggregate is re-imbedded into the surface.
Splits or tears in aging BURs can also be readily treated. Any poorly attached elements of the BUR can be re-secured with fasteners into the deck. The fasteners and splits can then be stripped in with a mod-bit membrane. Ridging on aging BUR membranes can form due to internal moisture collecting at the insulation joints, insulation movement, or curling. When the top of these ridges lose their surfacing, they can be cleaned and recoated with a roof coating or mastic and aggregate to prevent further roof deterioration. Crazing, punctures, building movement, damage to base flashings, and membrane curling will expose a BUR to increased weathering. However, these issues can be addressed through proper maintenance.
Before the advent of modified bitumen flashings, metal-edge gravel stops and edging for BUR generally consisted of a double layer of felt stripped in after the finish coat of bitumen and surfacing or cap sheet was applied. After years of thermal or wind-induced stresses, splits can form at the joint between the metal edging and the stripping felts. Today, these areas can be repaired with mod-bit flashing material to add strength and flexibility to the edge metal detail.
Missing or badly deteriorated metal cap flashings can also be replaced. Loose metal sections can be refastened and then resealed at the reglet or top of the counter-flashing with a construction-grade sealant. Generally, this is only an option for reglet- or surface-mounted flashings. All too often, using this sealant repair option on through-wall flashings makes a bad problem worse.
Expansion joint problems are generally associated with failures at the joint connection and deterioration of rubber bellows due to weathering. Deteriorated bellows should be replaced, while loose metal cap expansion joints can be re-secured, along with the use of an elastomeric sealant at joints for added flexibility. On older BUR designs using pitch pockets, the fill material has a tendency to shrink over time. In this case, an elastomeric sealant (not bitumen or roof cement) can restore pitch pocket seals and slope.
“Property owners rarely have to replace a four-ply BUR until it is absolutely, positively worn out,” says one roofing contractor who asked to remain anonymous. “Based on experience, these asphalt-based systems ‘hang in there’ longer than less-robust roof options.”