Building successful indoor cannabis cultivation facilities
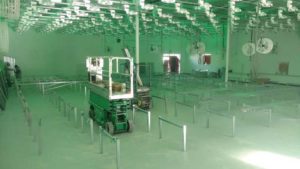
Photo courtesy MJardin
Floor plan considerations
Although operational activities are influenced by the individual cultivator’s processes and procedures, many unifying design elements apply to all indoor cannabis cultivation facilities.
Cannabis cultivation facilities typically contain the following areas:
- a security office;
- areas for decontamination (also referred to as “gown-in” areas);
- several different cultivation rooms; and
- a vault or secure storage area(s).
The location of these rooms with respect to one another helps mitigate the issue of microbial contamination and minimize labour costs in the facility.
Security office
Health Canada has implemented several security measures to ensure all cannabis facilities—cultivation, processing, or retail—are secure from an external as well as internal perspective.
Two key items outlined in the security measures within ACMPR are visual monitoring and intrusion detection services. These measures are in place to enable a company to monitor all activity around a facility and be able to provide a report to Health Canada—upon request, at any time—detailing all persons who have entered and activities that have occurred at the facility. This protects the staff and product as well as the consumer.
The security office should be located near the entrance to the building so staff can monitor visitor sign-in and escort guests accordingly. It is outlined as a compliance practice by ACMPR that the security office has onsite security footage storage and every room in the building is visually monitored. Having cameras all over the facility creates a lot of wiring, so more than one information technology (IT) or security room might be necessary depending on the size of the facility.
Gown-in/decontamination areas
These areas are typically located toward the entrance to the facility to allow all visitors and employees to put on personal protective equipment (PPE) and clean outer garments, and decontaminate or replace footwear before entering the sensitive cultivation and processing areas. This minimizes the introduction of pests, diseases, and microbial contaminants into the facility. They typically include a washroom area, space to change and store street clothes, and an air-lock separating the decontamination area from the sensitive areas of the facility, such as cultivation rooms, processing rooms, and finished product storage areas.
Lockers should be sealed to the wall, and tops should be sloped to avoid the accumulation of dust and debris. These areas need to be frequently cleaned to avoid becoming reservoirs of contamination for the facility.
Floors, ceiling panels, and walls should be:
- non-porous;
- chemically resistant to degradation from disinfectant chemicals;
- non-absorbent;
- free of cracks and crevices;
- sealed;
- durable; and
- cleanable.
Fibre-reinforced plastic, polyvinylchloride (PVC), stainless steel, polyurethane, and epoxy are a few examples of materials and coatings that would work to achieve the above objectives.
Decontamination areas in cannabis cultivation facilities are similar to laboratories and food processing plants in terms of HVAC design, material selection, and process flow. However, there are many conditions within the facility promoting the growth of micro-organisms. For example, cannabis plants are rooted into a potting media containing ample water and organic matter, giving micro-organisms all the things they need to thrive and grow. This creates a risk of possible cross-contamination, as flowers can have incidental contact with the pots during harvest (Consult the May 2005 paper “Sanitary Design and Construction of Food Processing Facilities” by R. H. Schmidt and D. J. Erickson.).
Air sanitation systems (e.g. filtration and ultraviolet germicidal [UV-C] sterilization) can be installed and used to control the quantity of unwanted spores in the air, which tend to be at higher levels than normally found in laboratories and food processing plants. Spore sizes of common fungal contaminants (e.g. Aspergillus and Penecillium) typically range from two to three microns.
Another design element that can aid in controlling micro-organisms in the facility is a water sanitation system. Even in systems that do not reuse irrigation water, biofilms and unwanted organisms can develop in the irrigation lines, which can result in microbial contamination in the crop as well as cause maintenance issues for irrigation systems. Ozone, calcium hypochlorite [Ca(ClO)2], and peroxide injections are common water sanitation methods for indoor cannabis cultivation facilities. These chemicals also reduce the growth of micro-organisms and algae on the surface of the media, as well as the runoff sitting on the benches.
Cultivation rooms
Cultivation rooms are a series of controlled environments containing plants, horticultural lighting, benching, and irrigation/drainage systems. The idea is to minimize the distance a plant travels through the facility to make things more efficient, and keep the cultivation areas grouped together to segregate them from the processing area and minimize cross-contamination. In all cases, maximizing use of available space is essential to designing a profitable facility.

Image courtesy GrowForce Holdings Inc.
The plant flows through the cultivation rooms in the following order:
- mother (stock);
- propagation;
- vegetative; and
- flowering (Figure 1).
Mother (stock) rooms provide the cuttings that grow in the propagation room. Rooted cuttings are then placed in the vegetative rooms to allow the plants to grow bigger, before being moved into the flowering rooms. Therefore, mother (stock) rooms should be near propagation rooms, propagation rooms near vegetative rooms, and vegetative rooms near flowering rooms. The receiving and storage area should be located close to the cultivation area for supplies since they are often bulky and can be quite tedious to move long distances.
Selection of horticultural lighting for cannabis facilities is driven by three main factors: fixture efficacy (micromoles of light per joule or watt), cost, and spectrum. In geographical locations where energy costs are high, selecting fixtures with higher efficacy values is desirable. Current light-emitting diode (LED) technology can reduce costs associated with plant illumination by 20 to 40 per cent, depending on fixture selection, increasing the return on investment (ROI). In areas where cost of power is low, double-ended high pressure sodium (HPS) lighting is typically utilized in flowering areas. LEDs have higher fixture costs but they increase ROI beyond the fixture life.
In vegetative areas, LED lighting makes sense at lower cost per kWh, compared to flowering areas, given the longer lamp operation time (18-24 hours of light for vegetative rooms versus 12 hours of light in flowering rooms). Ceramic metal halide is another option for vegetative plant illumination.
It has a spectrum suitable for vegetative growth, and has a lower capital investment cost. However, operating ceramic metal halide lamps is more expensive.
Plants are grown on benches that come in set widths. One less bench in a space can mean hundreds of thousands of dollars of lost revenue a year. The horticultural lighting is also designed to fit the bench area. The more regular the shape of the rooms (squares or rectangles), the better, because this allows for the best possible space capture for cultivation and a more uniform light set-up. Since the cultivator is looking to maximize benching in these rooms, it is desirable to work with an architect who has a nuanced understanding of building codes regarding door requirements, exiting distances, and aisle widths.
The combination of benches, plants, and mounting height of horticultural lights above the plant canopy means the ceilings in these rooms need to be between 4 and 4.5 m (12 and 15 ft) from the ground, and meet the same requirements as the gown-in area. While acoustic considerations are not an issue in cannabis cultivation facilities, air circulation is of the utmost importance. With ceilings of this height, benches and plant canopies can create vertical barriers causing temperature stratification and microclimates. Usually horizontal or vertical airflow fans are used in these rooms to break up the microclimates around the leaves and promote transpiration and growth, but often they do not solve the problem entirely.
The mechanical equipment for the facility must be sized to meet dehumidification needs, since the plants transpire the majority of the irrigation water entering these rooms into the air. Additionally, cultivation rooms require exhaust capabilities to counteract the CO2 enrichment and pesticide sprays.
Cultivation rooms are exposed to a lot of water from irrigation, transpiration from plants, and cleaning, and they cannot harbour microbial growth. The floors, walls, and ceiling finishes should follow the same requirements as the gown-in/decontamination area. These rooms will likely flood multiple times, so the joint between the wall and the floor should be waterproofed. To do this, the authors suggest wrapping the floor coating (epoxy or polyurethane) up the wall 102 to 152 mm (4 to 6 in.) to create a continuous seal across the joint. Floor drains, or trench drains with floors sloped towards them, are a must.
Thermal breaks for insulation on exterior walls are also important, especially in seasonal climates, as the large difference between indoor and outdoor temperatures can cause condensation to form on the wall, which can result in a variety of microbial contamination issues.
There are no windows in cultivation rooms for two reasons: the movement of the sun and moon would interrupt the plants’ light cycle (which is carefully controlled using artificial lighting for optimum growth) and windows also pose an unnecessary security risk.
Integrated automation systems are becoming standard in cultivation rooms. Features like automated irrigation, variable speed controls on fans, and automated horticulture lighting are often controlled by one system for ease of use. Space to place the control panels should be considered when sizing the cultivation rooms and corridors feeding these rooms. While these features make life easier for the cultivator, they certainly add more complexity to an already complex cultivation room design.