Building more durable balconies
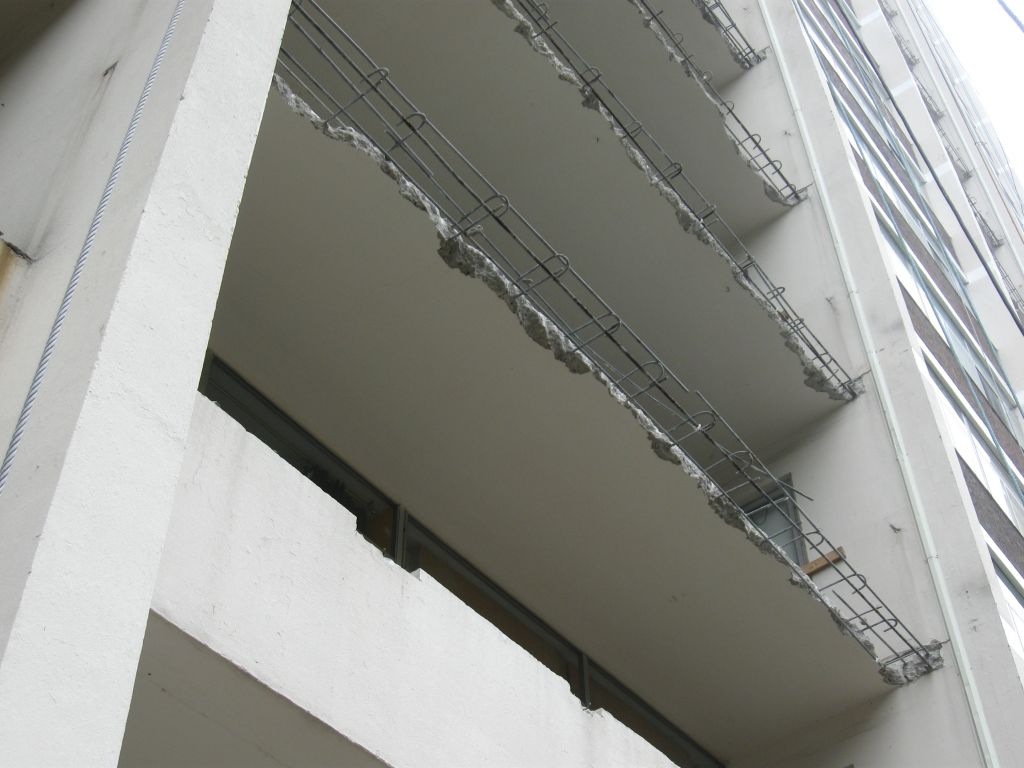
By Gavin Lobo, P.Eng., Sally Thompson, P.Eng., and John Kosednar, P.Eng.
Balcony slab repairs are perhaps the most disruptive project that can take place in a multi-residential building or hotel. Vibrations from the jackhammers that must be used to remove concrete can travel through the entire building, making it unbearable for residents who are home during the process.
For hotels with balconies, repairs can also lead to significant loss of revenue. While the hotel rooms themselves become unusable during the day, the noise from the repairs also affects meeting rooms, restaurants, and other income-generating facilities.
Deferring repairs is rarely an option due to the risk of falling concrete. However, what if design/construction professionals could prevent—or at least, minimize—balcony deterioration in the first place?
Carbonation: The most common cause of balcony slab edge failure
Most Canadian high-rise buildings are built using conventionally reinforced cast-in-place concrete construction. Fresh concrete is highly alkaline, which makes the embedded reinforcing steel immune to corrosion because a ‘passive’ layer is formed on the steel’s surface. In effect, it acts as a protective layer against corrosion.
The chief culprit contributing to the deterioration of reinforced concrete balconies is ‘carbonation.’ This natural process, which involves interaction between the concrete and carbon dioxide in the air, reduces the concrete’s alkalinity. The process advances over time from the exposed surface inward. When this ‘carbonation front’ reaches the depth of the embedded reinforcing steel, the passive layer is destroyed, and the steel is now susceptible to corrosion.
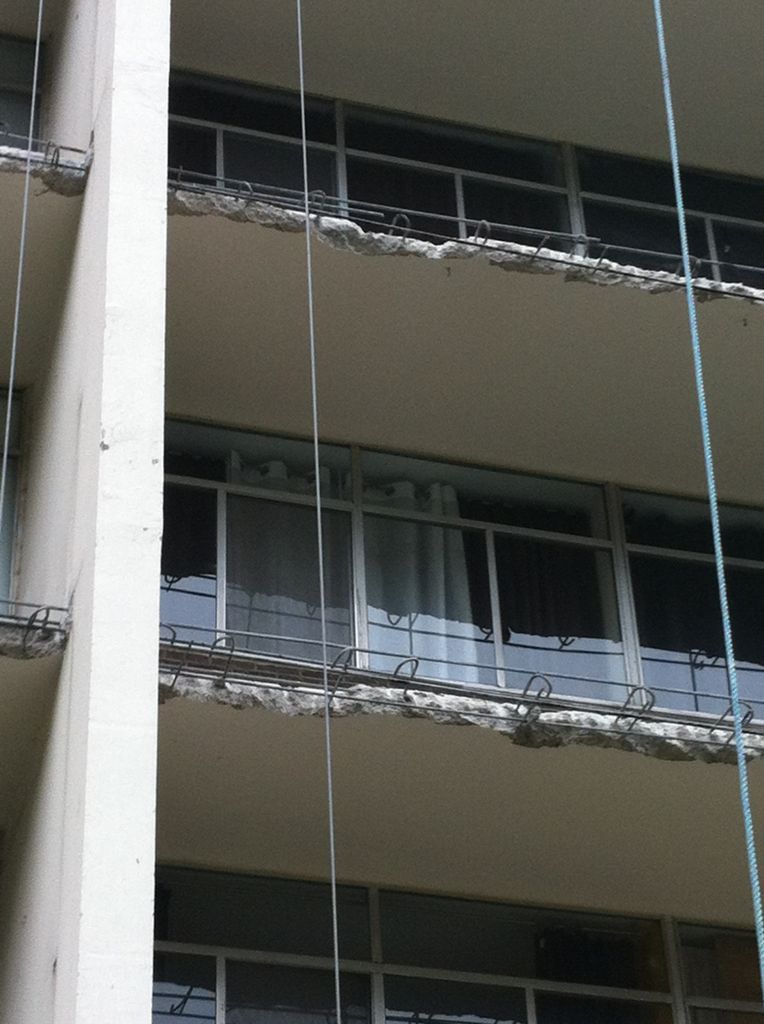
As the steel corrodes, it expands and causes the overlying concrete to work loose. This loose concrete is, of course, at risk of falling from the balcony slabs and therefore presents a serious safety risk.
Carbonation is more of an issue on the undersides of slabs than it is on their vertical surfaces or topsides. This is because the top surface and vertical edge are more frequently wet from precipitation. This moisture in the concrete actually helps protect against carbonation by effectively blocking the concrete pores.
What can be done to minimize balcony failure?
Design/construction professionals can help reduce the risk of these failures by specifying durable materials, properly detailing the slab edges, and enforcing the ultimate design.
Specify and install durable concrete
Carbonation is a self-limiting process. As concrete carbonates, it becomes less porous, eventually limiting its own exposure to carbon dioxide in the air. In other words, the speed at which the ‘carbonation front’ progresses into the concrete slows down over time.
With high-quality concrete, even in a building 30 or more years old, the depth of carbonation should not exceed 5 or 10 mm (1/5 to 2/5 in.). With reasonable-quality concrete, the carbonation depths can reach perhaps 20 or 25 mm (4/5 to 1 in.). Only very-poor-quality concrete is susceptible to greater depths.
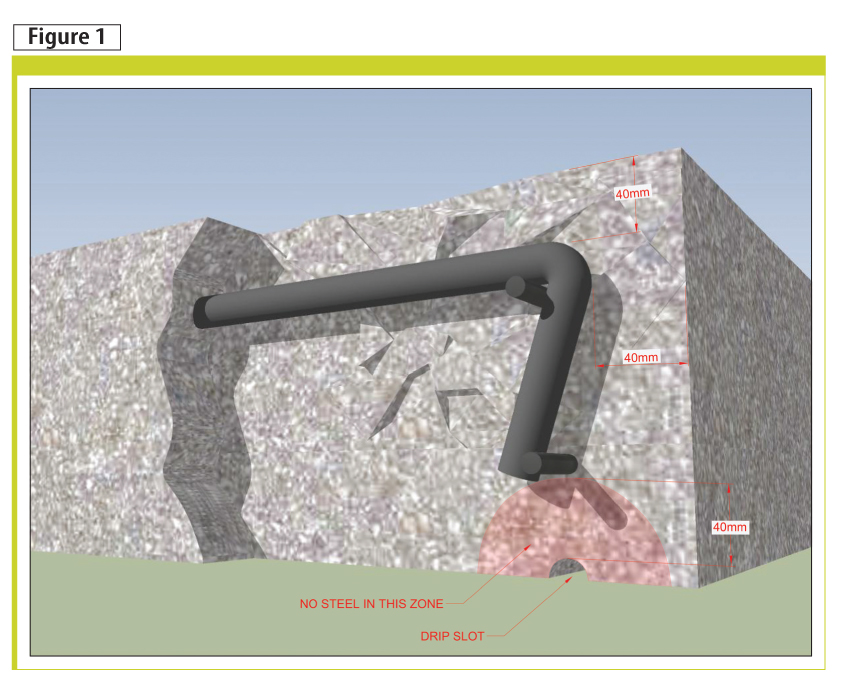
care must be taken to ensure no steel is placed in the bottom 40 mm (1 3/5 in.) of concrete, with particular attention paid to the zone around the drip slot (shown in red).
Using high-quality concrete reduces the total depth of carbonation for the life of the building. At a minimum, Class F-1 air-entrained concrete should be specified—this material is designed for exposure to freezing and thawing. Class C-1, designed for exposure to chlorides (which, like carbonation, cause embedded reinforcing steel to corrode) would be even more durable.
Air-entrainment is a feature of both F-1 and C-1 concrete—it distributes minute air bubbles throughout the concrete. These bubbles provide the space to accommodate the expansion that naturally occurs when water freezes. Non-air-entrained concrete specified for the interior floor slabs (which are not subject to freeze-thaw or chlorides) should not be inadvertently extended into the balcony slab areas. The proper concrete, designed for exposure, must be used when pouring the balcony slabs.
Carefully detail the slab edges
As indicated, carbonation most strongly impacts the undersides of slabs. For example, on a 30-year-old balcony, the carbonated layer of concrete might be 20 mm (4/5 in.) deep on the underside, 10 mm deep on the vertical edge, and only 5 mm deep on the top surface.
ASTM A23.1, Concrete Materials and Methods of Concrete Construction,which is referenced by the National Building Code of Canada (NBC) requires the rebar on balconies to have 40 mm (1 3/5 in.) of concrete cover between the steel and the exposed surface for concrete exposed to the exterior. So if carbonation normally only reaches depths of about 20 mm, why are balcony slab edges falling apart?
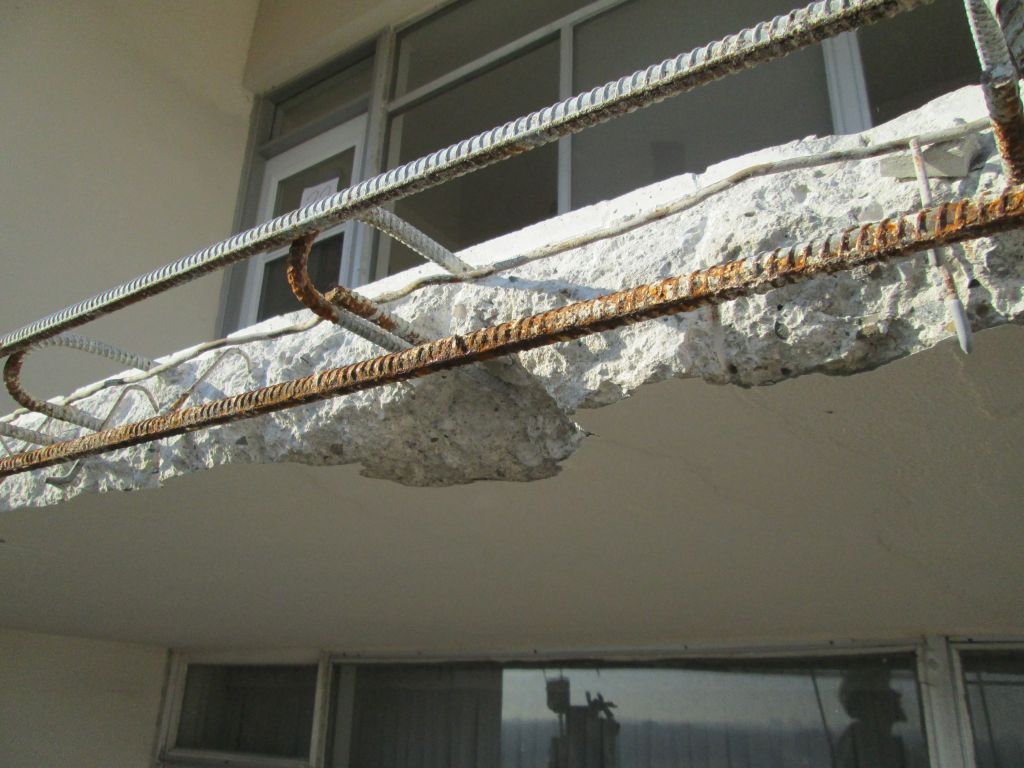
As is often the case, the answer to this question is an unintended consequence of another normal detail on a balcony slab: the drip slot. The drip slot functions to prevent rainwater that spills over the slab edge face from running back and staining the slab’s underside.
The drip slot is placed on the underside of the balcony at the outside edge. It is typically formed using a piece of wood laid in the formwork for the slab. This displaces concrete, which locally reduces the material’s depth over the rebar. The drip slot location usually lines up directly below and near reinforcing steel running along the slab’s bottom edge—this creates the perfect opportunity for carbonation to reach the steel, initiate corrosion, and cause the slabs to delaminate (Figure 1).
The drip slot may seem like a minor issue because it is so small relative to the slab’s size. Nevertheless, it is, in essence, the Achilles heel of balcony slab construction. This small area of reduced concrete cover causes the carbonation front to reach the steel, which then results in the corrosion that eventually requires rebuilding of the balcony slab edges.
To help prevent this, designers should ensure the drip slot is clearly indicated on construction drawings, with all necessary dimensions for slot location and size. Details should indicate the minimum distance of reinforcing bars to the drip slot as well as to all exposed concrete faces.
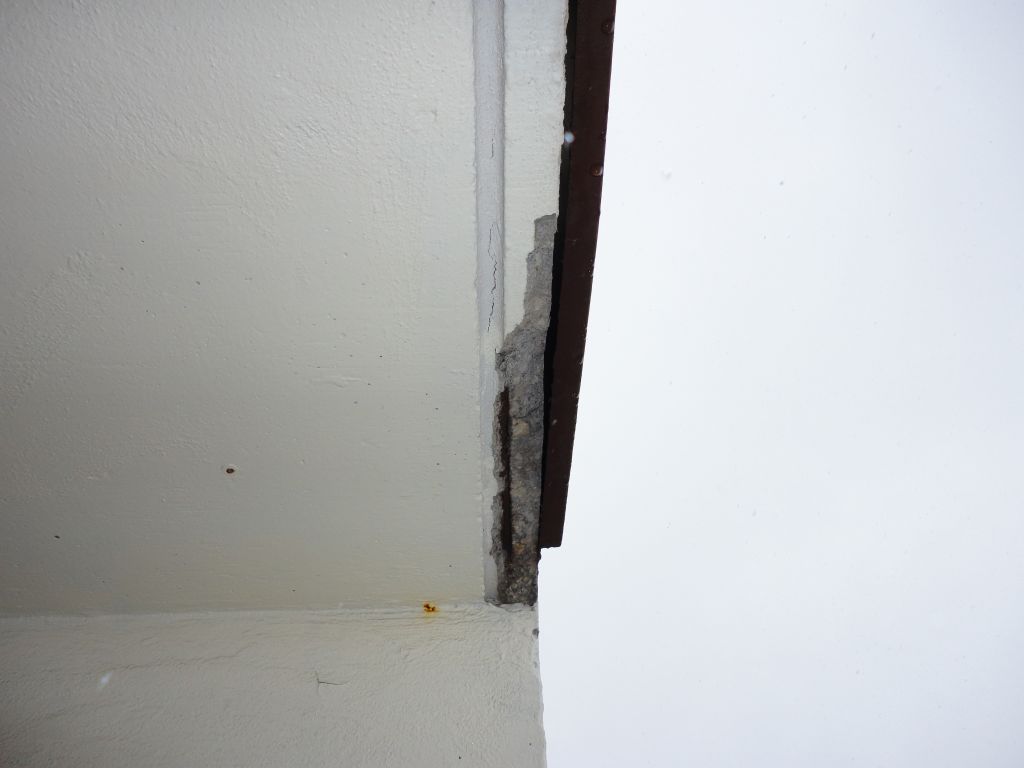
The drip slot design should also clearly allow for adequate concrete cover to the adjacent steel. This cover should be at least 40 mm (1 3/5 in.), taking care not to allow any unintended reduction at drip slots. This may require the structural engineer to slightly modify the steel’s placement in this location.
As a belt-and suspenders approach, designers might also consider specifying any rebar running parallel to (and just above) the drip slot be epoxy-coated. While this will not prevent carbonation, it still helps protect the steel should, by chance, it get installed without the intended cover in isolated locations.
Enforce the design
During construction, care should be taken to position the reinforcing steel and form the drip slots as indicated in the improved design details. It will help if the formwork contractors understand why this particular detail is important. This way, they will be partners in prevention—the installers will know the care they take with their work will save future owners money, and residents and guests a lot of disruption.
Conclusion
As an industry, architects, structural designers, and contractors must step up and work together to build durable concrete balconies that will not be susceptible to carbonation-induced corrosion. Making even these few minor changes when designing and forming balcony slab edges can go a long way toward preventing deterioration to concrete balconies. More importantly, these changes can be made with almost no additional cost to the construction.
Gavin Lobo, P.Eng., is a project manager with Halsall Associates, a consulting engineering company with seven offices across Canada. He specializes in the repair of reinforced concrete structures as well as building envelope elements, including roofs and windows. Lobo can be contacted via email at globo@halsall.com.
Sally Thompson, P.Eng., is an executive vice-president and National Practice Leader for Property Condition Assessment services at Halsall. She acts as project principal for a wide range of capital planning and restoration projects for various building types. Thompson can be contacted via email at sthompson@halsall.com.
John Kosednar, P.Eng., is a managing principal at Halsall. As a corrosion specialist, he oversees the evaluation and repair of reinforced concrete structures, as well as other restoration projects on various building types. Kosednar can be contacted via email at jkosednar@halsall.com.
To read about the two basic balcony configurations, click here.