Building in the Bathroom: A new way to build in wet areas with building panels
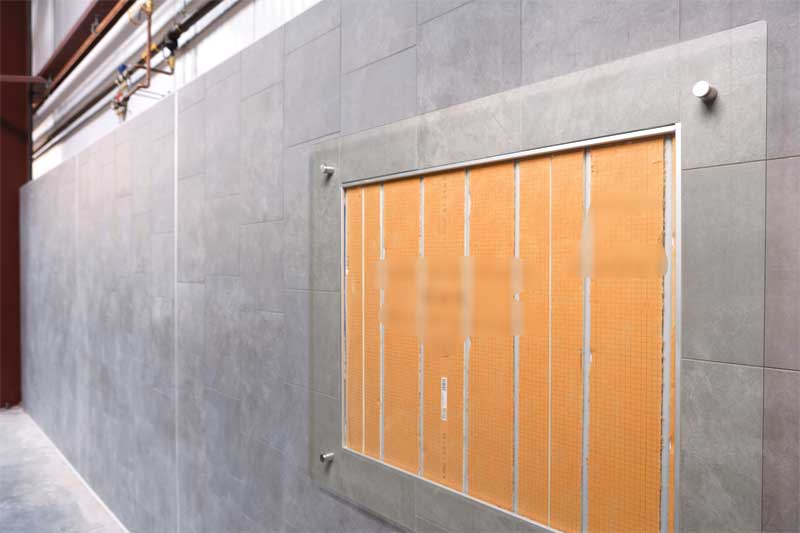
International examples
Building panels can also simplify some very unique and challenging projects, such as one application where a series of tub-surrounds were needed to encase oval bathtubs for a resort project in Grand Cayman Islands. This particular project was a turnkey installation where all material and labour were being supplied by a tile contractor based out of Toronto. It was essential to have a system that was easy to assemble, and capable of handling the heavy weight of the stone being applied on the tub surround.
The building panel chosen for this project was cut and shaped using basic computer numerical control (CNC) equipment and the pieces for each tub surround were packaged as a kit and sent to Grand Cayman for assembly onsite. Once at the resort, each tub surround was assembled within one day by an installer and a helper. It would have been much more challenging and the shipping much less economical if the kits had been made with another solid backing such as CBU.
Another unique application was at a corporate headquarters based in Reno, Nev., where the proposed design called for several faucets to empty into a single long communal sink in each washroom. One linear drain was used per sink, essentially creating a long trough drain. The entire sink was built using building panels.
The combination of their light weight and strength allowed the sinks to be cantilevered from the wall using a ledger made of a stainless steel profile made specifically to work with the building panel. A supporting leg was built on one end, constructed with 50-mm (2-in.) thick building panels and no lumber. Building these sinks with traditional materials would have been extremely time-consuming and challenging.
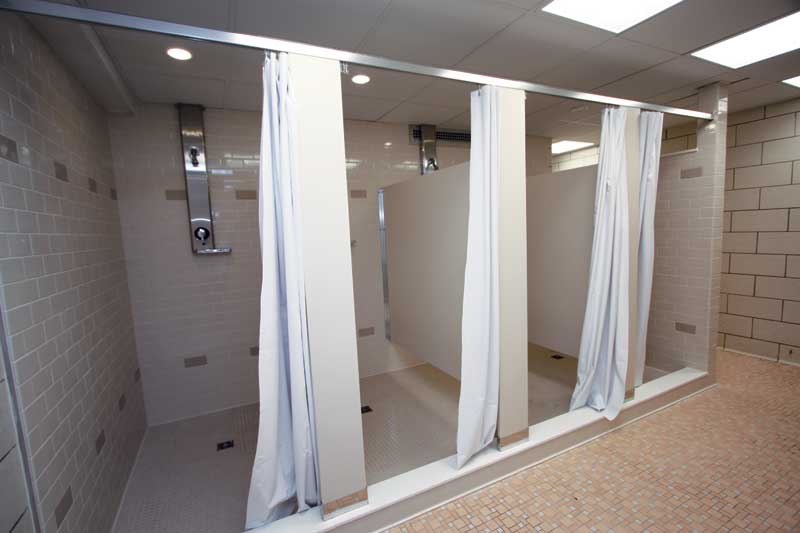
At the same Reno facility, the building panel was used in the walls in the warehouse where a 37.5-mm (1 ½-in.) thick panel with an R-value of approximately 6.5 was used to insulate all the 2.4-m (8-ft) high walls around the warehouse. The board was not only used for its R-value, but it was also routed out to hold the hydronic pipe, which was heated by a geothermal system, making the warehouse exceptionally energy efficient and quick in reaction time.
Traditional office and distribution buildings in the Tahoe Reno Industrial Center (similar to this facility in size and use) typically have total energy consumption costs ranging between $13.45 and $16.14 U.S. per square metre ($1.25 to $1.50 U.S. per square foot) per meter squared. Over the past two years, this building has been running at a cost of $4.62 U.S./m2 ($0.43 U.S./sf), or an overall cost saving of approximately 65 per cent. The board was tiled with a porcelain tile which has a much longer lifecycle than finishes such as drywall and paint.
Conclusion
Waterproof building panels, like many other relatively new construction materials, change the way structures are built in two dramatic ways. The first is they help to provide better results more quickly in relatively standard applications like residential showers and university dormitory showers. The second is the role they play in expanding the affordable possibilities in construction.
Wall-mounted sinks with trough drains, hydronic heating in walls, and oval tub surrounds that are prefabricated at the factory and installed in Grand Cayman—these are all creative solutions that are made much more attainable through the use of lightweight, waterproof building panels.
DESIGNING FOR STEAM ROOMS |
Steam rooms have been a real challenge in the tile industry as vapour is very difficult to contain in an enclosed room, especially in continuous use steam rooms commonly found in commercial environments such as in fitness centers or spas. In the most recent revision (i.e. 20122014) of the Tile, Terrazzo, Marble Association of Canada’s (TTMAC’s) 09 30 00 Tile Installation Manual (2012-2014), the detail for continuous use steam rooms was modified, providing two options to meet the vapour retarder requirements. Where the waterproof membrane acts as the waterproofing membrane and the vapour retarder, the waterproof membrane must have a perm rating of 0.5 or less using procedure E of ASTM E96 with 90 per cent humidity. Alternatively, if the waterproof membrane has a perm rating higher than 0.5, then a vapour retarder should be used that has a perm rating 1.0 or less when tested with ASTM E96 procedure A, which is typically located behind the solid backing such as cementitious backer unit (CBU). In the case of building panels, depending on the thickness of the board, the perm rating can be met simply by using the boards. If the thickness of board used does not have a perm rating less than 0.5, a waterproofing membrane can be applied over the board, which will lower the perm rating almost to zero. |
Dale Kempster, CSC, CTC, TTMAC, is the technical director of Schluter-Systems (Canada), and has been with the company for 25 years. He is the president of the Materials, Methods, and Standards Association (MMSA) in the United States, and was on the Terrazzo, Tile, and Marble Association of Canada’s (TTMAC’s) board of directors for 14 years. Kempster co-chairs the Specifications and Technical Research Committee and is chair of the TTMAC 09 30 00 Tile Installation Manual. He is the current chair of the Canadian Advisory Committee for the International Standards Organization (ISO [TC189]). Kempster also co-chairs the MMSA Sound-control Committee and served as co-chairperson of the MMSA Crack-isolation Committee. He is a graduate of the Certified Tile Consultants (CTC) program given by the Ceramic Tile Institute of America (CTIOA). Kempster can be reached via e-mail at dkempster@schluter.com.