Building Durable Structures: From concrete mixes to waterproofing strategies
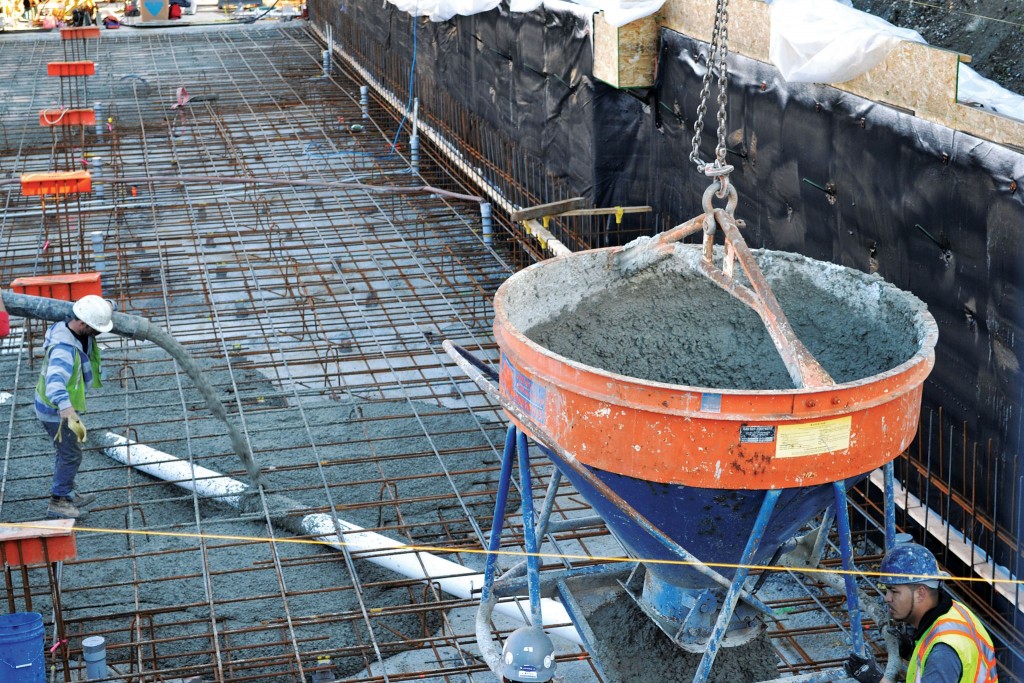
Advantages with supplementary cementitious materials
Another solution to prevent water penetration is through the use of supplementary cementitious materials (SCMs) such as silica fume. These components are materials added in conjunction with concrete’s basic form—water, portland cement, and fine and coarse aggregate. These SCMs make up a portion of the cementitious material within a concrete mixture, which means the proportion of cement in a given mixture will lessen as SCMs are added. Some engineers and concrete suppliers point out they can use silica fume and other materials to produce a concrete mix that has very low permeability and can be considered watertight.
SCMs are used for various reasons within a concrete mixture, which includes a means to increase durability. According to the National Ready Mix Concrete Association (NRMCA):
These materials modify the microstructure of concrete and reduce its permeability thereby reducing the penetration of water and water-borne salts into concrete.
Thus, the addition of SCMs can aid in creating a watertight structure that, in turn, will create a durable end structure.
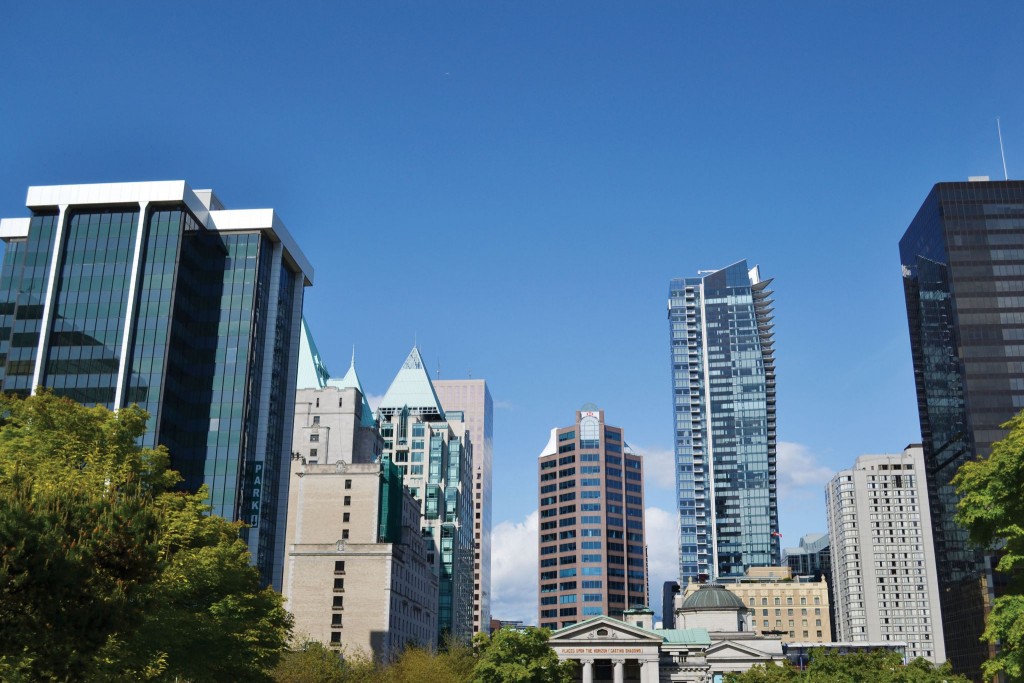
However, silica fume, and other SCMs used to increase concrete strength and durability by densifying the mixture to block the flow of water, is not in and of itself a waterproofing material. SCMs can contribute to reducing concrete permeability and be complementary components in a well-proportioned mixture, but they do not make the material watertight. Further, they must be used at an optimal dosage or drawbacks will be seen. For instance, the use of silica fume in concrete shows a tendency for cracking, resulting in water penetration and corrosion of reinforcing steel. This increased densification of the concrete often creates an illusion of waterproofing capability. In actuality, the use of silica fume will accelerate the deterioration process when cracking occurs.
This means optimally specified SCMs can significantly improve a concrete mixture’s lifespan, but an alternative solution must be used to create a completely watertight structure that will ensure a durable building.
Conclusion
In order to achieve a durable concrete structure, the permeability of the concrete mix must be as low as possible, which can be achieved with the proper waterproofing method. An externally applied membrane wraps itself around the concrete, protecting it from water ingress with a layer of material. However, if the shell fails, repair can be time-consuming, costly, and sometimes impossible. If using an internal membrane, the concrete matrix will be improved and will become the waterproofing barrier. By having a proper internal waterproofing system, your structure will be protected during its service life and not just during the short warranty period.
Alireza Biparva, B.Sc., M.A.Sc., LEED GA, is research and development manager/concrete specialist at Kryton International Inc. He has more than 20 years of experience in the field of concrete permeability. Biparva oversees several research projects focusing primarily on concrete permeability studies and the development of innovative products and testing methods for the concrete waterproofing and construction industries. He is an active member with the American Concrete Institute (ACI), and has given more than 300 presentations on concrete permeability, waterproofing, durability, and sustainability around the world. Biparva can be reached by e-mail at alireza@kryton.com.