Blistering Over Concrete: Getting ahead by going beneath the surface
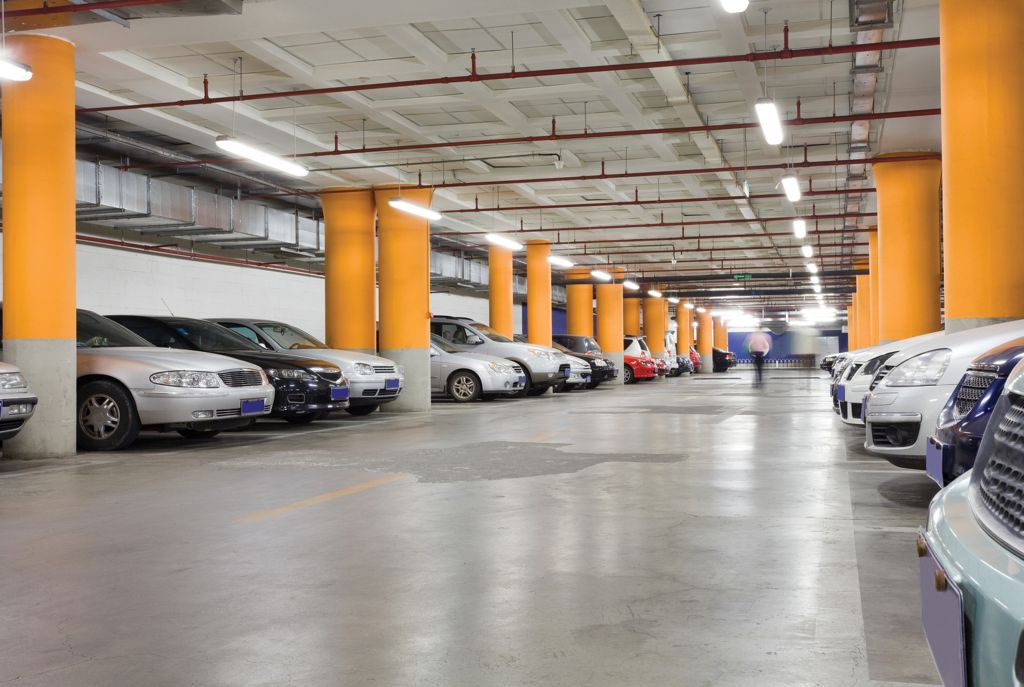
By Peter Culyer
Anyone involved with concrete finishing and protection—either through design, supply, or installation—is likely to have been affected by blistering and other moisture-related failures on floor finishes. A multi-million-dollar problem in North America, there are numerous reasons for such failures. However, a conversation being had more frequently today surrounds the relationship between alkali-silica reaction (ASR) and near-surface alkali reaction (NSAR) and finishing failures.
ASR has been a subject of increasing research and failure investigation over the past 30 years. While a previously identified phenomenon, it would appear greater intensity into identification/testing methods have only recently (in relative terms) emerged. Simply stated, ASR is the reaction between cement’s hydroxyl ions (forming highly alkaline solutions such as calcium hydroxide) with reactive (i.e. acidic) silica aggregates. These include:
- chert;
- quartzite;
- opal; and
- strained quartz crystals within aggregate (larger) components.
This reaction within the concrete matrix’s porous structures leads to the production of a gel—calcium silicate hydrate. Through both absorption and adsorption of greater amounts of moisture, the formed gel swells and causes cracking.
Telltale signs such a reaction may be present and/or has occurred is web-type cracking patterns. However, such patterning may be related to other issues and ASR requires deeper investigation to confirm its presence. Where this can become particularly important is in areas of once bare and unfinished concrete being repurposed and requiring application of some form of coating.
NSAR is a more recent area of research and diagnosis. More than ASR, it is associated with blistering of low-permeance coatings on concrete. Like ASR, NSAR is the reaction between hydroxyl ions and reactive aggregates; what differentiates the two is the aggregates involved. While ASR is believed to be primarily related to larger aggregates, NSAR is believed to stem from potential reactions between hydroxides and smaller aggregates, including sands.
There is increasing research to suggest this reaction may be of greater significance than reactions with larger aggregates. Some may point to time required for the development and effects of each to manifest itself, with NSAR being believed to happen over a short period, and ASR sometimes taking years to become apparent.
Cause and effect
Efflorescence is a condition fairly familiar to most design/construction professionals, as it is one of the first signs of moisture problems for cementitious materials. A by-product of moisture combining with free salts, this phenomenon can be an esthetic issue (as it is a white powdery substance), but it can also cause the material to weaken.
Like efflorescence, ASR and NSAR require the confluence of no less than three contributors, as shown in Figure 1. However, unlike efflorescence, these reactions are predominately associated with various forms, and cracking and eventual spalling. The degree of spalling can be quite significant and explains why a great amount of research can be found on ASR in connection with concrete use in roads and airfield runways.
The American Association of State Highway and Transport Officials (AASHTO) has developed numerous ASR guidelines that are highly informative and instructive on steps to take for its detection and consequent actions. While related to road works, much of what they describe would be applicable to the built world in general.
Figure 2 is taken from the U.S. Federal Highway Administration ASR survey and tracking guidelines, relating to its Survey and Tracking Alkaline-Aggregate Reactions (STAR) approach, beginning with a condition state analysis. It should be noted this is a truncated look at their program, but nevertheless gives a flavour of their approach.
The STAR approach quantifies what ‘good,’ ‘fair,’ ‘poor,’ and ‘severe’ mean (Figure 3), along with qualifying hairline, narrow, and medium. What to do about the determined state will depend on current function, future functional need, and criticality of function—this is where a decision tree would be helpful in standardizing an approach. Options from the guidelines are depicted in Figure 4.
Understanding NSAR
ASR is visually assessable, at least to some degree. NSAR, on the other hand, tends to be somewhat more discrete due to the subsurface nature and the affected depth. The relationship between NSAR and osmotic blistering in coatings is an area this author believes there must still be more research. While osmotic blistering is documented and understood in certain coating sectors (e.g. coating of concrete containment tanks), the association with imbalances in pH between semi-permeable surfaces and an impermeable one (e.g. low-permeance coating) is most always absent of linkages to NSAR.
In connection to NSAR, mechanisms reviewed could go to piece together the following linkage to osmotic blistering. The presence of calcium silicate hydrate (i.e. gel), or even simply the creation of a silicic acid, draws greater levels of moisture from various depths within the concrete—likely in relationship to porosity and available localized reactive silicates. This creates pockets of osmotic cell pressure.
As the isolated area looks for greater dilution to balance the pH with the surrounding area, it draws more water toward it. Osmosis occurs across the semi-permeable layer, while low-permeance coatings do not allow for its evacuation, causing a blister to form in these areas (Figure 5). Unlike vapour pressure, which is not believed to be capable of blistering a well-adhered coating, osmotic cell pressure is capable of creating sufficient pressure to lead to blister formation, particularly if developed within the first seven or so days of a coating’s application.
Although not required for osmotic cell pressure to cause a blister, inhibited bonding mechanisms and time of application and curing would certainly increase the likelihood. One could perhaps go further and suggest a relationship with through dry/curing rates of the coating and blister likelihood should the other required contributors (e.g. sufficient moisture and solution) be present.
NSAR and osmotic blistering
Unfortunately, there are no straightforward or easily deployable detection methods for NSAR. Assessment and elemental analysis can be made through petrography, scanning electron microscopy (SEM), and electron dispersive spectroscopy (EDS). However, taking these steps likely means a problem is already being experienced. Prevention should be the key.
There are actions that can be taken to avoid the consequences of NSAR, similar behaviours, and osmotic blistering. In addition to admixtures to deal with ASR in concrete, there are special primer coatings meant to prevent osmotic blistering. In practical terms, blistering of concrete coatings can be steeply mitigated through gaining an understanding of the concrete’s pH and vapour transmission, or its moisture vapour emission rate (MVER). While focusing on osmotic pressure and blistering, most of what is noted in coating guides for prevention of osmotic blistering would also be applicable steps in arresting NSAR effects on low-permeance coatings.
The most obvious step to take begins before the concrete is poured—that is, at the design stage. As previously suggested, if the concrete is to be coated, then it is of particular importance to ensure all aggregates have been screened and tested for reactivity potential, such as through ASTM C1260-07, Standard Test Method for Potential Alkali Reactivity of Aggregates (Mortar-Bar Method).
Concrete-modifiers such as supplementary cementing materials (SCMs) and concrete admixtures may be carefully considered as well. As with any concrete application, the blend should be tailored for its purpose and time of year use.
In addition to concrete composition, the configuration should seek to mitigate vapour transmission through the slab. Use of an ultra-low-permeance vapour barrier beneath the concrete, suitable for the substrate on which it is laid, brings control to one of the aforementioned contributing factors by taking moisture loading from ground sources out of play.
The question is, once all other factors are under control, how soon is too soon to apply the low-permeance coating? ASTM has standards for the determination of vapour emission rate in concrete and material RH. These protocols should be in the wheelhouse of concrete coating contractors—particularly those applying high-end, low-permeance coatings. It may also be an area where third-party validation is prudent.
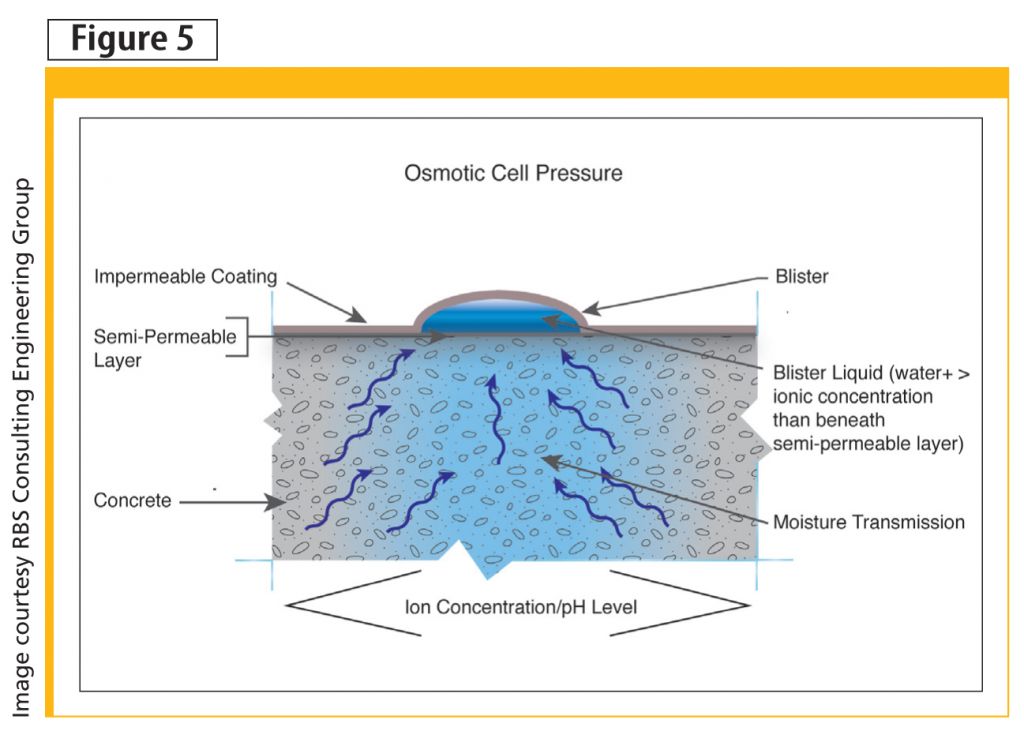
Like other phenomena described in this article, osmotic blistering would appear to have certain dependencies for its development. These would include:
- sufficient moisture and resultant moisture vapour emission through the slab;
- semi-permeable region or primer; and
- very low or impermeable coating or layer.
To avoid osmotic blistering, control of these factors is essential. Since there may be little in way of options around the permeability of the coating, the design professional must instead manage moisture, vapour emission, and pH.
High pH can be detrimental to numerous types of floorcoverings. There are many solutions available to deal with high pH levels, from simple water rinses to chemical and proprietary treatments. However, care must be exercised to ensure one stays within the coating manufacturer’s pH range. High pH may also be indicative of elevated moisture; they should never be looked at in isolation from other factors. Moisture content levels can be measured through moisture metering—ASTM D4263, Standard Test Method for Indicating Moisture in Concrete by the Plastic Sheet Method, and the like.
Understanding moisture vapour emission rate is somewhat more involved. There are various methods deployed with mixed measures of success. Alas, the ‘time’ and ‘well-it-looks-good-to-me’ strategies are sadly still in use today. This is not entirely surprising given there is little readily available from coating manufacturers in terms of objective methodologies to use before coating applications. There is plenty of warning about not applying coatings until dry, or to where vapour transmission may occur during application. Ultimately, however, there is little if anything that quantifies what these mean (as there will always be some amount), or how to determine the rate of transmission.
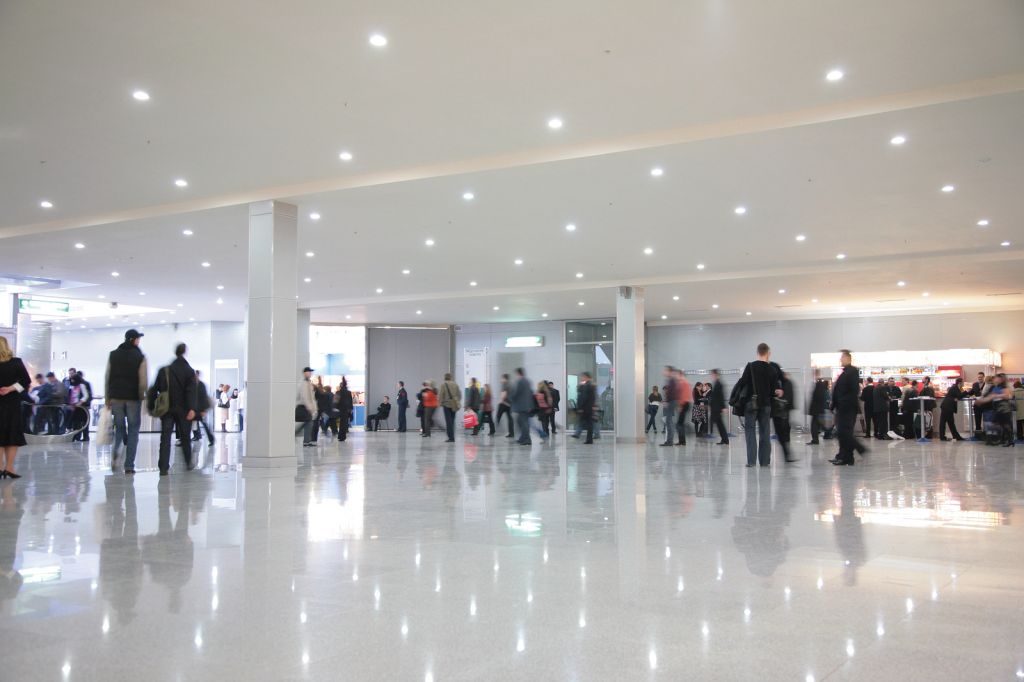
While thresholds will vary from product to product,1 a commonly expressed threshold is 3 lb per 1000 sf per 24 hours, as established through ASTM F1869, Standard Test Method for Measuring Moisture Vapor Emission Rate of Concrete Subfloor Using Anhydrous Calcium Chloride. How long it takes for concrete to reach this rate is going to depend on numerous factors. Without use of supplemental additives, or after-application conditioners, this period is unlikely to be less than 28 days. It can be considerably longer depending on concrete composition, slab thickness, time of year, and other factors.
If the MVER is found to be too high, and construction schedule too short, there are treatments for use over concrete to slow these rates down, but only to a point. Their deployment should not be stretched beyond the stated limitations.
Conclusion
Concrete and high-end coatings are a long-term investment, the returns of which can be enjoyed for years. It is worth taking investigative steps to understand the concrete’s condition before moving ahead with its covering. The bottom line is ‘know before you go’—that is, understand the situation before application.
Clear construction documentation/specifications, competent contractors, technically astute suppliers, and third-party specialists all go toward successful outcomes when blended correctly to make for a solid mix.
Peter Culyer is a project manager with RBS Consulting Engineering Group in Innisfil, Ont. He was previously technical services manager for Dryvit Systems Canada—an exterior insulation and finish systems (EIFS) and specialty coatings manufacturer. Culyer can be contacted via e-mail at p.culyer@rbsengineering.ca.