Better blankets for greener buildings
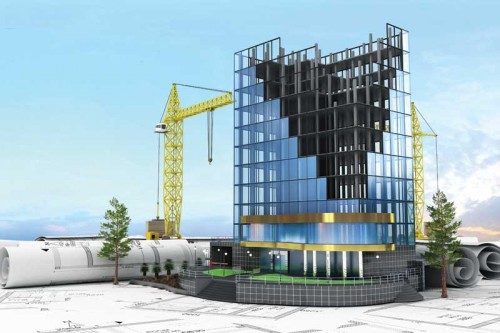
By Amir Hassan, M.Sc., P.Eng.
The scientific community has virtually agreed the planet’s atmosphere is changing due to greenhouse gas (GHG) emissions generated by human activities. The Paris Conference’s agreement, within the structure of the United Nations Framework Convention on Climate Change (UNFCCC) in December 2015, marks a change in direction toward a greener planet.
It confirms the target of keeping the rise in average global temperature below 2 C (3.6 F), as scientists believe a greater increase would be very dangerous. The agreement even establishes, for the first time, that a maximum rise of 1.5 C (2.7 F) should be the goal in a bid to protect island states, which are the most threatened by the rise in sea levels.
In typical buildings, space heating and cooling are usually the biggest consumers of primary energy, and consequently, are the largest contributors to carbon dioxide (CO2) emissions. Therefore, the logical approach for design/construction professionals is to reduce building energy use by creating better environmental barriers separating the interior and exterior climate conditions.
Codes and standards
In North America, an ambitious move toward sustainable building began almost two decades ago with the U.S. Green Building Council (USGBC) launch of Leadership in Energy and Environmental Design (LEED) program. The rating system, which promotes the use of building envelope systems with better performance by directly and indirectly offering some reasonable credit points, has diversified for different types of projects and spread to Canada and around the world.
While the LEED rating system (and others like it, including Green Globes) may have trail-blazed the green evolution in buildings, in many cases it remains voluntary and unenforceable. Prudently, then, recent building and energy code updates have refocused requirements on energy efficiency in buildings and a lower carbon footprint. The optimal goal is true net-zero-energy (NZE) projects—buildings producing at least as much energy as they consume on an annual basis.
Design/construction professionals and building envelope consultants in particular must do their part in ensuring building skins are adequately insulated when it comes to opaque walls, roofs, floors, fenestration, doors, and skylights.

Images courtesy Amir Hassan
In general, the newest energy codes are ahead of the present local market’s standards. Therefore, manufacturers need to keep up by improving their systems (especially exterior wall assemblies) to satisfy the new codes. Historically, that improvement process happened with glazing systems—today, one struggles to find exterior single-pane glass panels on a new Canadian building. Similarly, triple-pane insulating glass (IG) units, dynamic curtain walls, and double-skin façades will eventually replace mainstream double-glazed IG systems in the future.
The prescriptive path of the latest National Energy Code for Buildings (NECB) requires high-performance exterior walls with thermal resistance values ranging from RSI-3.2 to RSI-5.6 (R-18.2 to R-31.8), depending on climate. In other words, for a building in Edmonton to comply with the prescriptive path of the 2011 NECB, the above-ground opaque exterior wall system should have a maximum overall thermal transmittance of 0.21 W/m2.K, which is almost an RSI-4.8 (R-27.3) wall—this takes into account the effects of thermal bridging. In essence, this is a very high RSI-value for conventional exterior wall assemblies available in the local market.
Full adoption (or adaptation) of the 2011 NECB by all authorities having jurisdictions (AHJs) across Canada is expected by the end of this year. The code represents a significant reduction in building energy consumption levels over the 1997 Model National Energy Code for Buildings (MNECB) by around 25 per cent, and outperforms American Society of Heating, Refrigeration, and Air-conditioning Engineers (ASHRAE) 90.1-2010, Energy Standard for Buildings Except Low-rise Residential Buildings, by 18 per cent.
Accordingly, Canada’s building envelope industry needs to understand and accommodate the new energy requirements to construct sensible façades economically and environmentally. Thus, the first logical step is to increase the thermal insulation values of exterior walls in order to conserve heating and cooling energy in buildings.