Better blankets for greener buildings
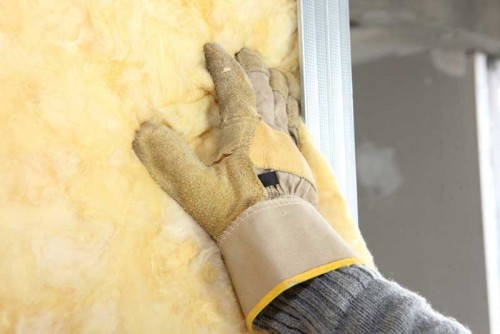
Water within the supporting structure would rot wood, corrode metal, and deteriorate concrete. This could compromise the building’s structural integrity, leading to very costly and inconvenient repair.
Mould is more of a growing problem within the building industry; there are many spore species known to cause adverse health effects in humans. Mould needs four essentials to survive: food (cellulose in most of building materials), oxygen, warmth, and water. Of these, three are challenging, if not impossible, to forgo from occupied spaces. Therefore, eliminating humidity in wall assemblies is the most viable way to ensure a mould-free building.
Besides the supporting structure (e.g. loadbearing masonry, stud wall, and metal deck roof assemblies) and the outer finish layer (e.g. brick veneer, vinyl siding, stucco, and metal cladding) serving as the weather shield, the building skin consists of three main layers: the thermal barrier, the water barrier, and the air barrier. The key to good design is understanding how those layers interact with one another and, most importantly, with the surrounding environment.
Depending on the position of the insulation layer, building skin types can generally be categorized as either:
- an interior insulated wall assembly (e.g. insulated stud wall assembly), where insulation can be inserted into the cavity between studs, and commonly secured by friction; or
- an exterior insulated wall assembly (e.g. basement wall or exterior insulation finish systems [EIFS]), where insulation would usually be installed on the outside and secured by a bonding agent or fasteners.
When it comes to increasing the thermal resistance of new and existing walls by adding insulation, some think it is a case of the more, the better. This can be true for thermal performance; but for wall durability, the increased probability of condensation occurrence within the new wall has to be carefully analyzed.
In some cases, adding insulation arbitrarily can actually be quite damaging. For example, with an existing building clad in EIFS, adding batt insulation in the wall cavity would reduce the surface temperature of the main membrane, because insulation performance depends on the difference in temperatures across the thickness.
In this instance, without a vapour-permeable membrane, interstitial condensation will eventually occur in the new wall. Hygrothermal analysis should be implemented to evaluate heat and moisture movements through buildings during design stage in order to reduce the risk of condensation.
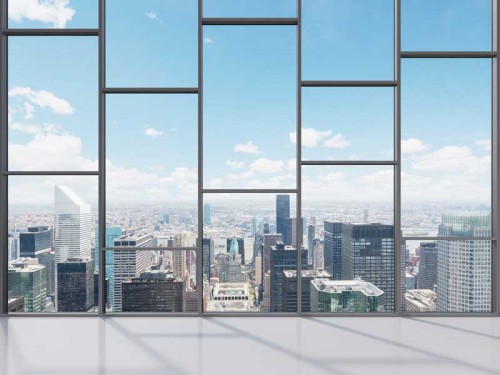
Adaptation process
If architects and designers cannot find sufficient systems under the prescriptive approach, they can try to trade-off some of non-compliant elements of the exterior shell with more efficient HVAC, domestic hot water (DHW), and lighting. Architects usually leave reducing window/wall ratio as a last resort. Therefore, proposed buildings with a substantial percentage of glazed surfaces will need either incredibly high-performing glazing or significant HVAC upgrades to achieve compliance.
It is important to note a maximum fenestration-and-door-to-wall ratio (FDWR) of 20 to 40 per cent, depending on the climate region in which the project is located, is allowed in the 2011 NECB. Alternatively, the ‘performance path’ option can be taken, where there will be higher demand for employing thermal simulation software to be used in energy modelling software, such as National Resources Canada’s (NRCan’s) CAN-QUEST. (For more information, visit www.nrcan.gc.ca/energy/efficiency/buildings/eenb/16600).
While the performance path requires additional effort up-front in the form of energy modelling, it offers the greatest flexibility for demonstrating compliance. Further, it is often the only alternative when the design is non-compliant due to high FWDR. General consensus seems to be once energy modelling becomes a part of the design process, then exceeding the minimum code requirements is often cost-effective and desirable. Using energy modelling as a tool early on can also minimize costly redesigns and the need to introduce expensive technologies at the end of design.
To satisfy the energy codes as well as mitigate building envelope issues, architects and developers should engage sustainability and building science specialists to participate in or lead design choices for wall and glazing assemblies, provide or review building enclosure specifications, critique architectural and shop drawings, evaluate pre-construction mockups, and conduct onsite testing and commissioning. Testing and commissioning are important parts of the energy efficiency package to ensure systems operate in the way they were intended.
Amir Hassan, M.Sc., P.Eng., is a building science manager with WSP Canada Inc. He has more than 20 years of envelope experience in the Middle East, Europe, and North America, having worked with structural glass, curtain wall design and evaluation, frameless and skylight systems, structural assessment, weathertightness, thermal performance, cladding, roofing, and thermography. Hassan holds a bachelor’s degree in civil engineering, and a master’s degree in façade engineering. He can be reached via e-mail at amir.hassan@wspgroup.com.