Benefits of airtightness testing
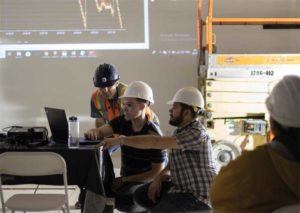
Specifications of tests
There are many ways to measure air leakage rates of buildings, and specifications are prone to misinterpretation by those with limited knowledge of airtightness testing. It is generally considered best practice to consult a testing agency with experience in evaluating large buildings. A building envelope consultant can help an architect set the bar, and will work with site supervisors and trades in the planning and construction phases.
Unless airtightness testing is mandated by a building code in a given municipality, or the project is aiming for a certification requiring airtightness testing, all testing will be voluntary, and is usually completed as part of a building envelope commissioning or quality control process. An airtightness test can be written into the project specifications by indicating:
- test type (Operational [HVAC-related openings as-is] versus Building [HVAC-related openings excluded or masked]);
- when it will be performed (for example, leading up to the final test, qualitative testing should be completed to sections of the building while the ABS is still accessible and quantitative tests must be undertaken as soon as the structure is closed in and the ABS is still accessible for repairs; all testing prior to the final test should be a rehearsal for the ‘big final test’ where the aim is to achieve the tightness requirements and not having to search for air leaks last minute); and
- the target air leakage rate (e.g. Vancouver Green Buildings Policy for Rezoning [2017] sets it at 2 L/s∙m2 [0.4 cfm•sf] @75Pa, Denmark mandates 0.20 L/s∙m2 [0.04 cfm•sf] @75Pa, and 0.4 L/s∙m2 [0.08 cfm•sf] @75Pa, as per PHIUS+ 2015).
It is common for airtightness specifications to be misquoted, but bringing experienced testers into the process as early as the specification writing stage can be beneficial. The way building scientists typically measure air leakage in small versus large buildings, for example, differs. In small, Part 9 buildings, the air leakage is proportional or normalized to the conditioned volume and is communicated as air changes per hour (ach) 50 or @50 Pa. In large buildings, however, the leakage rate is normalized to all six sides of the surface area, including slab, soffit, roof, above- and below-grade walls, and window areas, and is communicated as litres per second per square metre of envelope surface area (L/s∙m2). The metrics can get confusing, so special attention must be paid to them. One can reference the metric to imperial conversion tables in the Illustrated Guide to Achieving Airtight Building by B.C. Housing.
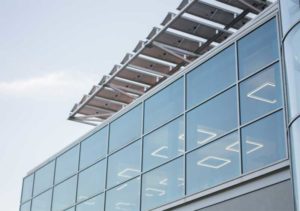
For comparison, the American Society of Heating, Refrigerating and Air-Conditioning Engineers (ASHRAE) 90.1-11, Energy Standard for Buildings Except Low-Rise Residential Buildings, deems a building airtight if leakage rate is below 0.5 L/s∙m2 (0.1 cfm/sf) @75Pa, and average building air leakage rate is below 1.5 L/s∙m2 (0.3 cfm/sf) @75Pa, and leaky is 3 L/s∙m2 (0.6 cfm/sf) @75Pa.
Mandatory testing
Codes and certifications mandating airtightness testing include the Washington State Building Code (SBC), B.C. Energy Step Code, TGS v3, Leadership in Energy and Environmental Design (LEED), EnergyStar Multifamily High-rise Pilot, and Passive House.
Several years ago, Washington State introduced mandatory testing for all buildings with a voluntary target. This acted as a ‘soft push’ for the industry to move toward high-performance building.
For Part 3 residential buildings, LEED has a credit for single-unit compartmentalization airtightness testing with a mandatory minimum performance threshold. The EnergyStar for Multifamily High-rise Pilot Program in Ontario has taken this one step further, requiring not only compartmentalization testing, but also whole-building airtightness testing. Airtightness testing is also required when energy code compliance modelling claims credit for improved airtightness metrics.
It is anticipated with the shift toward performance-driven approaches to energy efficiency in buildings in an attempt to reduce carbon emissions, mandatory testing enforced by either building codes or project owners will become commonplace.
Conclusion
Presently, TGS does not specify a target air leakage rate. To prevent undue hardship for the building industry while also bringing up the quality of building stock in Toronto, it is likely an airtightness performance threshold will be introduced eventually. Nothing currently prevents building owners from setting their own performance thresholds and committing the construction team to a higher standard like Passive House, which sets one of the most stringent leakage rates (the Passive House Institute U.S. (PHIUS) airtightness requirements have been adjusted from a limit of 0.6 air changes per hour [ACH] 50 for Part 9 and from 0.02 L/s [0.05 cfm] 50 and 0.04 L/s [0.08 cfm] 75 per square foot of gross envelope area for the high-rise residential, commercial, and institutional sectors). Achieving building airtightness does not require a transformation in process or new technologies, but rather a change in work culture that consistently focuses on the small details needed to assemble a continuous ABS.
Austin Todd, CPHC, CEA, is the cofounder of the consulting firm CoEfficient Building Science, and focuses on business development in both the residential and the commercial sector. A building science enthusiast, Todd is committed to accelerating the transition to a zero-carbon built environment. He is on the board of Passive Buildings Canada. Todd can be reached at atodd@coeff.ca.
Greg Labbe, CEA, CET, runs the building science laboratory for the Graduate Studies programs at Ryerson University, Toronto. He also does contract work with Russell Richman Consulting Ltd. Labbe specialises in non-destructive testing of building enclosures, with a specialty in large building airtightness/air leakage testing using multiple, computer-controlled and logged blower door fans. He can be reached at glabbe@ryerson.ca.