Benefits of airtightness testing
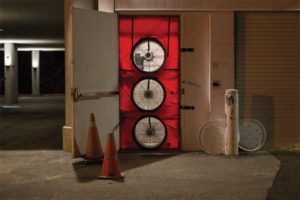
the building.
Images courtesy CoEfficient Building Science
A Building Envelope test requires temporarily masking ventilation openings to measure the leakage rate of the building’s enclosure while removing leakage through mechanical systems from the results. This kind of test is usually used to meet the requirements of a building performance standard like EnergyStar or Passive House (PH or its U.S. version, PHIUS). Currently, TGS does not make a distinction between the two tests. Since the as-operated test method is less onerous, it will likely be the most specified one.
Testing to quantify the building’s air leakage rate is performed at substantial completion of the ABS, prior to occupancy. Some standards (e.g. PH) require testing at this phase to verify the building’s air leakage rate is below the acceptable certification threshold. If the building is not within the limits, additional air sealing work and tests would be required.
The building must be unoccupied on test day, with no trades or residents opening and closing exterior windows and doors. Prep work depends on the specifics of the test and the building type. This includes sealing mechanical vents and placing of blower door fans to keep the pressure uniform throughout the entire building. Typically, the enclosure consultant, project manager, and site supervisors are onsite to take notes on ABS deficiencies that need to be addressed prior to the final airtightness test. Ideally, even large buildings are tested as one whole ‘zone’ prior to occupancy, as was done with the 39-storey Incity building in Lyon, France, the Amazon Distribution Centre in Warsaw, Poland, and a 20-storey residential apartment building in Hamilton.
An alternative to single zone or whole-building airtightness testing is to evaluate sections of the building using the Guarded Testing technique. Guarded blower door testing is utilized when the whole building cannot be tested as one zone. The process involves isolating a representative section of the building, which is then sealed off temporarily from adjacent areas of the building, and all are tested at the same time (e.g. testing a single level of a multi-storey building when assessing the full building is impossible). However, it is unknown if the leakage through the isolated section of envelope accurately extrapolates to the full-building results—more on-field research is required. To this end, multiple guarded tests are being conducted during the construction phase of a high-performance, high-rise retrofit in Ontario. This will be followed by a final whole-building airtightness test. This project may provide insights on the feasibility of extrapolating data from one level to the whole building.
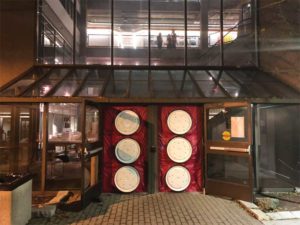
When to test
The authors’ recommendation is to test early, and often. As architect Tom Knezic suggests, it is best to plan for testing by including it in the critical path method diagram or in the Gantt charts. Ideally, all components of ABS are accessible during the test so repairs can be made as required, meaning during the construction process. However, whole-building testing is next to impossible in high rises, as the bottom third of the building is usually fully occupied before the top third is even enclosed. Therefore, some flexibility is expected on the part of the municipality because several guarded tests of a few representative floors are performed as the building sections are completed.
Most of the air leakage occurs where different components of the ABS come together, such as electrical, mechanical, plumbing, structural, and communication cable penetrations. Additionally, transitions at the roof-to-wall membrane, wall-to-soffit, and below-grade to above-grade wall can also be challenging. Simple visual inspection of the integrity of the seal between ABS components is a good start to ensuring the continuity of the air barrier system.
The transition joint between fenestration products and the rough openings is also a source of air leakage. Even if some windows are tested for air leakage, as per ASTM E783, Standard Test Method for Field Measurement of Air Leakage Through Installed Exterior Windows and Doors, and meet the requirements, the testing only measures air leakage through the fenestration product and not the integrity of the connection between the fenestration and the rough opening. The testing agency can quantitatively and separately test both and make recommendations on how to remediate the transition joint if excessive air leakage is measured.
Mockup testing can be used to verify airtight performance early in the project so changes can be made, if necessary. It is advisable to plan regular assessments of sections and use qualitative testing of ABS. Using ASTM 1186-03, Standard Practice for Air Leakage Site detection in Building Envelopes and Air Barrier Systems, air leaks in the ABS can be detected by employing theatrical fog or infrared thermography to pinpoint air leaks before they get covered in drywall, insulation, drop soffit, or brick. Once ABS is covered, repairs to make the envelope more airtight become prohibitively expensive.
As-operated testing and long-term airtight performance relies heavily on mechanically controlled dampers to control air leakage through mechanical systems. Rest assured, not all mechanically controlled dampers close well to seal under pressure, so selecting high-quality, remote-controlled damper systems in HVAC appliances ensures the lowest possible air leakage rate.