Benefits of airtightness testing
By Austin Todd, CPHC, CEA, and Greg Labbe, CEA, CET
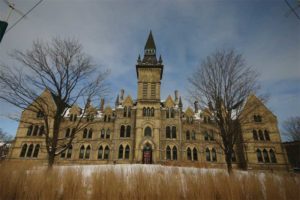
The drive toward a low-carbon environment means construction professionals are constantly refining the details of high-performance buildings. Though the industry is developing new materials to help achieve this, assembling airtight buildings is still a challenge. New and innovative air barriers are available for builders, but the challenge of integrating an air barrier system (ABS) comprising many connecting components requires attentive and caring tradespersons.
Performing airtightness testing on Part 3 buildings has been limited to high-performance projects. However, there is now a trend of mandatory airtightness testing in North America. With the third version, the Toronto Green Standard (TGS) almost catches up with industry peers in Europe, Washington State, and British Columbia in requiring whole-building airtightness testing of Tier 2, 3, and 4 buildings. TGS works similarly to the B.C. Energy Step Code, and in 2022, Tier 2 will replace Tier 1, meaning mandatory testing is on the horizon. Since there is no set airtightness target threshold, it is widely expected the most progressive builders will want to fix relatively easy test goals.
While a standalone airtightness test can be beneficial in quantifying building performance and serving as an opportunity to identify deficiencies in the ABS, it is most effective when combined with an envelope commissioning strategy. The envelope commissioning process involves:
- thorough review of the details to ensure continuity and compatibility of an ABS and its components;
- development of a project-specific airtightness strategy that gets shared with the trades;
- targeted training for the installation of key component details coupled with mockup testing and site inspections; and
- partial as well as full-building airtightness test.
The resulting periodic site visits to inspect the ABS along with physical testing of its components inevitably leads to greater consistency, higher quality, and results in improved building efficiency, comfort, durability, and better indoor air quality (IAQ).
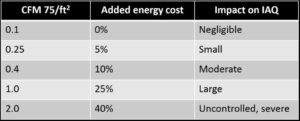
Image © Colin Genge of Retrotec
Why test?
It is well-known when buildings are more airtight, occupants experience greater comfort, IAQ is higher, durability increases, and liability is reduced for owners. The ultimate and quantifiable goal, though, is decreased energy consumption in the built environment.
An enclosure commissioning process is similar to a mechanical system commissioning process in that the enclosure is tested to qualitatively and quantifiably assess its integrity. If issues arise during the construction phase, changes are implemented to optimize assembly and performance of the ABS, leading to fewer future problems. Additionally, identifying and remediating deficiencies during the construction phase means the cost of these repairs is likely to be lower.
Current practices often produce inconsistent building enclosure detailing that can leave owners vulnerable to premature repairs due to condensation or moisture issues. Occupants are also affected, as they suffer from increased discomfort, street-level noise, and reduced air quality—all due to poor ABS detailing. Adding insult to injury, mechanical systems are typically designed to include a padded estimate for heat lost through the enclosure due to uncontrolled air leakage, leading to larger and possibly more expensive-than-necessary assemblies. Reducing uncontrolled air leakage lowers condensation risk and offers greater energy efficiency (Figure 1).
The benefits of adding more insulation in building enclosures are numerous, especially when the insulation layers are in intimate contact with the ABS. However, the benefits are squandered if there are gaps in the insulation or bypasses for air leakage. Thicker layers of insulation can leave a building vulnerable to unexpected and unwanted water vapour buildup driven by moisture-laden air leakage entering poorly connected ABS and getting into wall, soffit, or roof assemblies. Installing additional insulation to an envelope, even one that has been effective previously, can impact the location of the dewpoint in the assembly. If fuelled by an uncontrolled air leak, the condensation at the dewpoint can lead to significant moisture-related issues in the wall assembly.
Exhaust-only ventilation systems have been replaced by balanced, heat recovery systems in new construction, and these more expensive ventilation systems earn their keep if the building is airtight.
Test methods
The most widely adaptable test method is the newly released ASTM E3158-18, Standard Test Method for Measuring the Air Leakage Rate of a Large or Multizone Building. Unlike previous standards, ASTM E3158-18 gives the agency guidance for evaluation during colder conditions and guarded testing. The standard methodology can be applied to all typologies of buildings from low-rise, stacked townhomes to high-rise commercials.
ASTM E3158-18 also distinguishes between an Operational or ‘as-operated’ test and Building Envelope or ‘as-is’ tests. The former is used to assess the building in its natural or as-operated state, and the results are utilized as inputs in energy models.